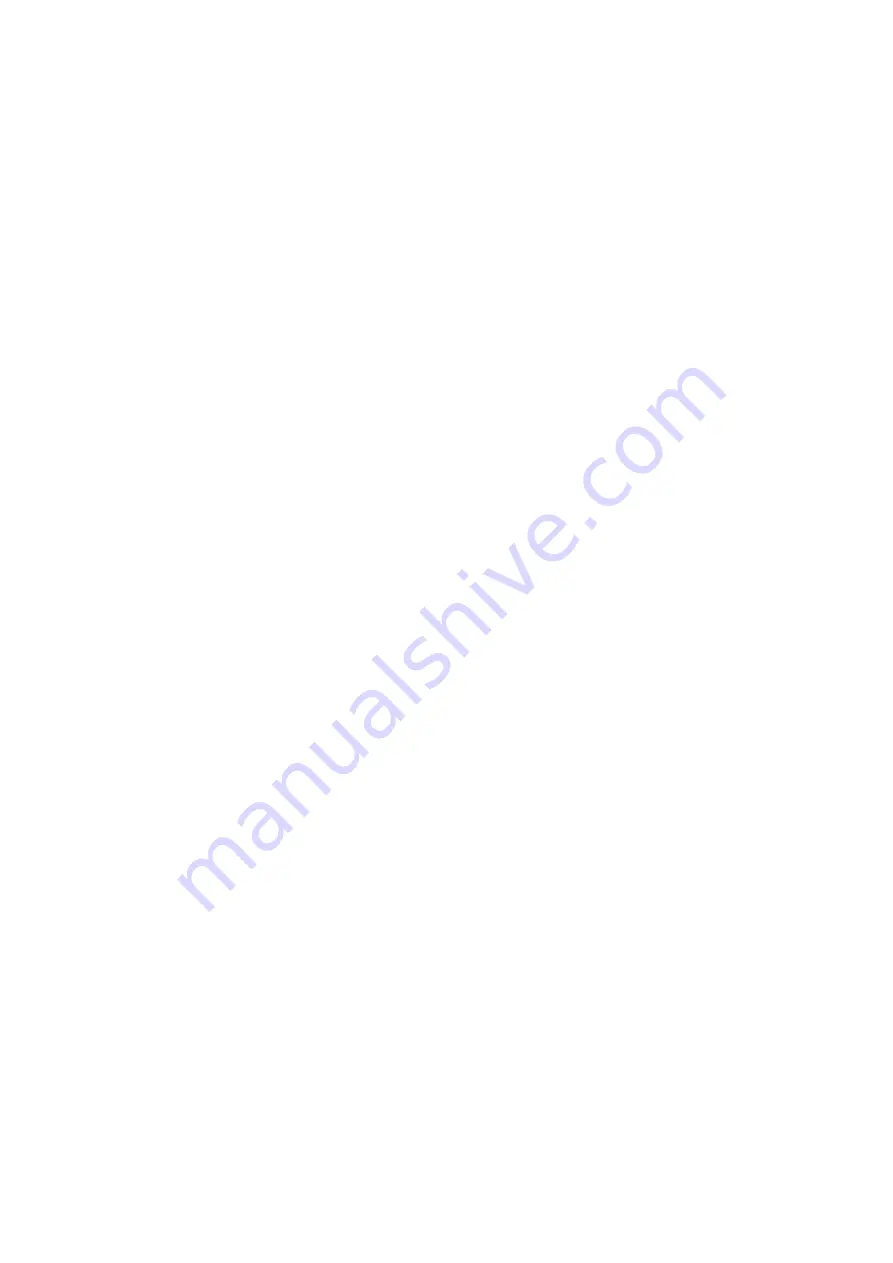
13
SERVICING REFRIGERATION COMPONENTS
Any technician attending the machine for any purpose must be
a fully qualified refrigeration engineer.
WARNING: Before doing any work on the machine ensure that
the power is switched and locked off and that all isolators are
tagged. If a refrigerant circuit is opened, it must be evacuated,
and recharged, after ensuring that the refrigerant is clean and
free from impurities, the filter-drier has been changed and the
unit has been tested for leaks. Before any operation on a
refrigerant circuit, it is necessary to remove the complete
charge of refrigerant from the unit with a refrigerant charge
recovery group.
General maintenance
Keep the unit itself and the space around it clean and free of
obstructions. Remove all rubbish such as packing materials, as
soon as the installation is completed.
Regularly clean the exposed pipework to remove all dust and
dirt. This makes detection of water leaks easier, and they can
be repaired before more serious faults develop.
Confirm that all screwed and bolted connections and joints are
secure. Secure connections prevent leaks and vibration from
developing.
Check that all insulation joints are securely closed and that all
insulation is firmly in place. Check all heat exchangers and all
pipework.
Confirm regularly that any phase imbalance in the three-phase
power supply is within acceptable limits.
Lubricate the hinges, locks and latches on the electrical control
box doors sparingly.
Liquid refrigerant charging
Checking the charge
Run the unit at full capacity for some time and then add
refrigerant until there are no bubbles in the sight glass. This
will generally mean adding more refrigerant than would be
needed to prevent bubbles from being seen in the sight glass.
WARNING: To ensure proper operation of these units there
must be at least 5 K of subcooling as the liquid refrigerant
enters the expansion valve (difference between the saturated
pressure at the liquid valve and the liquid temperature).
The 38AJ/AZ units use a liquid refrigerant charge. For your
information, we are reproducing here some extracts from the
official publication dealing with the design, installation,
operation and maintenance of air conditioning and refrigera-
tion systems and the training of people involved in these
activities, agreed by the air conditioning and refrigeration
industry.
Refrigerant guidelines
Refrigeration installations must be inspected and maintained
regularly and rigorously by specialists. Their activities must be
overseen and checked by properly trained people.
To minimise discharge to the atmosphere, refrigerants and
lubricating oil must be transferred using methods which reduce
leaks and losses to a minimum.
•
Leaks must be repaired immediately
•
A valve on the condenser liquid refrigerant outlet line
enables the refrigerant charge to be transferred to the
receiver provided specifically for this purpose.
•
If the residual pressure is too low to make the transfer
alone, a purpose-built refrigerant recovery unit must be
used.
•
Compressor lubricating oil contains refrigerant. Any oil
drained from a system during maintenance must therefore
be handled and stored accordingly.
•
Refrigerant under pressure must never be discharged to
the atmosphere.
CAUTION: 38AZ units are designed to run on refrigerant
HFC-407C. This non-azeotropic refrigerant blend consists of
23% R-32, 25% of R-125 and 52% R-134a, and is character-
ised by the fact that at the time of the change in state the
temperature of the liquid/vapour mixture is not constant, as
with azeotropic refrigerants. All checks must be pressure tests,
and the appropriate pressure/temperature ratio table must be
used for the interpretation of the values.
Leak detection is especially important for units charged with
refrigerant R-407C. Depending on whether the leak occurs in
the liquid or in the vapour phase, the proportion of the
different components in the remaining liquid is not the same.
Undercharge
If there is not enough refrigerant in the system, this is indicated
by gas bubbles in the moisture sight glass. There are two
possiblities:
•
Small undercharge (bubbles in the sight glass, no
significant change in suction pressure).
-
After detection and repair the unit can be recharged.
-
The replenishment of the charge must always be done
in the liquid phase at the liquid line. The refrigerant
cylinder must contain a minimum of 10% of its initial
charge.
•
Significant undercharge (large bubbles in the sight glass,
drop in suction pressure).
-
After detection and repair completely drain the
refrigerant charge, using a refrigerant recovery unit,
then recharge completely, following the precautions
given above.
Compressors
Checking the oil charge
Check the oil level and add or remove oil as necessary so that
the level is 1/8 to 3/8 up each sight glass with the compressors
running normally.
WARNING: Use only oils which have been approved for use in
refrigeration compressors. Never use oil which has been
exposed to air.