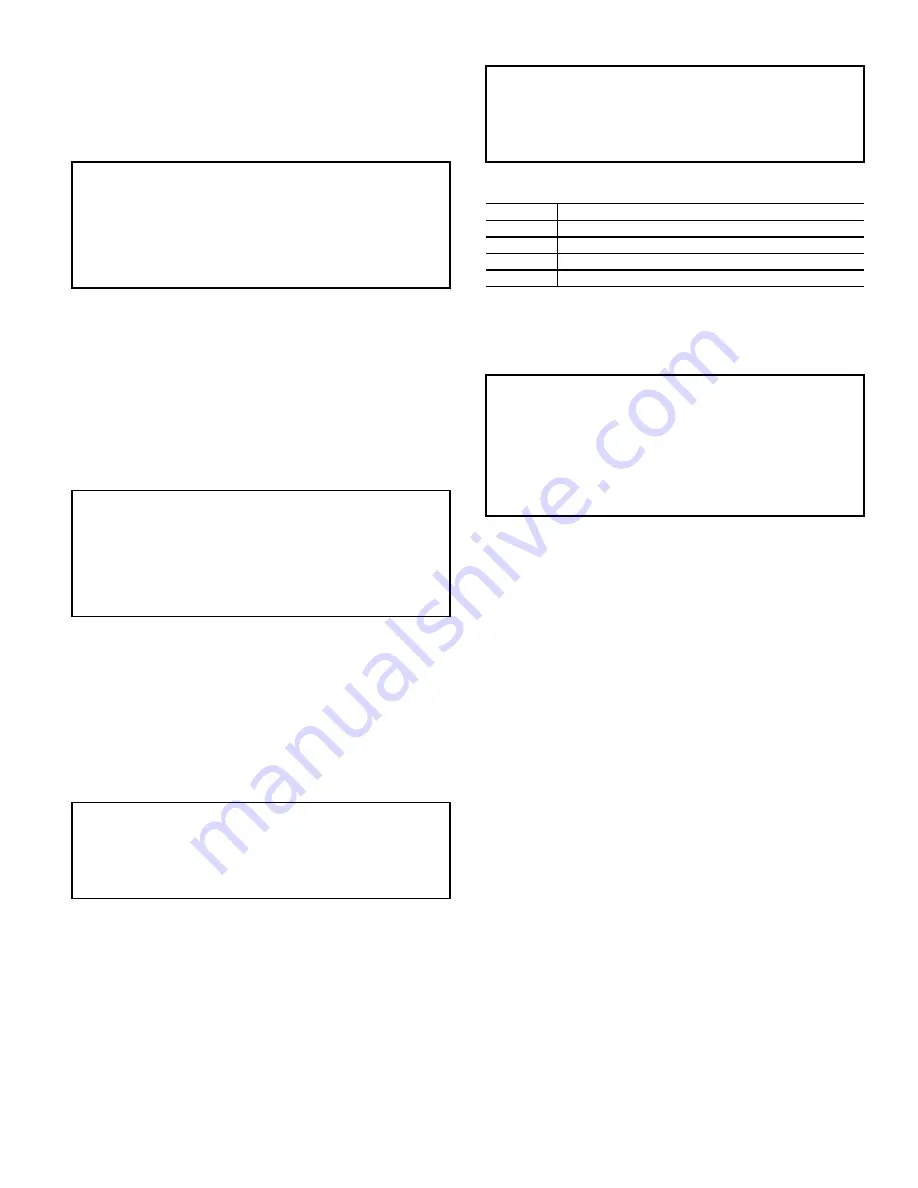
29
Sensor and Controller Tests
SENSOR ALARM TEST
The sensor alarm test checks a sensor’s ability to signal an
alarm state. This test requires the use of a field-provided SD-
MAG test magnet.
SENSOR ALARM TEST PROCEDURE
1. Hold the test magnet where indicated on the side of the
sensor housing for seven seconds.
2. Verify that the sensor’s Alarm LED turns on.
3. Reset the sensor by holding the test magnet against the
sensor housing for two seconds.
4. Verify that the sensor’s Alarm LED turns off.
CONTROLLER ALARM TEST
The controller alarm test checks the controller’s ability to initi-
ate and indicate an alarm state.
CONTROLLER ALARM TEST PROCEDURE
1. Press the controller’s test/reset switch for seven seconds.
2. Verify that the controller’s Alarm LED turns on.
3. Reset the sensor by pressing the test/reset switch for
two seconds.
4. Verify that the controller’s Alarm LED turns off.
DIRTY CONTROLLER TEST
The dirty controller test checks the controller’s ability to initi-
ate a dirty sensor test and indicate its results.
DIRTY CONTROLLER TEST PROCEDURE
• Press the controller’s test/reset switch for two seconds.
• Verify that the controller’s Trouble LED flashes.
DIRTY SENSOR TEST
The dirty sensor test provides an indication of the sensor’s abil-
ity to compensate for gradual environmental changes. A sensor
that can no longer compensate for environmental changes is
considered 100% dirty and requires cleaning or replacing. You
must use a field provided SD-MAG test magnet to initiate a
sensor dirty test. The sensor’s Dirty LED indicates the results
of the dirty test as shown in Table 6.
DIRTY SENSOR TEST PROCEDURE
1. Hold the test magnet where indicated on the side of the
sensor housing for two seconds.
2. Verify that the sensor’s Dirty LED flashes.
CHANGING THE DIRTY SENSOR TEST
By default, the dirty sensor test results are indicated by:
• The sensor’s Dirty LED flashing.
• The controller’s Trouble LED flashing.
• The controller’s supervision relay contacts toggle.
The operation of a sensor’s dirty test can be changed so that the
controller’s supervision relay is not used to indicate test results.
When two detectors are connected to a controller, sensor dirty
test operation on both sensors must be configured to operate in
the same manner.
TO CONFIGURE THE DIRTY SENSOR TEST OPERATION
1. Hold the test magnet where indicated on the side of the
sensor housing for approximately 60 seconds until the sen-
sor’s Alarm LED turns on and its Dirty LED flashes twice.
2. Reset the sensor by removing the test magnet and then
holding it against the sensor housing again for approxi-
mately 2 seconds until the sensor’s Alarm LED turns off.
REMOTE STATION TEST
The remote station alarm test checks a test/reset station’s abili-
ty to initiate and indicate an alarm state.
SD-TRK4 REMOTE ALARM TEST PROCEDURE
1. Turn the key switch to the RESET/TEST position for
seven seconds.
2. Verify that the test/reset station’s Alarm LED turns on.
3. Reset the sensor by turning the key switch to the RESET/
TEST position for two seconds.
4. Verify that the test/reset station’s Alarm LED turns off.
REMOTE TEST/RESET STATION DIRTY SENSOR TEST
The test/reset station dirty sensor test checks the test/reset sta-
tion’s ability to initiate a sensor dirty test and indicate the re-
sults. It must be wired to the controller as shown in Fig. 36 and
configured to operate the controller’s supervision relay. For
more information, see “Changing the Dirty Sensor Test.”
IMPORTANT: Failure to follow this NOTICE may result in
an unnecessary evacuation of the facility.
This test places the duct detector into the alarm state.
Unless part of the test, disconnect all auxiliary equipment
from the controller before performing the test. If the duct
detector is connected to a fire alarm system, notify the
proper authorities before performing the test.
IMPORTANT: Failure to follow this NOTICE may result in
an unnecessary evacuation of the facility.
This test places the duct detector into the alarm state.
Unless part of the test, disconnect all auxiliary equipment
from the controller before performing the test. If the duct
detector is connected to a fire alarm system, notify the
proper authorities before performing the test.
IMPORTANT: Failure to follow this NOTICE may result in
an unnecessary evacuation of the facility.
Pressing the controller’s test/reset switch for longer than
seven seconds will put the duct detector into the alarm state
and activate all automatic alarm responses.
IMPORTANT: Failure to follow this NOTICE may result in
an unnecessary evacuation of the facility.
Holding the test magnet against the sensor housing for
more than seven seconds will put the duct detector into the
alarm state and activate all automatic alarm responses.
Table 6 — Dirty LED Test
FLASHES
DESCRIPTION
1
0-25% dirty. (Typical of a newly installed detector)
2
25-50% dirty
3
51-75% dirty
4
76-99% dirty
IMPORTANT: Failure to follow this NOTICE may result in
an unnecessary evacuation of the facility.
Changing the dirty sensor test operation will put the detec-
tor into the alarm state and activate all automatic alarm
responses. Before changing dirty sensor test operation, dis-
connect all auxiliary equipment from the controller and
notify the proper authorities if connected to a fire alarm
system.
Summary of Contents for WeatherMaster Puron 48HC D17
Page 18: ...18 COOLING CHARGING CHARTS Fig 22 Cooling Charging Chart 15 Ton ...
Page 19: ...19 Fig 23 Cooling Charging Chart 17 5 Ton ...
Page 20: ...20 Fig 24 Cooling Charging Chart 20 Ton ...
Page 21: ...21 Fig 25 Cooling Charging Chart 25 Ton ...
Page 37: ...37 Fig 48 Unit Control Box IGC Location IGC Board IGC Board Side view Front view ...
Page 40: ...40 Fig 51 Typical IGC Wiring Diagram ...
Page 46: ...46 Fig 57 RTU Open Overlay for Economizer Wiring ...
Page 47: ...47 Fig 58 VFD Overlay for W2770 Controller Wiring ...
Page 84: ...84 Fig B 48HC D17 D28 Control Diagram 208 230 3 60 460 575 3 60 ...
Page 85: ...85 Fig C 48HC D17 D28 Power Diagram 208 230 3 60 ...
Page 86: ...86 Fig D 48HC D17 D28 Power Diagram 460 3 60 ...
Page 87: ...87 Fig E 48HC D17 D28 Power Diagram 575 3 60 ...
Page 88: ...88 Fig F 48HC D17 D28 Control Diagram with Humidi MiZer System ...
Page 89: ...89 Fig G 48HC D17 D28 Power Diagram 208 230 3 60 with Humidi MiZer System ...
Page 90: ...90 Fig H 48HC D17 D28 Power Diagram 460 3 60 with Humidi MiZer System ...
Page 91: ...91 Fig I 48HC D17 D28 Power Diagram 575 3 60 with Humidi MiZer System ...
Page 92: ...92 Fig J PremierLink System Control Wiring Diagram 50HE500891 F ...
Page 93: ...93 Fig K PremierLink System Control Wiring Diagram with Humidi MiZer System ...
Page 94: ...94 Fig L RTU OPEN Wiring Diagram ...
Page 95: ...95 Fig M RTU OPEN Wiring Diagram with Humidi MiZer System ...
Page 97: ......