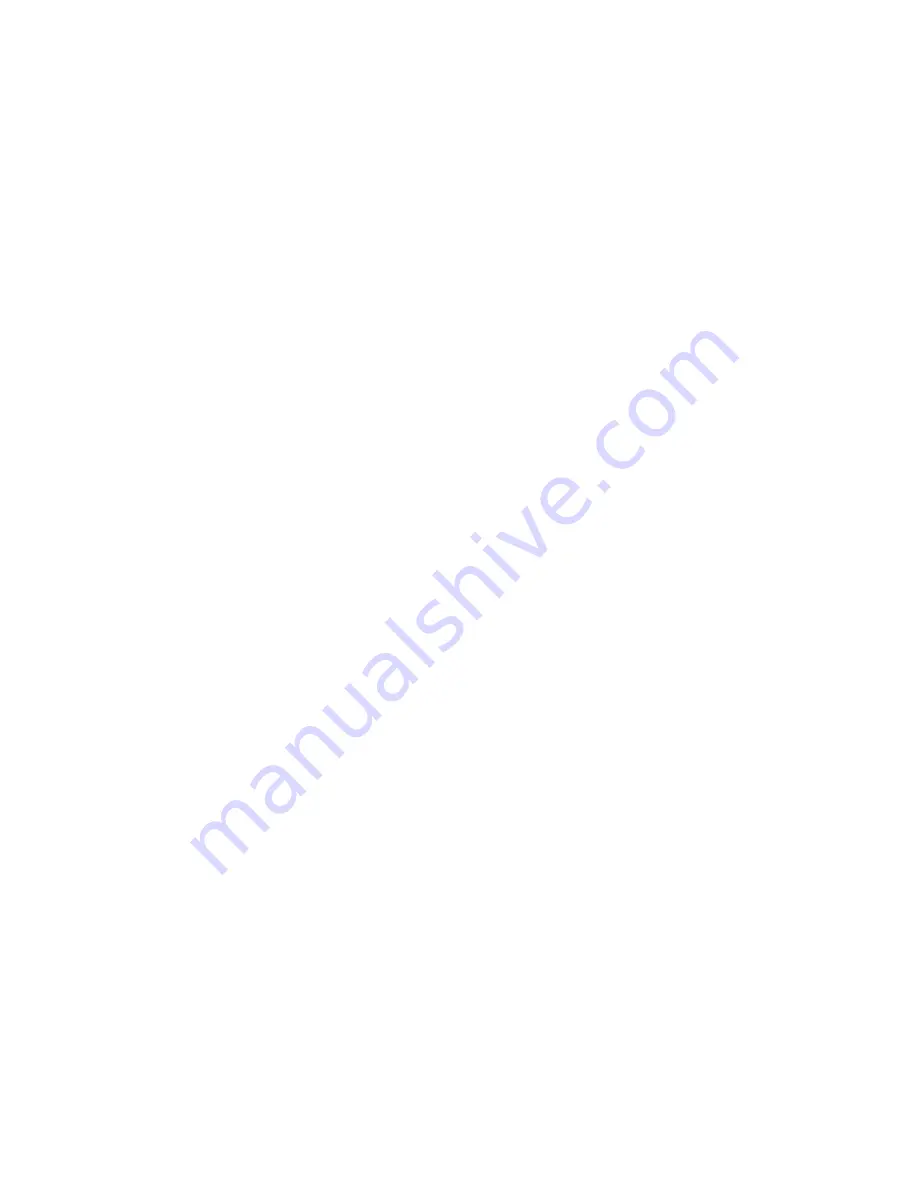
ChipBLASTER Inc
75
24.0. WARRANTY (Cont.):
24.3.8. This limited warranty shall cover alleged defects in materials and workmanship
about which ChipBLASTER receives notice within thirty (30) days of either the
discovery of the alleged defect or the expiration of the limited warranty period,
whichever is earlier. Any claim not made within this time shall be conclusively
deemed to have been waived by the purchaser.
24.3.9. ChipBLASTER warranty card must be completed by purchaser and returned to
ChipBLASTER within 30 days after installation of ChipBLASTER retrofits.
Procedures for Obtaining Technical Service or Warranty Service.
Repair or replacement under
this limited warranty can only be obtained by registering a warranty claim directly with ChipBLASTER.
To enable ChipBLASTER to respond to a request for technical assistance or a request for warranty
service, the purchaser must provide, at a minimum, the following information during the initial telephone
call: model and serial number of the equipment on which the ChipBLASTER retrofit was installed;
information regarding the installed ChipBLASTER retrofit; the date of purchase; the dealer or supplier
from whom the equipment was purchased; the nature of the problem or difficulty. A warranty claim
form can be obtained by contacting ChipBLASTER at 800-241-3163.
Limitation of Liability.
ChipBLASTER’s liability under this warranty is limited as set forth herein. This
limited warranty and the remedies set forth herein constitute the sole and exclusive remedy available to
the purchaser of ChipBLASTER™ retrofits covered by this limited warranty, and are in lieu of any or all
other remedies, whether based on statements or promises which are oral, written, express or implied,
and whether in contract, tort, equity or otherwise.
ChipBLASTER neither extends nor provides any warranty, expressed or implied, on any products not
manufactured by or sold by ChipBLASTER. Problems caused to ChipBLASTER™ retrofits used in
conjunction with ChipBLASTER™ equipment which are not either manufactured by ChipBLASTER or
manufactured to design specifications provided by ChipBLASTER and specifically approved by
ChipBLASTER in writing are not the responsibility of ChipBLASTER, either under this warranty, or
otherwise.
This warranty excludes all implied warranties of merchantability or fitness for particular purpose or any
purpose.
This warranty specifically excludes liability of ChipBLASTER for, “downtime,” loss of income and/or
consequential damages.
In no event will ChipBLASTER’s liability to the purchaser resulting from any claim or loss arising out of
a purchaser’s purchase of ChipBLASTER™ retrofits or the operation thereof exceed the purchase price
of the product manufactured or sold by ChipBLASTER
.
24.3