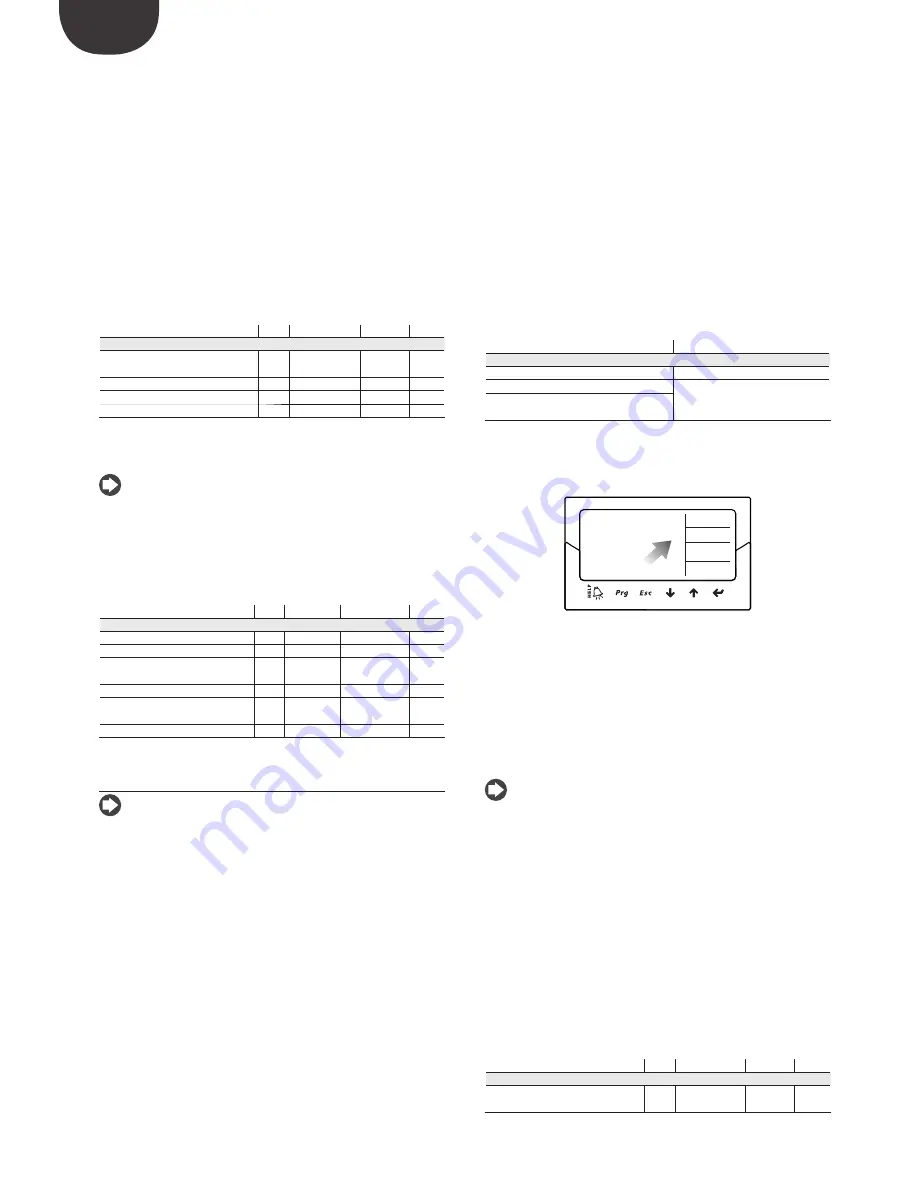
ENG
“EVD Evolution TWIN” +0300006EN - rel. 2.6 - 31.01.2019
22
Note that control is calculated as the sum of three separate contributions:
proportional, integral and derivative.
•
the proportional action opens or closes the valve proportionally to the
variation in the superheat temperature. Thus the greater the K (proportional
gain) the higher the response speed of the valve. The proportional action
does not consider the superheat set point, but rather only reacts to
variations. Therefore if the superheat value does not vary significantly, the
valve will essentially remain stationary and the set point cannot be reached;
•
the integral action is linked to time and moves the valve in proportion to
the deviation of the superheat value from the set point. The greater the
deviations, the more intense the integral action; in addition, the lower
the value of T (integral time), the more intense the action will be. The
integration time, in summary, represents the intensity of the reaction of the
valve, especially when the superheat value is not near the set point;
•
the derivative action is linked to the speed of variation of the superheat value,
that is, the gradient at which the superheat changes from instant to instant.
It tends to react to any sudden variations, bringing forward the corrective
action, and its intensity depends on the value of the time T (derivative time).
Parameter/Description
Def.
Min.
Max.
UOM
CONTROL
Superheat set point
11
LowSH: thre-
shold
180 (324) K(°F)
PID: proportional gain
15
0
800
-
PID: integral time
150
0
1000
s
PID: derivative time
5
0
800
s
Tab. 5.b
See the “EEV system guide” +030220810 for further information on calibrating
PID control.
Note: when selecting the type of main control (both superheat control
and special modes), the PID control values suggested by CAREL will be
automatically set for each application.
P
rotection function control parameters
See the chapter on “Protectors”. Note that the protection thresholds are set by
the installer/manufacturer, while the times are automatically set based on the
PID control values suggested by CAREL for each application.
Parameter/Description
Def.
Min.
Max.
UOM
CONTROL
LowSH protection: threshold
5
-40 (-72)
SH set point
K (°F)
LowSH protection: integral time
15
0
800
s
LOP protection: threshold
-50
-60 (-76)
MOP: th-
reshold
°C (°F)
LOP protection: integral time
0
0
800
s
MOP protection: threshold
50
LOP: thre-
shold
200 (392)
°C (°F)
MOP protection: integral time
20
0
800
s
Tab. 5.c
5.3 Adaptive control and autotuning
Note: from the software revision following the 6.6-6.7, functions
“Adaptive control” and “Autotuning” are no longer present. Then
the setting:
Main control= air-conditioner/chiller or cabinet/ cold room with adaptive
control, is equivalent to:
Main control = multiplexed cabinet/cold room.
EVD evolution TWIN features two functions used to automatically optimise
the PID parameters for superheat control, useful in applications where there
are frequent variations in thermal load:
1.
automatic adaptive control: the function continuously evaluates the
effectiveness of superheat control and activates one or more optimisation
procedures accordingly;
2.
manual autotuning: this is activated by the user and involves just one
optimisation procedure.
Both procedures give new values to the PID superheat control and protection
function parameters:
-
PID: proportional gain;
-
PID: integral time;
-
PID: derivative time;
-
LowSH: low superheat integral time;
-
LOP: low evaporation temperature integral time;
-
MOP: high evaporation temperature integral time.
Given the highly variable dynamics of superheat control on different units,
applications and valves, the theories on stability that adaptive control and
autotuning are based on are not always definitive. As a consequence, the
following procedure is suggested, in which each successive step is performed
if the previous has not given a positive outcome:
1.
use the parameters recommended by CAREL to control the different
units based on the values available for the “Main control” parameter;
2.
use any parameters tested and calibrated manually based on laboratory
or field experiences with the unit in question;
3.
enable automatic adaptive control;
4.
activate one or more manual autotuning procedures with the unit in
stable operating conditions if adaptive control generates the “Adaptive
control ineffective” alarm.
A
daptive control
After having completed the commissioning procedure, to activate adaptive
control, set the parameter:
“Main control”= air-conditioner/chiller or showcase/cold room with adaptive
control
Parameter/Description
Def.
CONFIGURATION
Main control
multiplexed showcase/cold room
...
air-conditioner/chiller or showcase/cold
room with adaptive control
Tab. 5.d
The activation status of the tuning procedure will be shown on the standard
display by the letter “T”.
Superheating
4.9 K
Valve opening
44 %
ON
-- Relais
A/B
T
Fig. 5.d
With adaptive control enabled, the controller constantly evaluates whether
control is sufficiently stable and reactive; otherwise the procedure for
optimising the PID parameters is activated. The activation status of the
optimisation function is indicated on the standard display by the message
“TUN” at the top right.
The PID parameter optimisation phase involves several operations on the
valve and readings of the control variables so as to calculate and validate
the PID parameters. These procedures are repeated to fine-tune superheat
control as much as possible, over a maximum of 12 hours.
Note:
•
during the optimisation phase maintenance of the superheat set point is
not guaranteed, however the safety of the unit is ensured through activation
of the protectors. If these are activated, the procedure is interrupted;
•
if all the attempts performed over 12 hours are unsuccessful, the “adaptive
control ineffective” alarm will be signalled and adaptive control will be
disabled, resetting the default values of the PID and protection function
parameters;
•
to deactivate the “adaptive control ineffective” alarm set the value of the
“main control” parameter to one of the first 10 options. If required, adaptive
control can be immediately re-enabled using the same parameter. If the
procedure ends successfully, the resulting control parameters will be
automatically saved.
A
utotuning
EVD evolution TWIN also features an automatic tuning function (Autotuning)
for the superheat and protector control parameters, which can be started by
setting the parameter “Force manual tuning” = 1.
Parameter/Description
Def.
Min.
Max.
UOM
SPECIAL
Force manual tuning
0 = no; 1= yes
0
0
1
-
Tab. 5.e
Summary of Contents for EVD Evolution Twin
Page 2: ......
Page 4: ......
Page 6: ......
Page 66: ...ENG EVD Evolution TWIN 0300006EN rel 2 6 31 01 2019 66 Note...
Page 67: ......