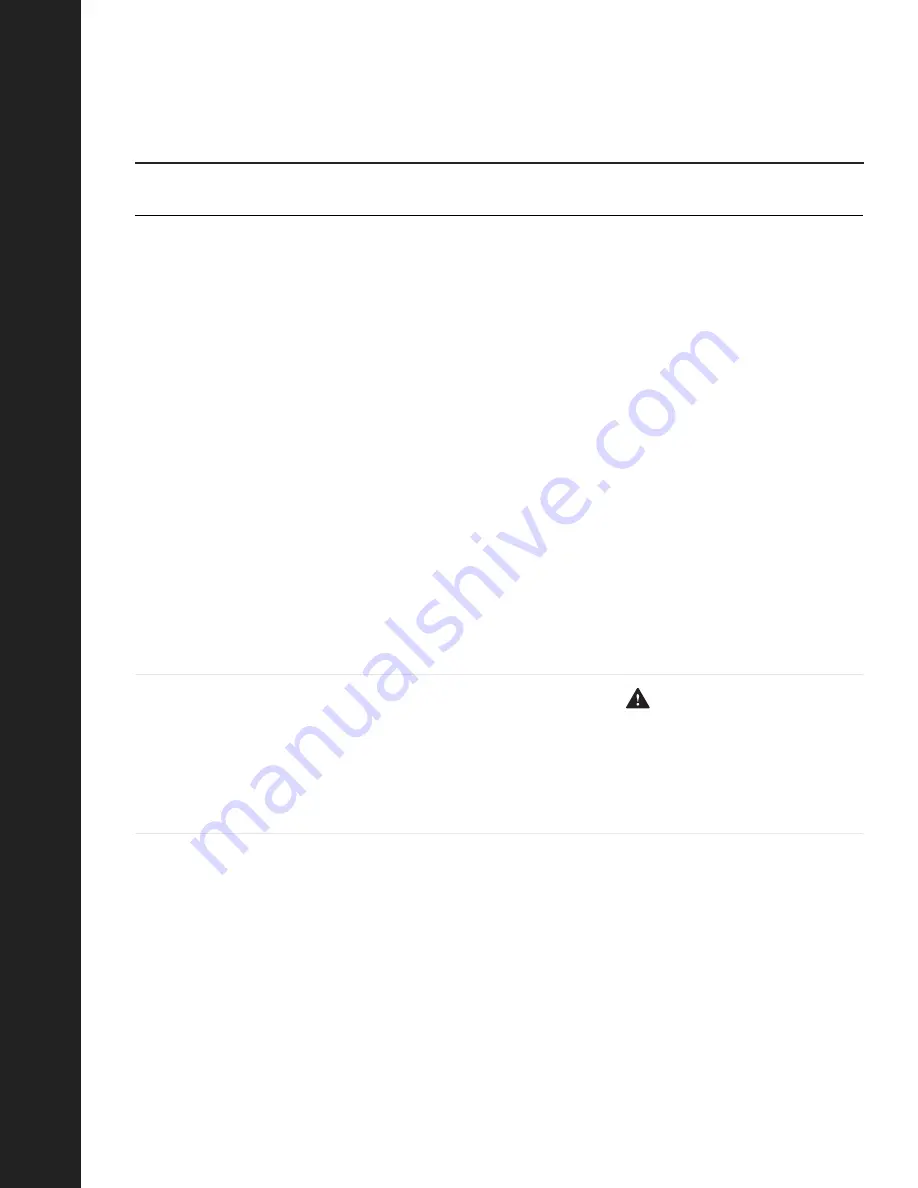
20
TrueComfort System
Troubleshooting
continued
PRObLEM
LIkELY CAUSE
REMEDY
Low production, insulation drips
out the end of the hose. Not
getting proper arc length.
Too many tight bends or a kink in
the hose.
When properly setup, the hose should
be as straight as possible to ensure a
smooth flow of material. Straighten out
any tight bends or kinks in the hose.
Worn seals in airlock.
Replace seals in airlock section of the
base. Minimum psi = 2.0.
Hose is too long.
The machine is supplied with 100'
foot mark of hose. If additional hose
length was added, remove hose added
beyond 100' foot mark.
Hose connections may be leaking.
Check the connection between the
2.5" hose outlet and quick hose
connect. Minimum psi = 2.0. It may be
necessary to replace one or all of the
components to correct air leakage.
Insulation drips out the end
of the hose. Not getting proper
arc length.
Foreign object in airlock or hose.
Disconnect power cord at
the machine. Remove hopper and
insulation from the base. Visually
inspect agitator and airlock for any
foreign objects. Also, check hose for
any foreign objects.
T
roubleshooting
Summary of Contents for TrueComfort
Page 18: ...18 Electrical Diagram TrueComfort System Electrical Diagram ...
Page 30: ...30 Notes ...
Page 31: ...31 Notes ...