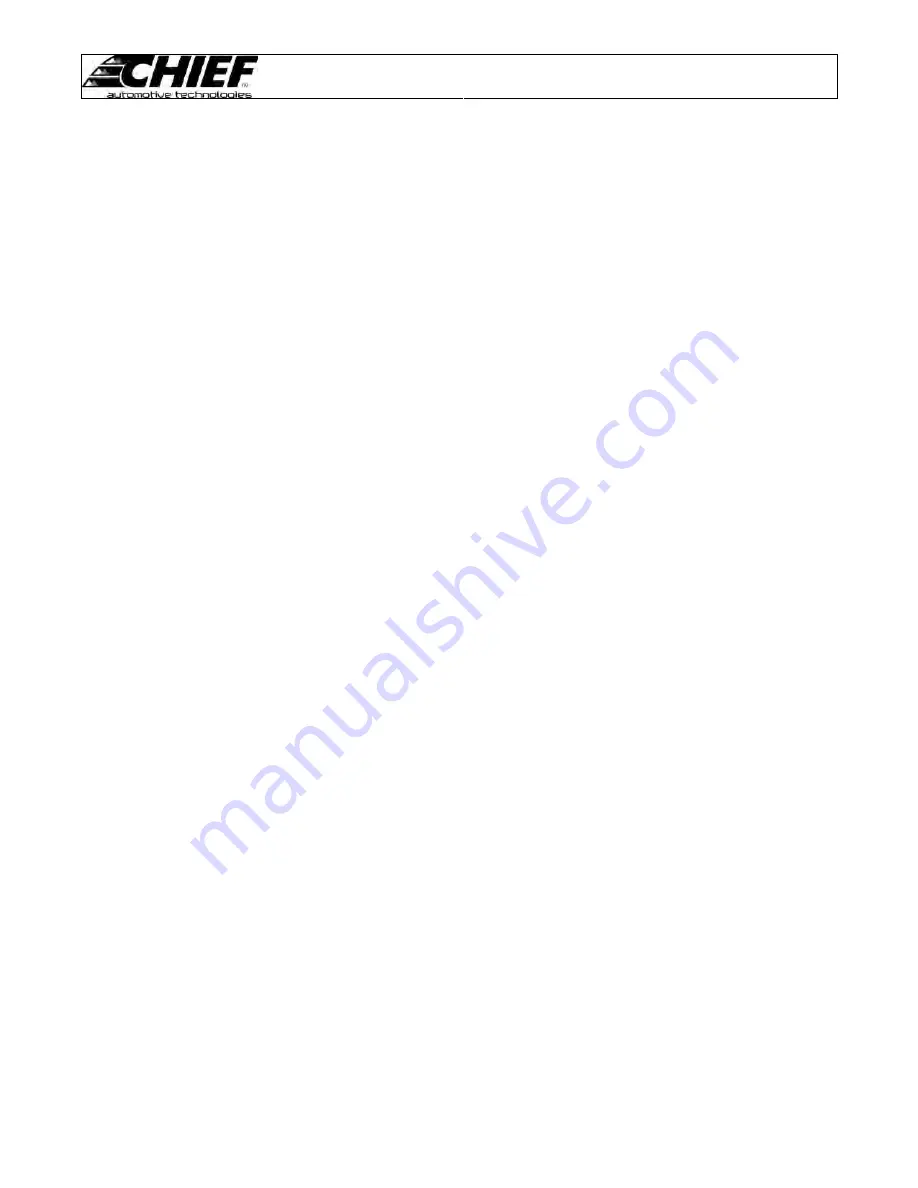
KAHUNA
Users Manual
12
The Owner/Employer:
•
Shall ensure that lift operators are qualified and that they are trained in the safe use and
operation of the lift using the manufacturer’s operating instructions; ALI/SM01-1, ALI
Lifting it Right safety manual; ALI/ST-90 ALI Safety Tips card; ANSI/ALI ALOIM-2000,
American National Standard for Automotive Lifts-Safety Requirements for Operation,
Inspection and Maintenance; ALI/WL Series, ALI Uniform Warning Label
Decals/Placards; and in the case of frame engaging lifts, ALI/LP-GUIDE, Vehicle Lifting
Points/Quick Reference Guide for Frame Engaging Lifts.
•
Shall establish procedures to periodically inspect the lift in accordance with the lift
manufacturer’s instructions or ANSI/ALI ALOIM-2000, American National Standard for
Automotive Lifts-Safety Requirements for Operation, Inspection and Maintenance; and
The Employer Shall ensure that lift inspectors are qualified and that they are adequately
trained in the inspection of the lift.
•
Shall establish procedures to periodically maintain the lift in accordance with the lift
manufacturer’s instructions or ANSI/ALI ALOIM-2000, American National Standard for
Automotive Lifts-Safety Requirements for Operation, Inspection and Maintenance; and
The Employer Shall ensure that lift maintenance personnel are qualified and that they
are adequately trained in the maintenance of the lift.
•
Shall maintain the periodic inspection and maintenance records recommended by the
manufacturer or ANSI/ALI ALOIM-2000, American National Standard for Automotive
Lifts-Safety Requirements for Operation, Inspection and Maintenance.
•
Shall display the lift manufacturer’s operating instructions; ALI/SM 93-1, ALI Lifting it
Right safety manual; ALI/ST-90 ALI Safety Tips card; ANSI/ALI ALOIM-2000,
American National Standard for Automotive Lifts-Safety Requirements for Operation,
Inspection and Maintenance; and in the case of frame engaging lifts, ALI/LP-GUIDE,
Vehicle Lifting Points/Quick Reference Guide for Frame Engaging Lifts; in a
conspicuous location in the lift area convenient to the operator.
•
Shall provide necessary lockout/tagout means for energy sources per ANSI Z244.1-
1982 (R1993), Safety Requirements for the Lockout/Tagout of Energy Sources, before
beginning any lift repairs.
•
Shall not modify the lift in any manner without the prior written consent of the
manufacturer.
Summary of Contents for Kahuna
Page 1: ...OWNERS MANUAL KAHUNA 2009 Chief Automotive Technologies USERS MANUAL ...
Page 2: ......
Page 6: ...KAHUNA Users Manual 4 GENERAL SPECIFICATIONS ...
Page 11: ...KAHUNA Users Manual 9 Controls ...
Page 30: ......
Page 31: ......