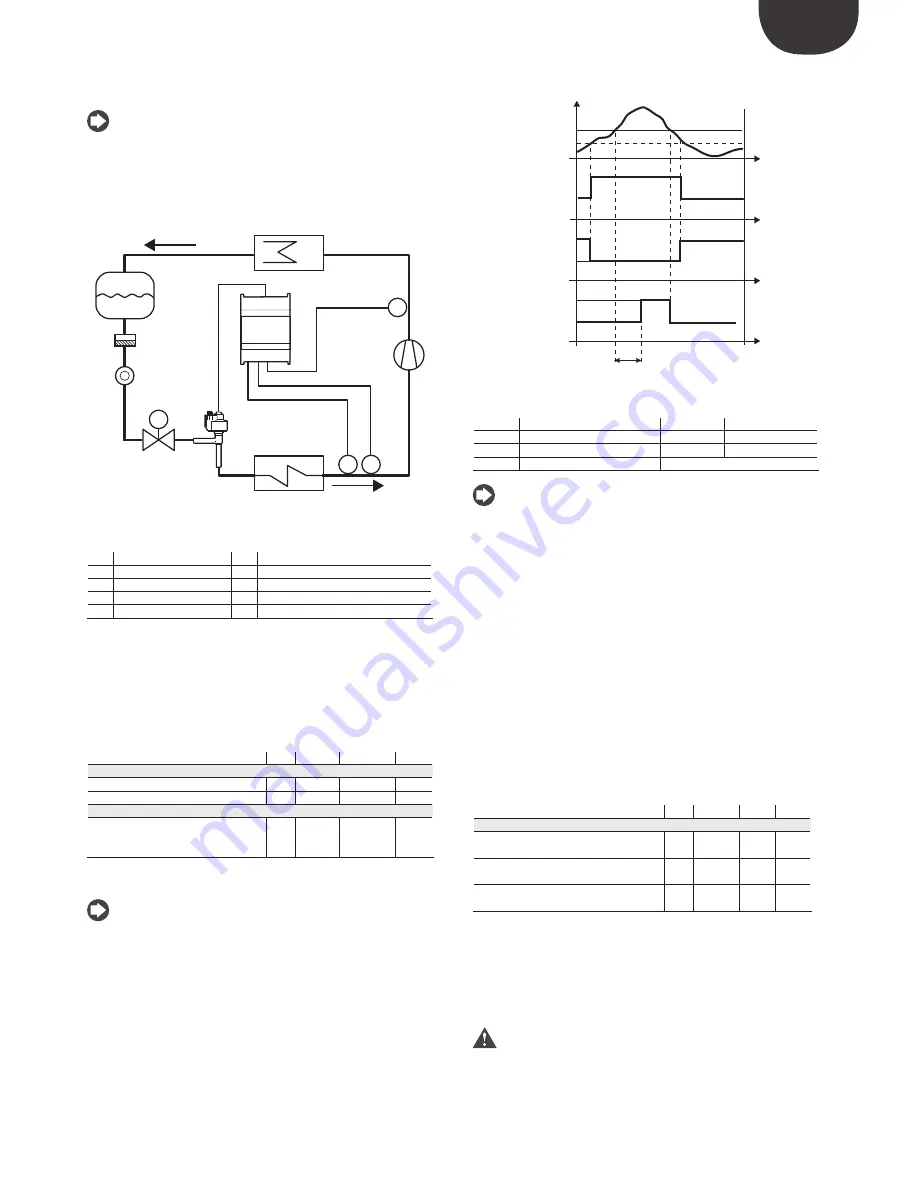
ENG
“EVD Evolution TWIN” +0300006EN - rel. 2.6 - 31.01.2019
63
The last option (available if “main control” = 1 to 18) requires the installation of
both probes S3 & S4, the first pressure and the second temperature.
Note:
if only one backup probe is fitted, under the manufacture
parameters, the probe thresholds and alarm management can be set
separately.
HIT
C
ond protection (high condensing temperature)
The functional diagram is shown below.
S2
S3
S1
EVD
evolution
P
P
E
V
S
F
L
M
T
CP
C
EEV
Fig. 13.g
Key:
CP
Compressor
EEV Electronic expansion valve
C Condenser
V Solenoid
valve
L Liquid
receiver
E Evaporator
F
Dewatering filter
P
Pressure probe (transducer)
S
Liquid indicator
T
Temperature probe
For the wiring, see paragraph “General connection diagram”.
As already mentioned, the HITCond protection can only be enabled if the
controller measures the condensing pressure/temperature, and responds
moderately by closing the valve in the event where the condensing
temperature reaches excessive values, to prevent the compressor from
shutting down due to high pressure. The condensing pressure probe must be
connected to input S3.
Parameter/description
Def.
Min.
Max.
UOM
ADVANCED
High Tcond threshold
80
-60 (-76) 200 (392)
°C (°F)
High Tcond integration time
20
0
800
s
ALARM CONFIGURATION
High condensing temperature alarm
timeout (High Tcond)
(0= alarm DISABLED)
600
0
18000
s
Tab. 13.j
The integration time is set automatically based on the type of main control.
Note
:
•
the protector is very useful in units with compressors on board if the air-
cooled condenser is undersized or dirty/malfunctioning in the more critical
operating conditions (high outside temperature);
•
the protector has no purpose in multiplexed systems (showcases), where
the condensing pressure is maintained constant and the status of the
individual electronic valves does not affect the pressure value.
To reduce the condensing temperature, the output of the refrigeration
unit needs to be decreased. This can be done by controlled closing of the
electronic valve, implying superheat is no longer controlled, and an increase in
the superheat temperature. The protector will thus have a moderate reaction
that tends to limit the increase in the condensing temperature, keeping
it below the activation threshold while trying to stop the superheat from
increasing as much as possible. Normal operating conditions will not resume
based on the activation of the protector, but rather on the reduction in the
outside temperature. The system will therefore remain in the best operating
conditions (a little below the threshold) until the environmental conditions
change.
t
t
t
t
OFF
ON
ALARM
OFF
ON
PID
OFF
ON
MOP
MOP
_T
H
- 1
MOP
_T
H
T_
EVAP
D
Fig. 13.h
Key:
T_COND Condensing temperature
T_COND_TH HiTcond: threshold
HiTcond High Tcond protection status
HiTcond
ALARM Alarm
PID
PID superheat control
t
Time
D Alarm
timeout
Note
:
•
the High Tcond threshold must be greater than the rated condensing
temperature of the unit and lower then the calibration of the high pressure
switch;
•
the closing of the valve will be limited if this causes an excessive decrease
in the evaporation temperature.
Modulating thermostat
This function is used, by connecting a temperature probe to input S4, to
modulate the opening of the electronic valve so as to limit the lowering of
the temperature read and consequently reach the control set point. This is
useful in applications such as the multiplexed cabinets to avoid the typical
swings in air temperature due to the ON/OFF control (thermostatic) of the
solenoid valve. A temperature probe must be connected to input S4, located
in a similar position to the one used for the traditional temperature control
of the cabinet. In practice, the close the controlled temperature gets to the
set point, the more the control function decreases the cooling capacity of
the evaporator by closing the expansion valve. By correctly setting the related
parameters (see below), a very stable cabinet temperature can be achieved
around the set point, without ever closing the solenoid valve. The function is
defined by three parameters: set point, differential and offset.
Parameter/description
Def.
Min.
Max.
UOM
ADVANCED
Modul. thermost setpoint
0
-60 (-76) 200
(392)
°C (°F)
Modul. thermost differential
0.1
0.1 (0.2)
100
(180)
°C (°F)
Modul. thermost SHset offset (0= fun-
ction disabled)
0
0 (0)
100
(180)
K (°R)
Tab. 13.k
The first two should have values similar to those set on the controller for the
cabinet or utility whose temperature is being modulated.
The offset, on the other hand, defines the intensity in closing the valve as
the temperature decreases: the greater the offset, the more the valve will be
modulated. The function is only active in a temperature band between the set
point and the set point plus the differential.
Important:
the “Modulating thermostat” function should not be used
on stand-alone refrigeration units, but only in centralised systems. In fact, in
the former case closing the valve would cause a lowering of the pressure and
consequently shut down the compressor.
Summary of Contents for EVD Evolution Twin
Page 2: ......
Page 4: ......
Page 6: ......
Page 66: ...ENG EVD Evolution TWIN 0300006EN rel 2 6 31 01 2019 66 Note...
Page 67: ......