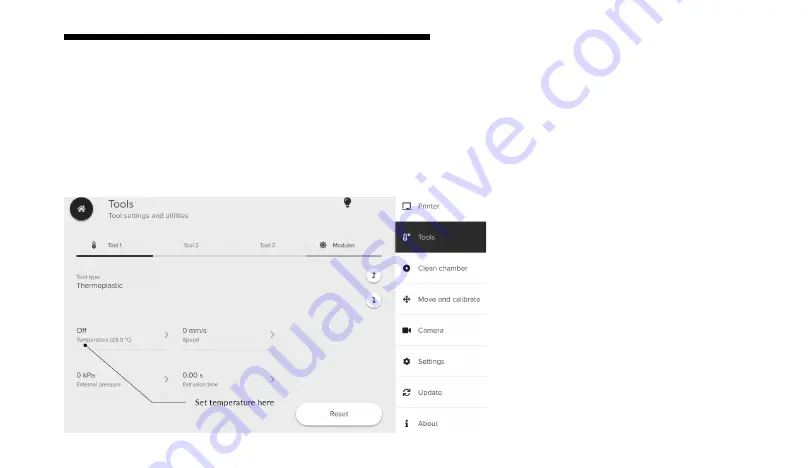
15
04 Getting started
4.2 Heating the Thermoplastic Printhead
NOTE:
The steps under this section will test the temperature functionality of your Thermoplastic Printhead. It is only necessary to follow
these steps once, after receiving your new printhead.
1. Assemble and attach the Thermoplastic Printhead (Section 4.1).
2. Go to the Utilities Menu and then the Tools submenu.
3. Set the printhead temperature (Figure 5).
Figure 5:
Presetting temperature for the
Thermoplastic Printhead.
Summary of Contents for BIO X
Page 1: ...BIO X Thermoplastic Printhead User Manual...
Page 2: ......
Page 4: ......
Page 5: ...1 Package contents 01...
Page 7: ...3 Technical specifications 02...
Page 11: ...7 Safety information 03...
Page 14: ...10...
Page 15: ...11 Getting started 04...
Page 25: ...21 04 Getting started Figure 8 Loading the Thermoplastic Print head with granulate A B C...
Page 37: ...33 Cleaning 05...
Page 40: ...36...
Page 41: ...37 Printing optimization 06...
Page 44: ...40...
Page 45: ...41 Relevant G code commands 07...
Page 48: ...44...
Page 49: ...45 Frequently asked questions 08...
Page 54: ...50...
Page 55: ...51 Maintenance 09...
Page 57: ...53 Appendix A Consumables...
Page 60: ...www cellink com...