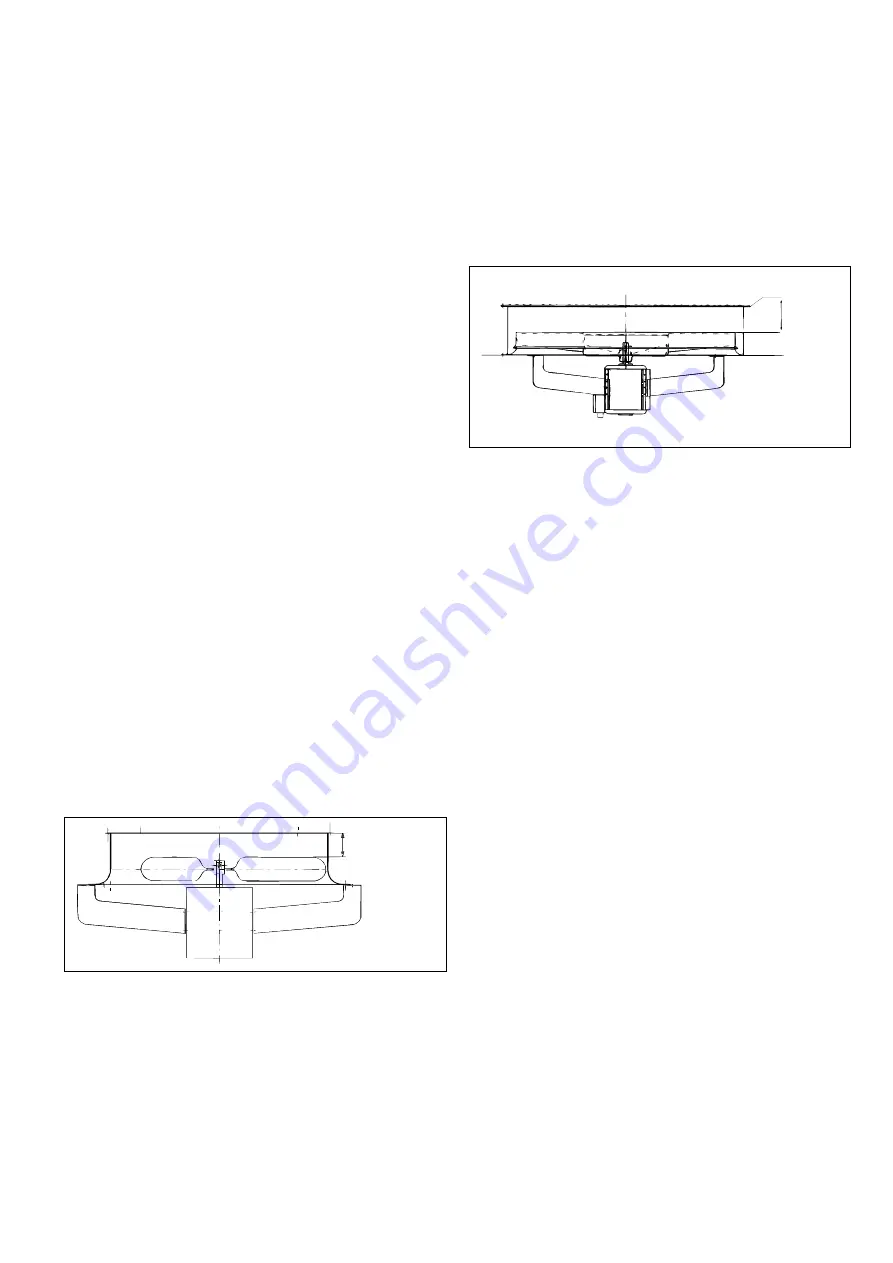
15
For normal maintenance routines we recommend using 1 kg of
the concentrated product, diluted to 10%, to treat a coil surface
of 2 m
2
. This process can either be carried out with a
TOTALINE applicator gun (part No. TE01 WA 4000EE) or
using a high-pressure spray gun in the low-pressure position.
With pressurised cleaning methods care should be taken not to
damage the coil fins.
The spraying of the coil must be done:
- in the direction of the fins
- in the opposite direction of the air flow direction
- with a large diffuser (25-30
°
)
- at a distance of 300 mm.
The two cleaning products can be used for any of the following
coil finishes: Cu/Cu, Cu/Al, Cu/Al with Polual, Blygold and/or
Heresite protection.
It is not necessary to rinse the coil, as the products used are pH
neutral. To ensure that the coil is perfectly clean, we
recommend rinsing with a low water flow rate. The pH value
of the water used should be between 7 and 8.
WARNING: Never use pressurized water without a large
diffusor. Concentrated and/or rotating water jets are strictly
forbidden.
Correct and frequent cleaning (approximately every three
months) will prevent 2/3 of the corrosion problems.
WARNING: Never use pressurized air or water, as this will
damage the fins, and always clean them against the normal air
flow direction.
Fan motor replacement
38AJ/AZ 008-012 units
Follow the safety considerations. Fan motors can be easily
removed through the top of the unit. Take care not to damage the
propeller. Label the wires to facilitate correct reassembly later.
38AJ/AZ 008-012 fan
Maximum
clearance
80 mm + mm
0
2
Maximum
clearance
170 + mm
0
2
38AJ/AZ 018-024 units
This presents no special problems. The work is done from
above the unit.
•
Remove the grille with its support air duct assembly.
•
Remove the fan shaft protection cap.
•
Pull the fan from the shaft using a FACOM U35, or
similar, hub puller.
•
Unscrew the fan motor fixing bolts.
WARNING: Remove only the lower bolts to prevent the
motor from falling.
Fan motor protection
All fan motors have thermal protection which will stop the
current flow when the fan motor temperature becomes too
high. The fans will restart automatically when the motor
temperature drops to a safe level. In addition all fan motors are
protected by one or several circuit breakers.
Refrigerant circuit
Liquid line service valve
This valve provides, in each circuit, a liquid refrigerant charging
port and, in conjunction with the compressor discharge line
valves, enables liquid refrigerant to be pumped to the high
pressure side of the system.
•
Withdraw the fan motor.
Installation is in the reverse order. Take care not to damage the
plastic components when installing the fan and position the fan
to maintain a clearance of 170 + 0/2 mm between the upper
edge of the fan and the upper edge of the volute. The tightening
torque on the fan motor support fixing screws must be 9 Nm.
CAUTION: On unit sizes 38AJ/AZ 014-074 the fan rotation is
counter clockwise, viewed from above.
38AJ/AZ 014-074 fan