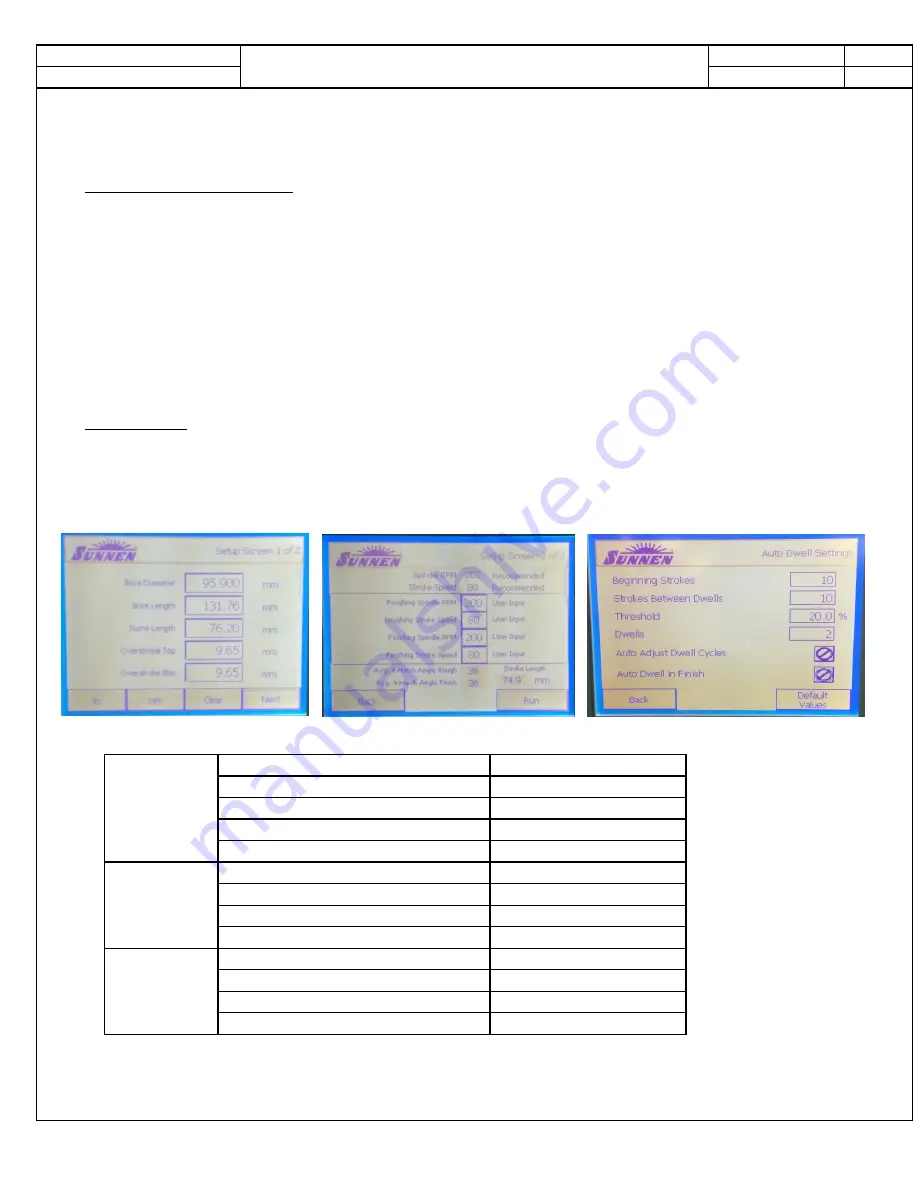
All operators should become familiar with the Sunnen SV‐10 Hone Operator Manual, safety precautions,
set up procedures, and operations of the SV‐10 Hone before honing engine blocks.
Required Parts and Equipment
1.
Sunnen SV‐10 Hone Machine
2.
Sunnen Honing Oil SHO965055 (55 gal.) / SHO965005 (5 gal.)
3.
Course Diamond Stones: Sunnen DHH6GMH85
4.
Plateau Brush: Sunnen DHHB6534 (DHHB7534 is an adequate substitute)
5 Sunnen Bore Gauge;
G
A
M‐2121
12" depth, 0.002mm resolution indicator dial bore gauge.
G
R
M‐2121
12" depth, 0.002mm resolution, with retractable indicator dial bore gauge.
G
A
M‐2121E 12" depth, 0.002mm resolution indicator bore gauge with digital readout.
G
R
M‐2121E 12" depth, 0.002mm resolution retractable indicator bore gauge with digital readout.
Machine Setup
Place the block in the SV‐10 honing machine with the front of the block facing left.
Set the stroke length to 3.0 " on the inch scale or 75 mm on the metric scale.
Set the Ratchet Feed setting to 1.
Manually set the tilting table height to 3/8" or 9.65mm.
Using the automated setup screens input the following parameters;
Bore Diameter
95.90mm
Bore Length
131.76mm
Stone Length
76.20mm
Over stroke Top
9.65mm
Over stroke Bottom
9.65mm
Roughing Spindle Speed RPM
200
Roughing Stroke Speed
80
Finishing Spindle Speed RPM
200
Finishing Stroke Speed
80
Beginning Strokes
10
Strokes Between Dwells
10
Threshold
20%
Dwells
2
These user input values should yield an average X‐hatch angle of 36° and a stroke length of 74.9 mm.
Section
4
Mar‐16
Sheet
8
Auto Dwell
Settings
Screen 1
Screen 2
Sunnen SV‐10
IIIH Hone Settings
Revision DRAFT
Summary of Contents for IIIH
Page 9: ...Section 3 New Engine Disassembly...
Page 20: ...Section 4 Main Oil Gallery Modifications and Honing...
Page 34: ...Section 5 Post Honing and Special Parts Cleaning...
Page 42: ...Section 6 Cylinder Head Pre Build Cleaning and Assembly...
Page 46: ...Section 7 Short Block Assembly and General Information...
Page 60: ...Section 8 Long Block Assembly...
Page 75: ...Section 9 Final Dress...
Page 89: ...Section 10 OHT Hardware...
Page 93: ...OHT3H 304 2 Pan Oil Modified Revision DRAFT OH Technologies Section 10 Mar 16 Sheet 4...