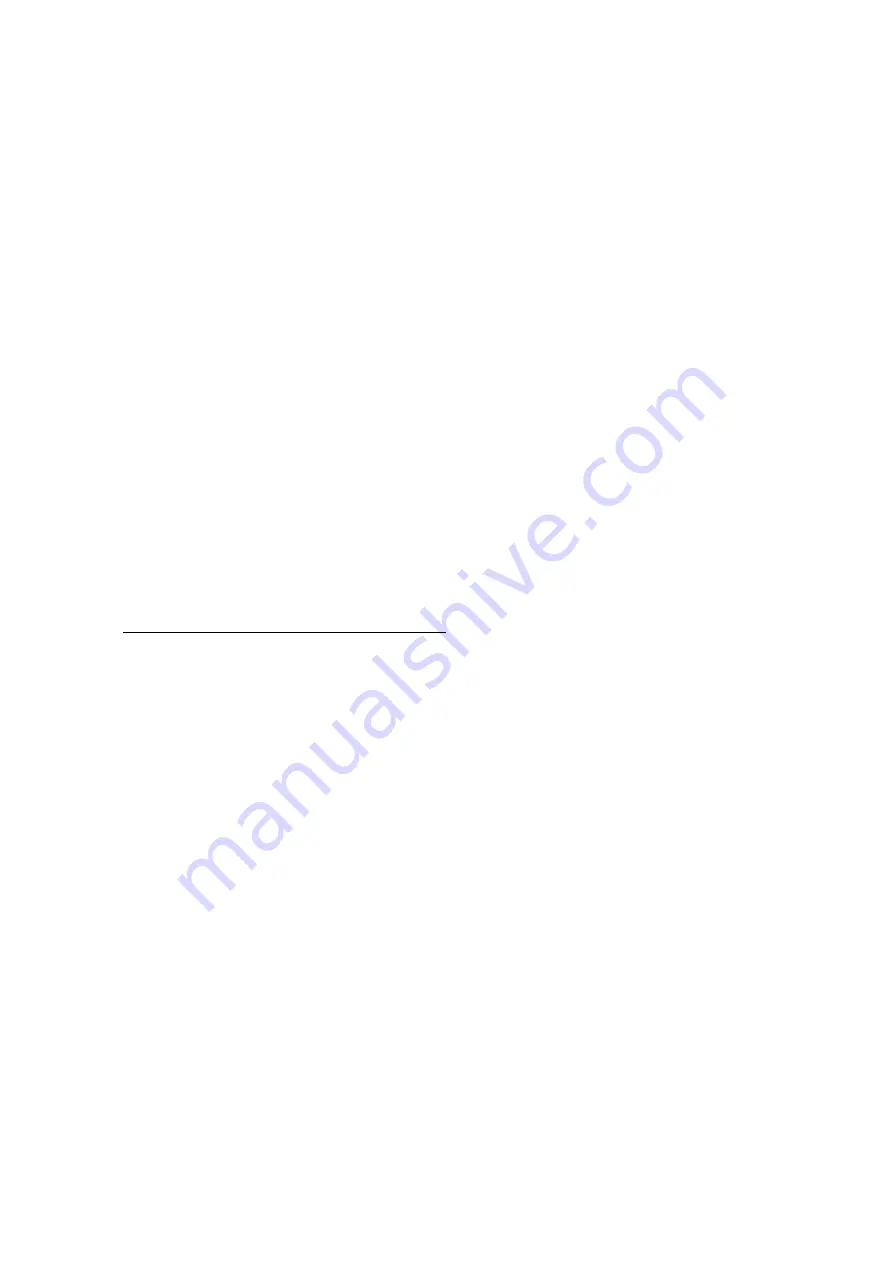
11
ACCESSORIES
The field-installed accessories are shipped with full installation
instructions and/or a wiring diagram.
•
Single- or two-stage low voltage thermostat.
•
Additional capacity unloader
•
Fan speed controller to maintain the condensing pressure
in the winter months
•
Hot gas bypass
•
Control circuit transformer
•
Coil protection grilles
•
Compressor operating hours counter
•
Compressor oil differential pressure gauge
•
Gauge panel (HP-LP)
Power supply
The power supply must conform to the specification on the
chiller nameplate. The supply voltage must be within the range
specified in the electrical data table.
For connections refer to the wiring diagrams.
WARNING: Operation of the chiller with an improper supply
voltage or with excessive phase imbalance constitutes abuse
which will invalidate the Carrier warranty. If the phase
imbalance exceeds 2% for voltage, contact your local
electricity supply company at once and ensure that the chiller
is not switched on until corrective measures have been taken.
Voltage phase imbalance (%) :
= 100 x max.deviation from average voltage deviation
Average voltage
WARNING: Never switch off the power supply to the crankcase
heaters unless the chiller is out of service for a seasonal
shutdown or lengthy repair. The heaters must be re-energised
for at least 24 hours before the chiller is restarted.
Start-up
IMPORTANT: Commissioning and start-up of the chiller must
be supervised by a qualified refrigeration engineer.
Preliminary checks
Before the unit pre-start-up, or start-up follow the start-up
checklist on page 3 of this document. Use of this list will
ensure a troublefree start-up, maintaining the initial operating
parameters.
Never start the unit, even momentarily, without fully
understanding the instructions in this document and without
having taken the following precautions:
•
Confirm that the power supply corresponds to the data on
the unit nameplate.
•
Check that the crankcase heaters are securely in place.
•
Touch the compressor crankcase to confirm that the
crankcase heaters are working. Each compressor is
equipped with a heater (see wiring diagram) which is
energized when the unit is switched off to ensure proper
lubrication of the compressor.
•
Open the compressor suction and discharge line valves,
and then close them one turn each to stabilise the pressure
to the control gauges (if fitted).
•
Open the liquid line service valves.
•
Check that the compressor sight glasses show an oil level
between 1/8 and 3/8 (check all compressors).
•
Check that there are no refrigerant leaks.
•
Confirm that the discharge muffler securing bands are
secure.
Electrical checks
Switch the power off.
Open the control circuit switch. Check the mains supply
voltage at the power supply bus bars.
•
Check the connections to the transformers.
•
Check the control circuit with reference to the unit wiring
diagram.
•
Check the tightness of all electrical connections
(terminals, connectors, bus bars etc.)
•
Check the direction of rotation of the three-phase fan
motors. Viewed from above the unit the direction of
rotation of the plastic blades must be counter-clockwise.
Swap any two of the three wires to correct the direction of
rotation, if necessary.
Unit start-up
Set the room thermostat to a temperature that is lower than the
room temperature in order to try to start up the unit. After this
check reset the thermostat to the set point which corresponds to
the required temperature.
Pressure-operated capacity control valves
See Fig. 7 and capacity reduction table.
Pressure-operated control valve
These valves are suction pressure-controlled and discharge
pressure-actuated. Each valve controls two cylinders. At start-
up the controlled cylinders do not load up until the differential
between the suction and discharge pressure is 70 kPa (10 psig).
Control setpoint
The cylinder control setpoint is set between 0 kPa and 586 kPa.
The differential pressure (difference in pressure between the
suction and discharge ports in a cylinder) is controllable
between 41 kPa and 152 kPa.
Setpoint control (cylinder load point)
Turn adjustment nut
햲
clockwise to its maximum position.
The setpoint is now 586 kPa.
The setpoint can now be adjusted to the desired pressure by turn-
ing the adjustment nut counter-clockwise. The number of turns
required can be determined from the curve. Each full turn counter-
clockwise decreases the setpoint by approximately 51 kPa.
11-1/2 turns will decrease the setpoints from 586 kPa to 0 kPa.