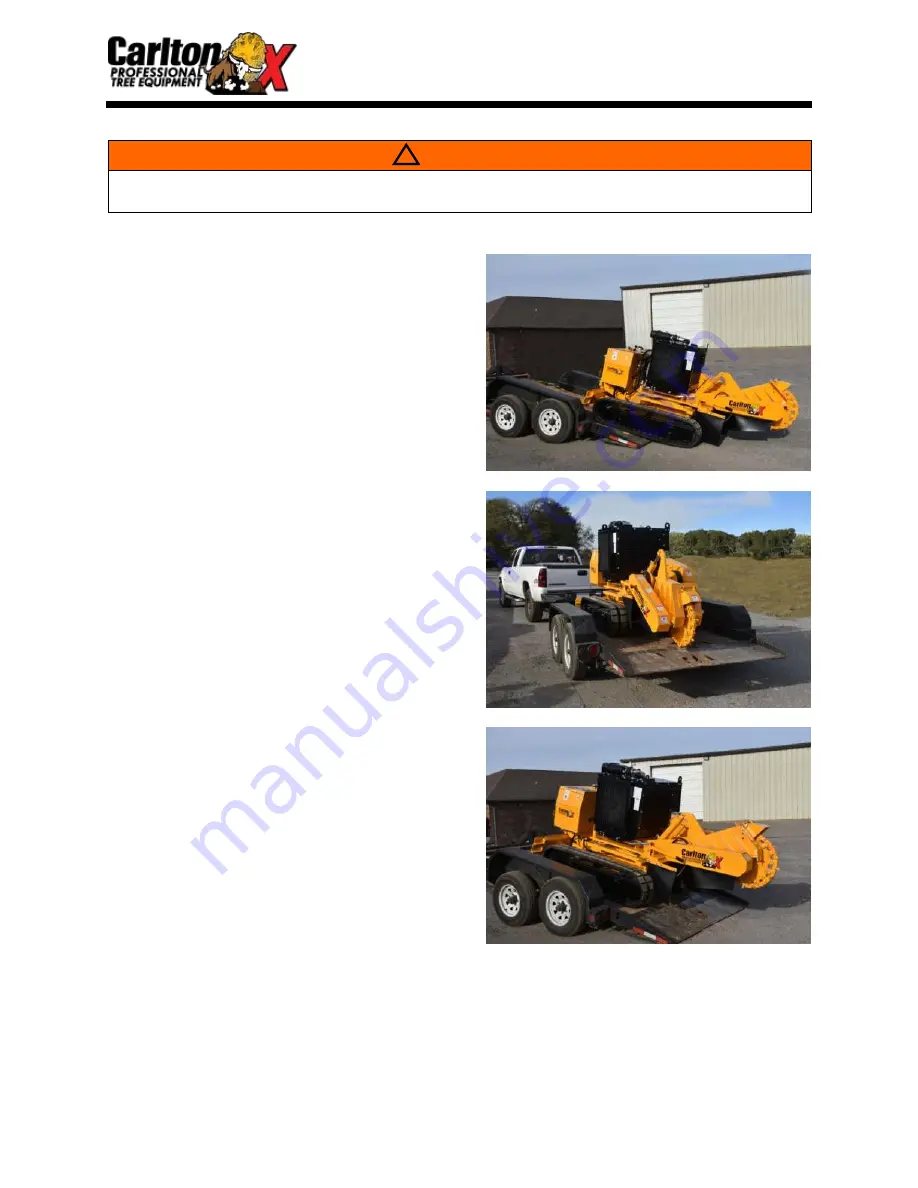
SP8018 TRANSPORTING
LOADING
•
Start engine as recommended by the
engine manufacturers manual.
•
Increase engine RPM, raise cutter head
just off the ground.
•
With operator in position, push the
forward travel control lever and steer
machine slowly up appropriate ramp into
transport vehicle.
KEEP MACHINE AS LEVEL AS
POSSIBLE.
•
Continually adjust cutter head height as
you go, keeping the mass as low to the
ground as possible.
•
Once the machine is loaded, lower the
cutter head, shut down engine and secure
machine tightly with sufficient tie downs
to prevent any movement in transit.
UNLOADING
•
Undo tie down straps and check ramps
for sturdiness and positioning.
•
Start engine, increase RPM, and raise
cutter head to just clear deck and/or
ramp.
•
Continually adjust Cutter head up and
down to keep the center of gravity as
low as possible.
•
Proceed to work site using extreme
caution on hills or uneven terrain.
WARNING
Trailer must be securely attached to tow vehicle before loading or unloading the stump grinder.
Do not unload on anything other than level ground!
!
17
Summary of Contents for SP8018
Page 2: ...BLANK SHEET...
Page 4: ...SP8018 SAFETY ALERT...
Page 5: ...SP8018 SAFETY ALERT OPERATE MACHINE FROM 25 FEET AWAY KEEP SPECTATORS AWAY...
Page 6: ...SP8018 SAFETY ALERT...
Page 7: ...SP8018 SAFETY ALERT...
Page 8: ...BLANK SHEET...
Page 12: ...BLANK SHEET...
Page 66: ...SP8018 STEIN MFG PTO CLUTCH Depending on engine selection 53...
Page 71: ...1 RUBBER TRACK OPERATIONS MANUAL...
Page 72: ...2...
Page 85: ...15 2 6 LUBRICATION CHART...
Page 92: ...22 APPENDIX A BOLT TORQUE TABLE...
Page 93: ...Appendix A...
Page 94: ...BLANK SHEET...
Page 96: ......