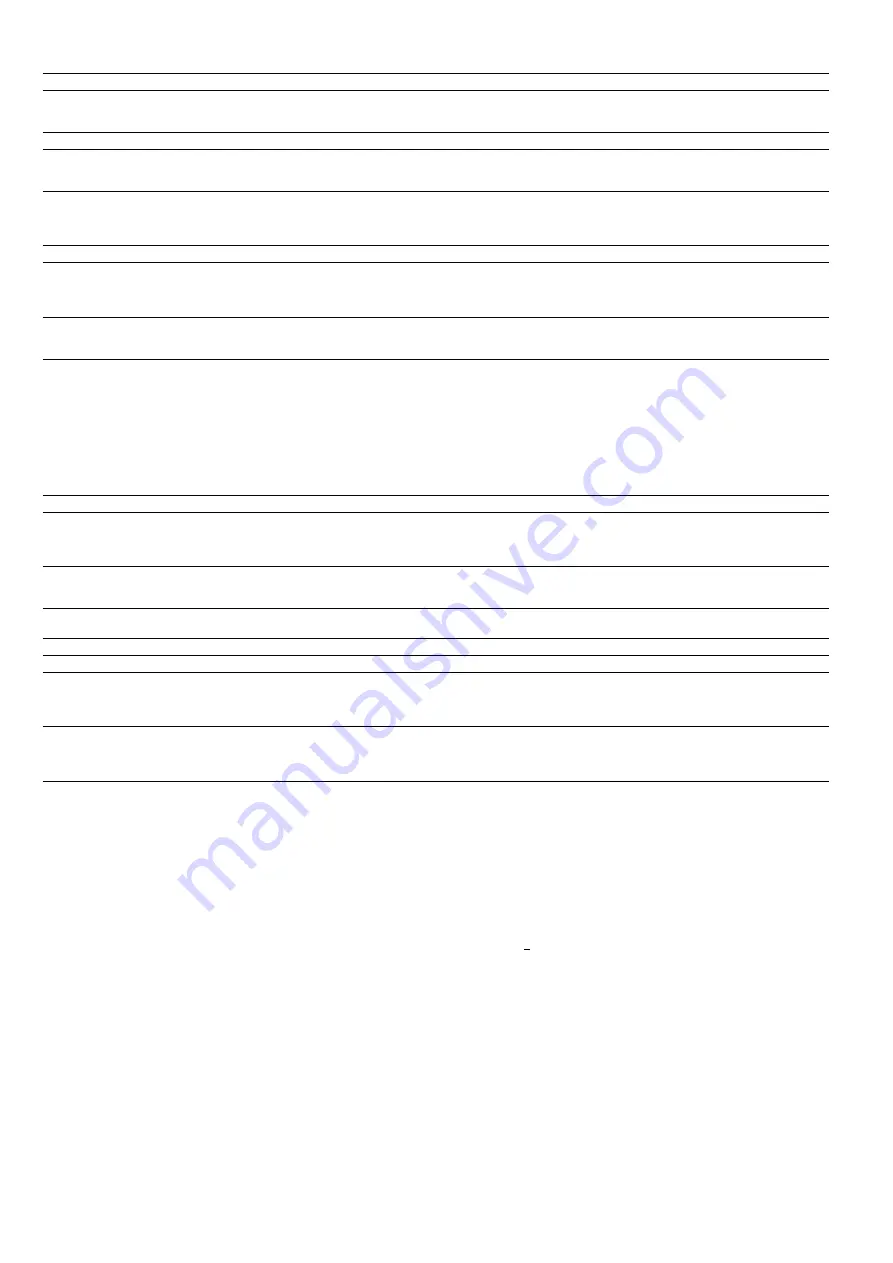
6
Physical data
38AJ/AZ
008
010
012
014
018
024
030
036
046
062
074
Nominal cooling capacity 38AJ*
kW
23.3
29.4
36.5
51.0
61.0
76.0
93.0
119.0
139.0
170.0
233.0
Nominal cooling capacity 38AZ*
kW
21.5
27.5
34.2
47.3
57.0
69.0
85.0
113.0
129.0
158.0
219.0
Operating weight**
kg
248
250
264
376
431
477
644
682
1185
1422
1492
Refrigerant
38AJ
R-22
38AZ
R-407C
Compressor
Hermetic
Semi-hermetic
Number of compressors
1
1
1
1
1
1
1
1
2
2
2
Number of capacity steps
1
1
1
2
2
2
2
2
4
4
4
Minimum capacity
%
100
100
100
66
50
66
66
66
33
33
33
Outdoor coil
Copper tubes and aluminium fins
Fan
Direct drive, propeller
Shrouded axial, Flying Bird low-noise fan
Quantity
1
1
1
1
1
1
2
2
2
4
4
Total air flow
l/s
2640
2640
2640
4700
4700
4700
9400
9400
9400
18800
18800
Speed
r/s
15
15
15
12.5
12.5
12.5
12.5
12.5
12.5
12.5
12.5
Pipe connection diameter
in
Suction line
1-1/8
1-1/8
1-1/8
1-3/8
1-5/8
1-5/8
1-5/8
2-1/8
1-5/8
2-1/8
2-1/8
Liquid line
5/8
5/8
5/8
5/8
5/8
7/8
7/8
7/8
7/8
7/8
7/8
Legend:
*
Nominal capacities are based on:
- a saturated suction temperature (R-22) or a suction dew point temperature (R-407C) of 7.2
°
C
- an outdoor air temperature (OAT) of 35
°
C
** Unit weight without options
Electrical data
38AJ/AZ
008
010
012
014
018
024
030
036
046
062
074
Power supply
Nominal power supply
V-ph-Hz 400-3-50
Voltage range
V
360-440
Auxiliary circuit
V-ph-Hz 230-1-50
Auxiliary circuit power input
(heaters)
W
70
70
70
100
200
200
200
200
400
400
400
Fan power input
kW
0.70
0.70
0.70
1.14
1.14
1.14
2.30
2.30
2.30
4.60
4.60
Fan power supply
400-3-50
Nominal unit power input*
kW
7.5
10.4
14.5
13.5
18.3
25.9
27.0
39.4
51.0
55.0
77.0
Maximum unit power input**
kW
8.6
13.0
16.1
18.6
22.3
29.2
34.9
47.3
59.0
70.0
95.0
400 V-3 ph-50 Hz (360 V-440 V)
Maximum starting current (ICF)
A
81
110
135
84
104
134
152
207
194
219
296
Nominal unit current drawn*
A
12.9
17.8
24.9
23.2
31.5
44.5
46.4
68.0
88.0
95.0
133.0
Maximum unit current drawn**
A
24.5
31.0
38.5
34.0
38.9
51.0
60.0
83.0
102.0
120.0
166.0
230 V-3 ph-50 Hz (207 V-253 V)
Maximum starting current (ICF)
A
140
190
233
146
180
232
263
359
336
379
512
Nominal unit current drawn*
A
22.3
30.9
43.2
40.2
55.0
77.0
80.0
117.0
152.0
165.0
230.0
Maximum unit current drawn**
A
42.4
54.0
67.0
59.0
67.0
88.0
104.0
144.0
177.0
208.0
288.0
Legend:
*
Saturated suction temperature (R-22) or a suction dew point temperature (R-407C) of 7.2
°
C, outdoor air temperature (OAT) of 35
°
C
** Maximum unit operating conditions (saturated suction temperature (R-22) or a suction dew point temperature (R-407C) of 10
°
C, saturated discharge temperature (R-
22) or discharge dew point temperature of 68.3
°
C.
*** ICF = maximum instantaneous current during starting, equal to the current value of the last compressor to start, plus the sum of the maximum currents of the other
compressors and fans ooperating.
Electrical data notes:
•
The units have a single power connection point.
•
A separate power source (230 V, 1 ph, 50 Hz) that does not exceed the main switch
capacity is required to power the compressor crankcase heater circuit. This source
must be supplied from a transformer. It must not be supplied from a phase + neutral
supply (for neutral systems).
•
The control box includes the following standard features:
-
Starter and motor protection devices for each compressor and the fan(s)
-
Control devices
•
Field connections:
All connections to the system and the electrical installations must be in full
accordance with all applicable local codes.
•
These Carrier units are designed and built to ensure conformance with local codes.
The recommendations of European standard EN 60 204-1 (machine safety - electrical
machine components - part 1: general regulations) are specifically taken into account,
when designing the electrical equipment.
NOTES:
•
Conformance with EN 60 204 is the best means of ensuring compliance with the
Machines Directive § 1.5.1. Generally the recommendations of IEC 364 are accepted
as compliance with the requirements of the installation directives.
•
Annex B of EN 60204-1 describes the electrical characteristics used for the operation of
the machines.
1. The operating environment for these units is specified below:
•
Environment* - Environment as classified in EN 60 721:
-
outdoor installation*
-
ambient temperature range: -25
°
C to +46
°
C, class 4K4H*
-
altitude: < 2000 m*
-
presence of hard solids, class 4S2 (no significant dust present)
-
presence of corrosive and polluting substances, class 4C2 (negligible)
-
vibration and shock, class 4M2
•
Competence of personnel, class BA4* (trained personnel - IEC 364)
2. Power supply frequency variation:
±
2 Hz.
3. The neutral (N) line must not be connected directly to the unit (if necessary use a
transformer).
4. Overcurrent protection of the power supply conductors is not provided with the unit.
5. The optional factory-installed circuit breaker is of type “a” (EN 60 204-1 § 5.3.2).
NOTE: If particular aspects of an actual installation do not conform to the conditions
described above, or if there are other conditions which should be considered, always
contact your local Carrier representative.
* The required protection level for this class is IP43BW (according to reference
document IEC 529). All units are protected to IP44CW and fulfill this protection
condition.