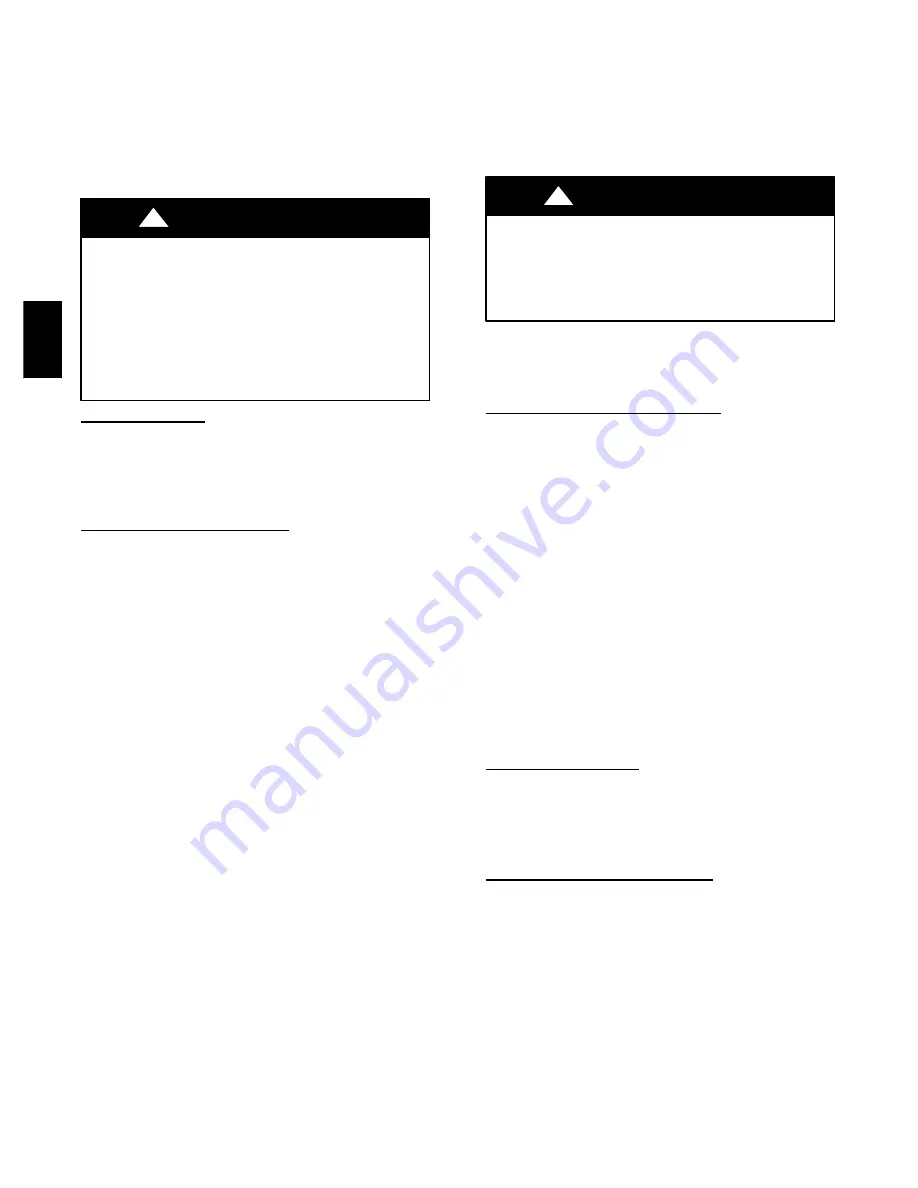
14
at 0.65 specific gravity, or propane gas with a heating
value of 2500 Btu/ft
3
at 1.5 specific gravity.
S
For elevations above 2000 ft, reduce input 4% for each
1000 ft above sea level. For example at 2500 ft. a 10%
total derate is required.
S
When the gas supply being used has a different heating
value or specific gravity, refer to national and local codes,
or contact your distributor to determine the required
orifice size.
UNIT DAMAGE HAZARD
Failure to follow this caution may result in reduced unit and/or
component life.
Do Not
redrill an orifice. Improper drilling (burrs,
out--of--round holes, etc.) can cause excessive burner noise
and misdirection of burner flame. If orifice hole appears
damaged or it is suspected to have been redrilled, check orifice
hole with a numbered drill bit of correct size.
!
CAUTION
ADJUST GAS INPUT
The gas input to the unit is determined by measuring the gas flow
at the meter or by measuring the manifold pressure. Measuring the
gas flow at the meter is recommended for natural gas units. The
manifold pressure must be measured to determine the input of
propane gas units.
Measure Gas Flow (Natural Gas Units)
Minor adjustment to the gas flow can be made by changing the
manifold pressure. The manifold pressure must be maintained
between 3.4 and 3.6 in. wc.
If larger adjustments are required, change main burner orifices
following the recommendations of national and local codes.
NOTE
: All other appliances that use the same meter must be turned
off when gas flow is measured at the meter.
Proceed as follows:
1. Turn off gas supply to unit.
2. Remove pipe plug on manifold (See Fig. 13) and connect
manometer. Turn on gas supply to unit.
3. Record number of seconds for gas meter test dial to make one
revolution.
4. Divide number of seconds in Step 3 into 3600 (number of
seconds in one hr).
5. Multiply result of Step 4 by the number of cubic feet (cu ft)
shown for one revolution of test dial to obtain cubic feet (cu
ft) of gas flow per hour.
6. Multiply result of Step 5 by Btu heating value of gas to
obtain total measured input in Btuh. Compare this value with
heating input shown in Table 3 (Consult the local gas
supplier if the heating value of gas is not known).
EXAMPLE: Assume that the size of test dial is 1 cu ft, one
revolution takes 32 sec, and the heating value of the gas is 1050
Btu/ft
3
. Proceed as follows:
1. 32 sec. to complete one revolution.
2. 3600
÷
32 = 112.5.
3. 112.5 x 1 =112.5 ft
3
of gas flow/hr.
4. 112.5 x 1050 = 118,125 Btuh input.
If the desired gas input is 115,000 Btuh, only a minor change in the
manifold pressure is required.
Observe manifold pressure and proceed as follows to adjust gas
input:
1. Remove cover screw over regulator adjustment screw on gas
valve.
2. Turn regulator adjustment screw clockwise to increase gas
input, or turn regulator adjustment screw counterclockwise
to decrease input. Manifold pressure must be between 3.4
and 3.6 in. wc.
FIRE AND UNIT DAMAGE HAZARD
Failure to follow this warning could result in personal injury
or death and/or property damage.
Unsafe operation of the unit may result if manifold pressure is
outside this range.
!
WARNING
3. Replace cover screw cap on gas valve.
4. Turn off gas supply to unit. Remove manometer from
pressure tap and replace pipe plug on gas valve. Turn on gas
to unit and check for leaks.
Measure Manifold Pressure (Propane Units)
The main burner orifices on a propane gas unit are sized for the unit
rated input when the manifold pressure reading matches the level
specified in Table 3.
Proceed as follows to adjust gas input on a propane gas unit:
1. Turn off gas to unit.
2. Remove pipe plug on manifold and connect manometer (See
Fig. 13).
3. Turn on gas to unit.
4. Remove cover screw over regulator adjustment screw on gas
valve.
5. Adjust regulator adjustment screw to the correct manifold
pressure, as specified in Table 3. Turn adjusting screw
clockwise to increase manifold pressure, or turn adjusting
screw counterclockwise to decrease manifold pressure.
6. Replace cover screw.
7. Turn off gas to unit. Remove manometer from pressure tap.
Replace pipe plug on gas valve, then turn on gas to unit.
Check for leaks.
CHECK BURNER FLAME
With burner access panel removed, observe the unit heating
operation. Watch the burner flames to see if they are light blue and
soft in appearance, and that the flames are approximately the same
for each burner. Propane will have blue flame (See Fig. 14). Refer
to the Maintenance section for information on burner removal.
AIRFLOW AND TEMPERATURE RISE
The heating section for each size unit is designed and approved for
heating operation within the temperature--rise range stamped on the
unit rating plate.
Table 8 shows the approved temperature rise range for each heating
input, and the air delivery cfm at various temperature rises. The
heating operation airflow must produce a temperature rise that falls
within the approved range.
Refer to Indoor Airflow and Airflow Adjustments section to adjust
heating airflow when required.
An LED (light--emitting diode) indicator is provided on the control
board to monitor operation. The control board is located by
removing the burner access panel. During normal operation, the
LED is continuously on (See Table 4 for error codes).
48E
S