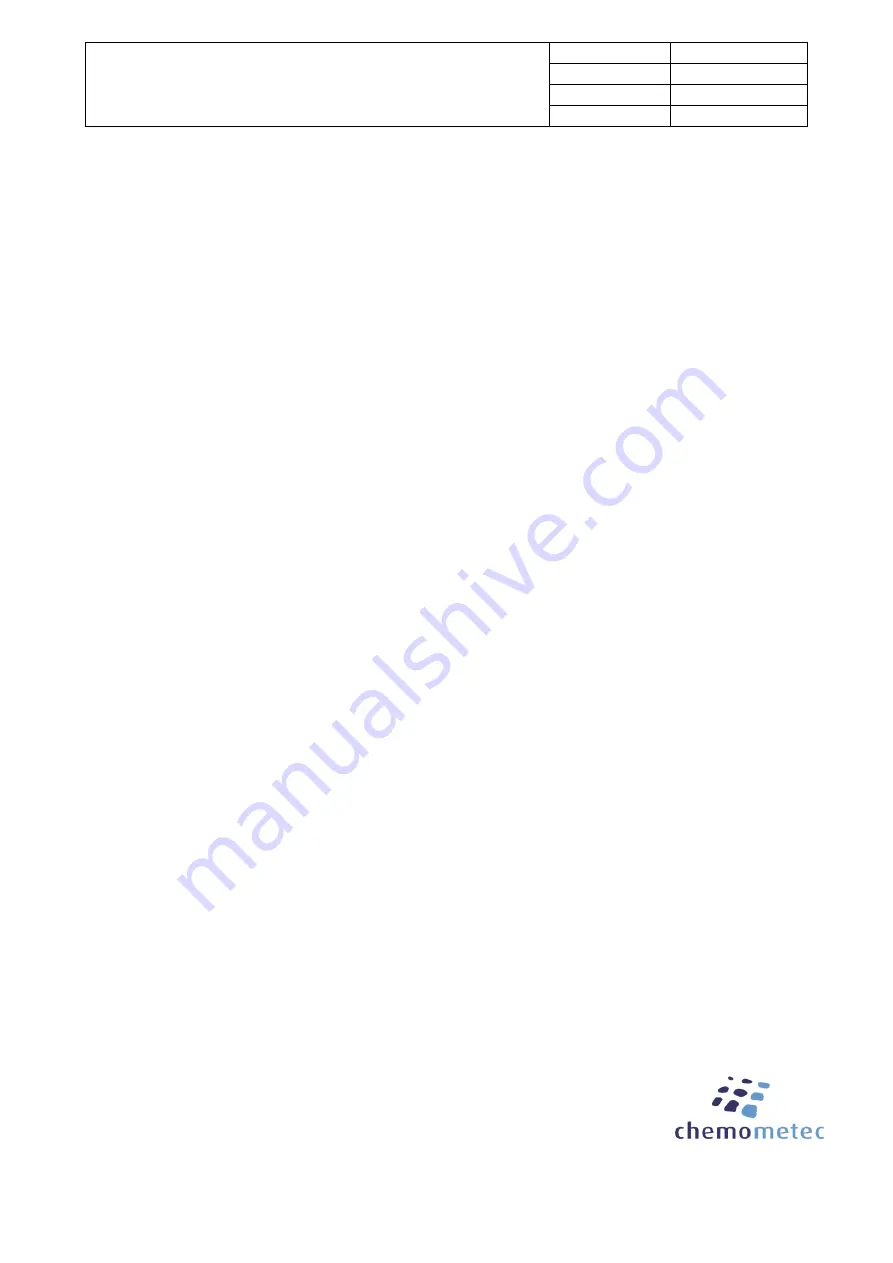
880-0030-76A QA Measures in Production of
ChemoMetec Cassettes
Doc. No. +Vers. 880-0030-76A v.4
Date
19-Jun-2018
Owner
IAP
Approved by
ELL
Template: 880-0017-79A v 4.1
Page
4
of
5
CONFIDENTIAL
Station 2: Cassette Assembly:
-
The dried flow parts are automatically transferred to the assembly line.
-
The flow part and the lid part are welded together.
-
The logo and lot number is printed on the cassette (100% test - checked by a vision system
on the assembly line).
-
The piston is inserted into the cassette (100% test - checked by a vision system on the
assembly line).
-
The cassette is put under pressure to test leakage (100% test - checked by a vision system on
the assembly line).
-
During production of the Cassette, a calibration parameter for every single cassette is
determined and printed on the cassette as a dot code. The dot code specifies the precise
depth of the measurement chamber of the cassette. If the depth is outside the range of 90-
110 µm the cassette is discarded (100% test - checked by a vision system on the assembly
line).
-
The dot code is read and decoded by the NucleoCounter® instrument during analysis and the
volume analyzed is determined by multiplying the imaged area with the depth of the
measurement area. The imaged area is only dependent on the optics of the instrument.
Therefore, the area is constant and specific for each instrument. The dot code must be
correctly placed and readable (100% test - checked by a vision system on the assembly line).
-
Cassettes that fail any of the inspection steps are discarded automatically at the end of the
assembly line. If three cassettes fail sequentially the assembly line stop automatically. The
number of errors in each production lot is systematically monitored and the trend is followed
closely.
Station 3: Bagging:
-
The correct number of cassettes is inserted into each bag (100% test
–
by weight).
-
An anti-moisture bag is inserted into each bag (100% test
–
by weight).
-
The label, which contains lot number and expiration date, is correctly positioned on the bag,
(100% test - visually inspected).
Station 4: Packaging:
-
Check that all printed labels are correct (100% test - visually inspected).
-
Repackage and re-label bags that have been discarded.
-
Pack bags into boxes containing 10 bags.
-
The label is correctly positioned on the box, which contains lot number and expiration date
(100% test - visually inspected). All cassette lots are composed of one or more sub-lots. Each
production day represents a sub-lot. The sub-lots are denoted A to G, and this sub-lot letter
is printed on the box-label.
-
The finished cassette lot is placed in quarantine storage until they have been QC tested.
Quality Control During Production:
-
Functionality tests of the cassettes are performed every hour during production. The results
of these tests are registered in the production log.
Page 23 of 127
Summary of Contents for NucleoCounter NC-202
Page 1: ...997 0005 NucleoCounter NC 202 Document Compilation V 1 0 Page 1 of 127...
Page 14: ...Page 14 of 127...
Page 15: ...Page 15 of 127...
Page 16: ...Page 16 of 127...