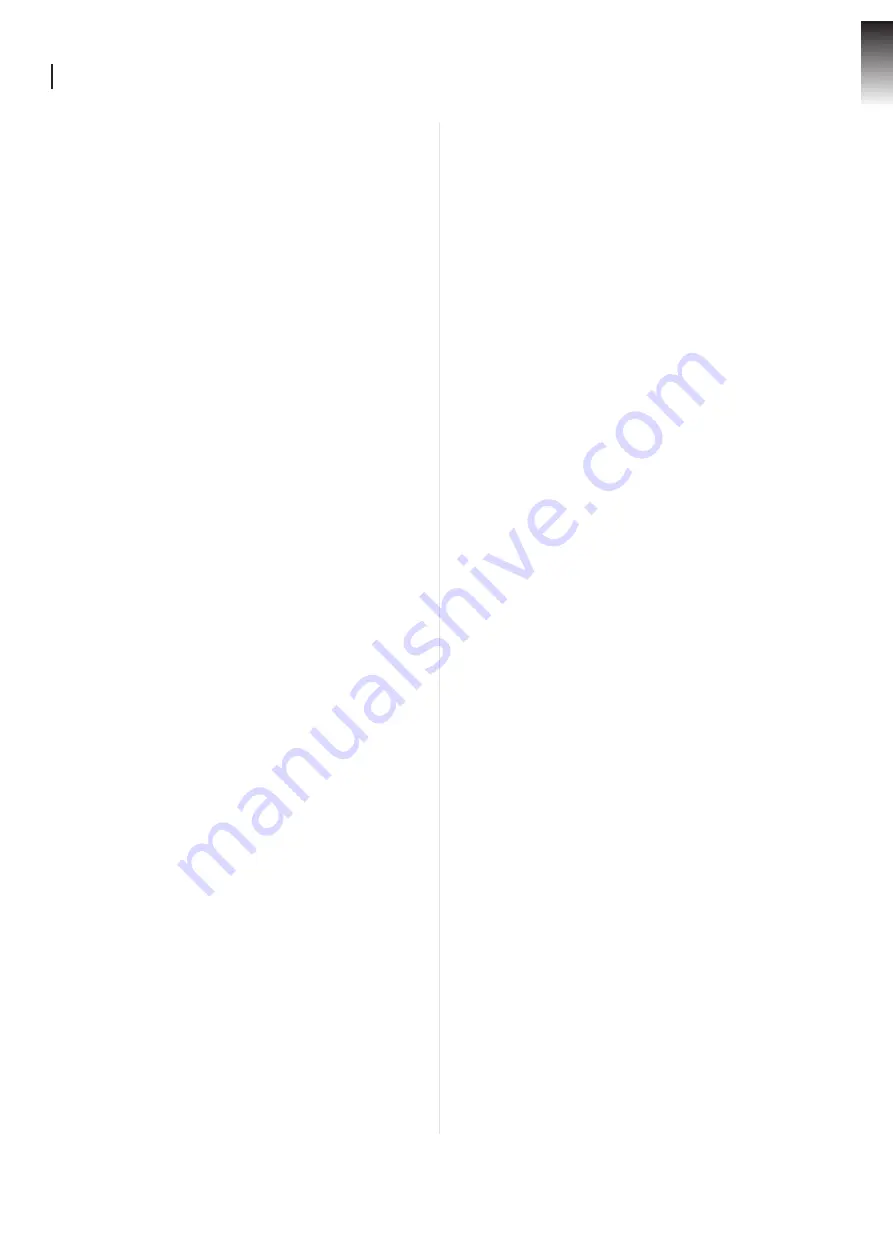
exposed while charging, recovering or purging the system;
That there is continuity of earth bonding.
7.Repairs to sealed components
1)During repairs to sealed components, all electrical
supplies shall be disconnected from the equipment being
worked upon prior to any removal of sealed covers, etc. If it
isabsolutely necessary to have an electrical supply to
equipment during servicing, then a permanently operating
form of leak detection shall be located at the most critical
point to warn of a potentially hazardous situation.
2)Particular attention shall be paid to the following to ensure
that by working on electrical components, the casing is not
altered in such a way that the level of protection is affected.
This shall include damage to cables, excessive number of
connections, terminals not made to original specification,
damage to seals, incorrect fitting of glands, etc.
Ensure that apparatus is mounted securely.
Ensure that seals or sealing materials have not degraded
such that they no longer serve the purpose of preventing the
ingress of flammable atmospheres. Replacement parts shall
be in accordance with the manufacturer's specifications.
NOTE: The use of silicon sealant may inhibit the
effectiveness of some types of leak detection
equipment. Intrinsically safe components do not have to
be isolated prior to working on them.
8.Repair to intrinsically safe components
Do not apply any permanent inductive or capacitance
loads to the circuit without ensuring that this will not
exceed the permissible voltage and current permitted for
the equipment in use. Intrinsically safe components are
the only types that can be worked on while live in the
presence of a flammable atmosphere. The test apparatus
shall be at the correct rating. Replace components only
with parts specified by the manufacturer. Other parts may
result in the ignition of refrigerant in the atmosphere from
a leak.
9.Cabling
Check that cabling will not be subject to wear, corrosion,
excessive pressure, vibration, sharp edges or any other
adverse environmental effects. The check shall also take
into account the effects of aging or continual vibration
from sources such as compressors or fans.
10.Detection of flammable refrigerants
Under no circumstances shall potential sources of ignition
be used in the searching for or detection of refrigerant
leaks. A halide torch (or any other detector using a naked
flame) shall not be used.
11.Leak detection methods
he following leak detection methods are deemed
acceptable for systems containing flammable refrigerants.
Electronic leak detectors shall be used to detect flammable
refrigerants, but the sensitivity may not be adequate, or
Warnings(for using R290/R32 refrigerant only)
6
may need re-calibration. (Detection equipment shall be
calibrated in a refrigerant-free area.) Ensure that the
detector is not a potential source of ignition and is suitable
for the refrigerant used. Leak detection equipment shall be
set at a percentage of the LFL of the refrigerant and shall be
calibrated to the refrigerant employed and the appropriate
percentage of gas (25 % maximum) is confirmed. Leak
detection fluids are suitable for use with most refrigerants
but the use of detergents containing chlorine shall be
avoided as the chlorine may react with the refrigerant and
corrode the copper pipe-work. If a leak is suspected, all
naked flames shall be removed/ extinguished. If a leakage
of refrigerant is found which requires brazing, all of the
refrigerant shall be recovered from the system, or isolated
(by means of shut off valves) in a part of the system remote
from the leak. Oxygen free nitrogen (OFN) shall then be
purged through the system both before and during the
brazing process.
12.Removal and evacuation
When breaking into the refrigerant circuit to make repairs
or for any other purpose conventional procedures shall be
used. However, it is important that best practice is followed
since flammability is a consideration. The following
procedure shall be adhered to:
Remove refrigerant;
Purge the circuit with inert gas;
Evacuate;
Purge again with inert gas;
Open the circuit by cutting or brazing.
The refrigerant charge shall be recovered into the correct
recovery cylinders. The system shall be flushed with OFN
to render the unit safe. This process may need to be
repeated several times. Compressed air or oxygen shall
not be used for this task.
Flushing shall be achieved by breaking the vacuum in the
system with OFN and continuing to fill until the working
pressure is achieved, then venting to atmosphere, and
finally pulling down to a vacuum. This process shall be
repeated until no refrigerant is within the system. When
the final OFN charge is used, the system shall be vented
down to atmospheric pressure to enable work to take
place. This operation is absolutely vital if brazing
operations on the pipe-work are to take place.
Ensure that the outlet for the vacuum pump is not close to
any ignition sources and there is ventilation available.
13.Charging procedures
In addition to conventional charging procedures, the
following requirements shall be followed.
Ensure that contamination of different refrigerants does
not occur when using charging equipment. Hoses or lines
shall be as short as possible to minimise the amount of
refrigerant contained in them.
Cylinders shall be kept upright.
Ensure that the refrigeration system is earthed prior to
charging the system with refrigerant.
Label the system when charging is complete (if not already).
GB