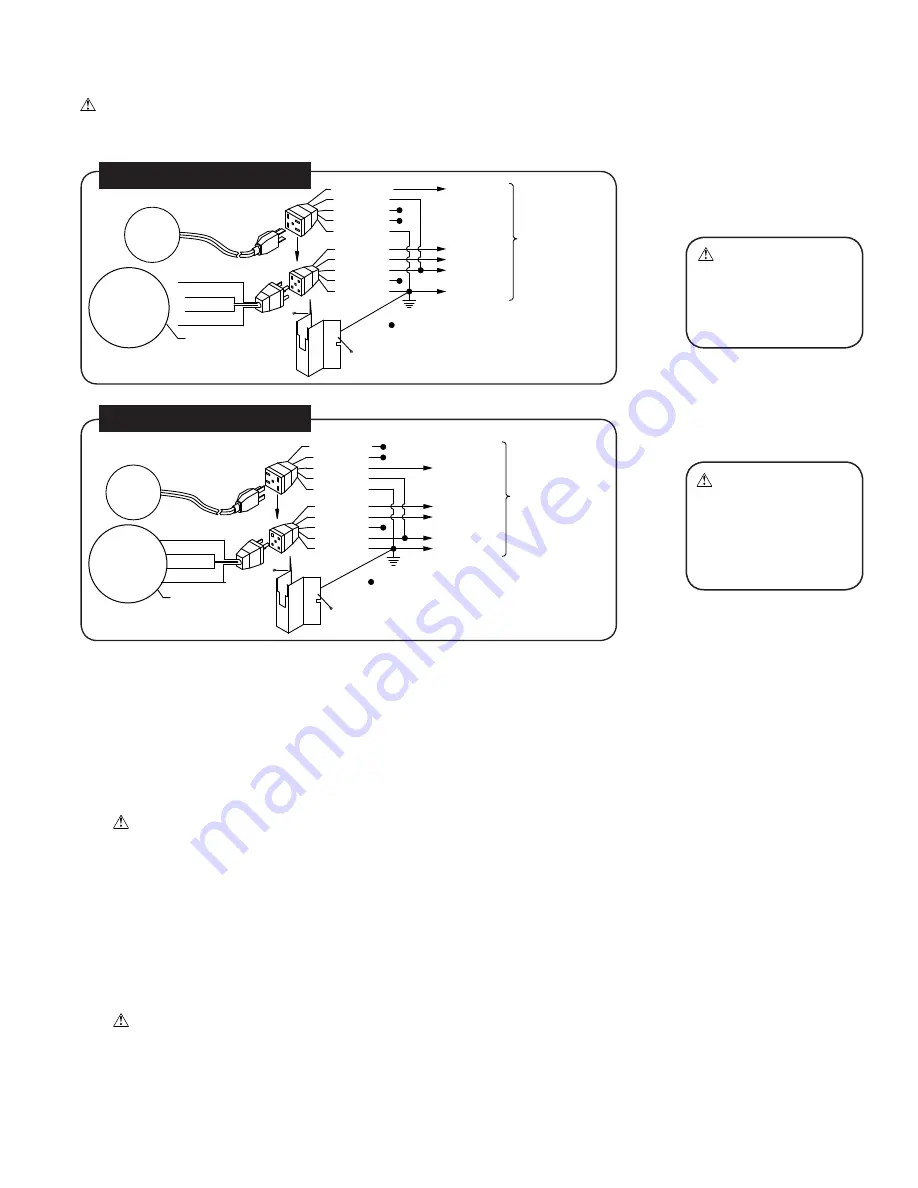
110524-1
3
Contractor Model 4000CRLD4
Note:
This unit comes with the motor, pulley, and thermostat control box installed. The unit is factory wired and for 120V power.
The supply power should be adequately protected against overloads and short circuits.
Supply Power to Unit
1. A disconnect switch (not included) should be installed near the unit.
2. Run a 2 conductor wire with ground from the power source to the disconnect switch box.
CAUTION: Make sure to use correctly sized wire and follow all local electrical codes.
3. Remove the screws securing the electrical junction box in the unit to gain access to the power lead wires.
4. Connect the power leads and ground wire from the unit junction box to the disconnect switch.
5. Reinstall the junction box to the unit.
Wall Thermostat Installation
1.
Find a suitable location for the wall thermostat (away from sources of heat, sunlight, or ventilation, and between 4 and 6 feet
from the floor). The thermostat may be mounted to a standard electrical box.
2. Route an insulated three or four-conductor thermostat cable (or similar) from the Control Box inside the cooler to the
thermostat electrical box. This cable is not supplied.
WARNING: The thermostat cable should not be routed next to or enter the cabinet through the same inlet as the
power supply wire.
3.
Connect the thermostat wires to the terminals on the back of the wall control and to the terminals located on the left side of the
control box in the unit. Make sure to follow the color code found next to each terminal.
Blue/Black
White
Brown
Orange
Green
Green
Orange
White
Red
Black
PUMP
HIGH
LOW
COMMON
GROUND
= WIRE NUT
HIGH
LOW
COMMON
GROUND
Black
Green
White
Red
BLOWER MOTOR
PUMP
MOTOR
TO SWITCH
120 VOLT
COMMON
PUMP
MOTOR
BLOWER MOTOR
Red
Orange
Green
Black
GROUND
COMMON
LOW
HIGH
= WIRE NUT
GROUND
LOW
HIGH
PUMP
Black
Red
White
Orange
Green
Green
Orange
Brown
White
Blue/Black
TO SWITCH
240 VOLT
CAUTION:
Recepta-
cles in junction box are
only for Motor and pump.
Do not plug anything
else into receptacle.
WARNING:
Ensure
cooler cabinet is proper-
ly grounded to a suitable
ground connection for
maximum safety and
protection of equipment.
6. Reinstall junction box to cooler cabinet.
7. Plug motor and pump plugs into receptacles.
8. Follow switch electrical instructions for connecting the four conductors and power leads to switch.
Warning: Pump cord must be secured in retaining clip to prevent contact with water.
ELECTRICAL WIRING DIAGRAMS - STANDARD MODEL 4000RLD4
Summary of Contents for 4000 CRLD4
Page 11: ...110524 1 11 PARTS DRAWING ...