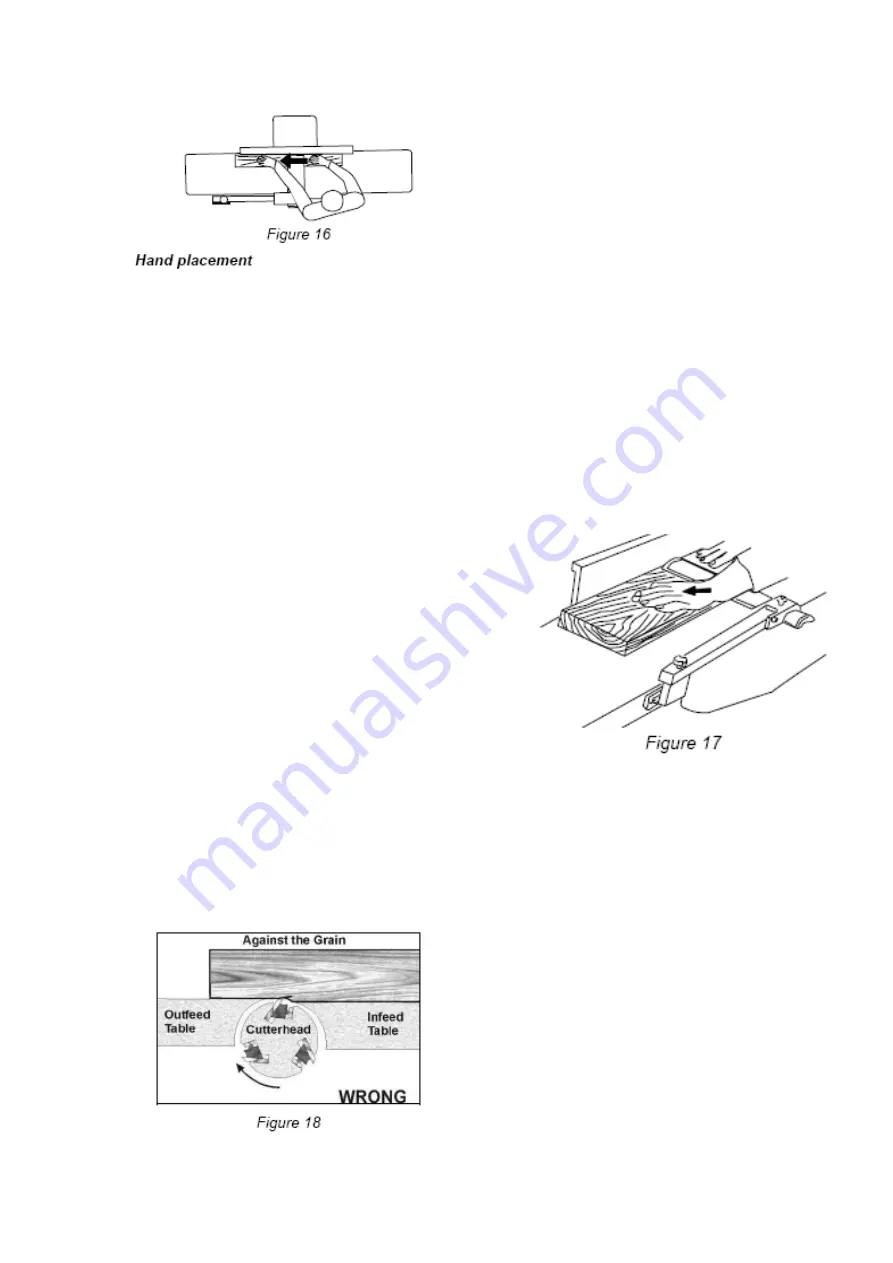
eferring to Figure 16:
At the start of the cut, the left hand holds the workpiece firmly against the infeed
table and fence while the right hand pushes the workpiece
in a smooth, even motion toward the cutterhead. After the cut is under way, the new
surface rests firmly on the outfeed table. he left hand is transferred to the outfeed
side (Figure 16) and presses down on this part of the workpiece, at the same time
maintaining flat contact with the fence. he right hand presses the workpiece
forward and before the right hand reaches the cutterhead it should be moved to the
work on the outfeed table.
Surfacing
he purpose of planing on a jointer is to produce
one flat surface (Figure 17). he other side can
then be milled to precise, final dimensions on a
thickness planer resulting in a board that is
smooth and flat on both sides and each side
parallel to the other.
If the wood to be jointed is cupped or
bowed, place the concave side down, and
take light cuts until the surface is flat.
Never surface pieces shorter than 12 inches
or thinner than 3/8 inch without the use of a
special work holding fixture.
Never surface pieces thinner than 3 inches without the use of a push block.
Cuts of approximately 1/16" at a time are recommended, which provides for
better control over the material being surfaced. More passes can then be made to
reach the desired depth.
Direction of Grain
Avoid feeding work into the jointer against the grain (Figure 18).
300mm
10mm,
or push blocks
1.5mm
75mm
Summary of Contents for TJ-X300C
Page 1: ...OWNERS MANUAL 300mm Industrial Thicknesser Jointer with Helical Cutterhead TJ X300C WARRANTY...
Page 25: ......
Page 26: ...Performance Troubleshooting Planer...
Page 27: ...Mechanical Troubleshooting Planer Jointer...
Page 28: ...TJ X300C Cutter Block Guard and Outfeed Assembly...
Page 31: ...TJ X300C Cutter Block assembly...
Page 33: ...TJ X300C Base Assembly...
Page 35: ...TJ X300C Infeed Table Assembly...
Page 37: ...TJ X300C Drive and Motor Assembly...
Page 39: ...TJ X300C Thickness Table Assembly...
Page 41: ...TJ X300C Working Fence Assembly...
Page 43: ......