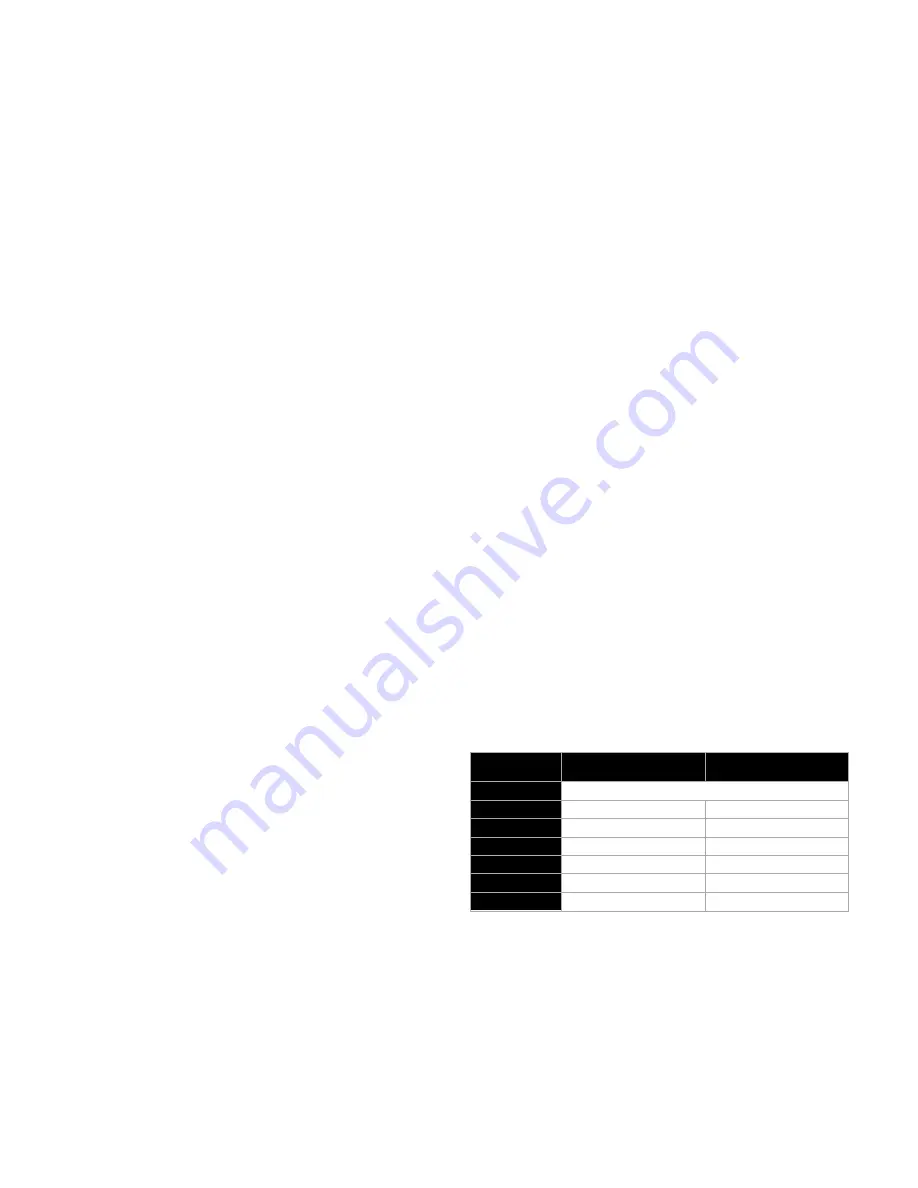
4
1.4
– Sequence of Operation
1.
Supply power connection as per Section 1.3.2.
2.
The power switch is placed in the “ON” position. 120 VAC
power is supplied to the control transformer. 24 VAC is
supplied to the ignition module and low voltage controls for
all models.
3.
If a Low Water Cut-off (LWCO) is supplied, it must be closed
to allow operation. The LWCO is to be wired into the
appropriate contacts on the unit control panel.
4.
The control activates the unit when the temperature
measured by the top tank sensor drops below the setpoint
(“SETPOINT”) by the programmed tank differential (“DIFF
ON
”).
5.
The control energizes the blower, increasing the voltage to
the electrically commutated DC motor on the combustion fan.
6.
If the airflow switches are closed the fan will run at pre-purge
speed until the pre-purge timer is satisfied.
7.
After pre-purge, the control will target the ignition fan speed.
8.
The control energizes the hot surface igniter for about 10
seconds. At the end of this period, the main gas valve is
energized for 4 seconds, during which time the flame must be
established.
9.
The hot surface igniter is de-energized at the end of the
ignition period.
10.
At the end of the flame establishing period, a signal of 0.8 Vdc
must be recognized by the controller at the flame sensor
(“
CURRENT
”) to keep the main gas valve in an open position.
The fan is kept at ignition speed until the stabilization timer is
satisfied, and the main flame is established.
11. The control will enter operation and release to modulation.
12. The control will modulate fan speed through Pulse Width
Modulation (PWM), adjusting water heater input to meet and
then maintain target temperature.
13. Fan speeds will modulate down when the temperature
measured by the temperature sensor is approaching setpoint.
14. The control will stage the unit off when the temperature
measured by the top tank sensor reaches setpoint.
15. The burner will shut off and the fan speed will ramp up to
post-purge speed until the post-purge timer is satisfied.
16. The unit will then go into standby until the next demand.
1.5
– Codes
The equipment shall be installed in accordance with those
installation regulations in force in the local area where the
installation is to be made.
These shall be carefully followed in
all cases. Authorities having jurisdiction shall be consulted before
installations are made. In the absence of such requirements, the
installation shall conform to the latest edition of the National Fuel
Gas Code, ANSI Z223.1. NFPD 54 and/or CSA B149.1-15 and
CSA B149.2-15 Natural Gas and Propane Installation Code. All
electrical wiring must be done in accordance with the
requirements of the authority having jurisdiction or, in the
absence of such requirements, with National Electrical Code,
ANSI/NFPA70 and/or the Canadian Electrical Code part 1 CSA
C22.1. Where required by the authority having jurisdiction, the
installation must conform to American Society of Mechanical
Engineers Safety Code for Controls and Safety Devices for
Automatically Fired Boilers, ASME CSD-1. All water heaters
conform to the latest edition of the ASME Boiler and Pressure
Vessel Code, Section II. Where required by the authority having
jurisdiction, the installation must comply with the CSA
International, CSA B149.1-15 and CSA B149.2-15 and/or local
codes. This appliance meets the safe lighting performance
criteria with the gas manifold and control assembly provided, as
specified in the ANSI standards for gas-fired units, ANSI
Z21.10.3.
1.6
– Warranty
Factory warranty (shipped with unit) does not apply to units
improperly installed or improperly operated.
Factory warranty (shipped with unit) does not apply to units
with no or improperly installed or operated
pump assembly
.
Factory warranty shall apply only when the appliance is
installed in accordance with local plumbing and building
codes, ordinances and regulations, the printed instructions
provided with it and industry best practices.
Excessive
water hardness
causing a scale buildup in the
stainless steel coils or tubes is not a fault of the appliance and
is not covered by warranty.
Using or storing
corrosive chemicals
in the vicinity of this
appliance can rapidly attack the stainless steel tubes and
coils and voids warranty.
Damage caused by
freezing or dry firing
voids warranty.
This appliance is not to be used for
temporary service
of
buildings under construction.
The manufacturer shall
NOT
be held liable for any personal
injury or property damage due to ice formation or the
dislodging of ice from the vent system or the vent termination.
1.7
– Scald Prevention
Water should be stored above 122
°
F (50
°
C) to avoid the bacterial
growth that happens at cooler temperatures. B
acteria won’t grow
above this level but are not destroyed, so systems often require
water be heated to 158
°
F (70
°
C) or above to kill any bacteria that
are present (140-160
°
F (60-71
°
C) is common in commercial
kitchens). This temperature causes the water to become more
aggressively corrosive, shortening the tank’s service life, so the
commonly recommended storage temperature is 140
°
F (60
°
C).
These temperatures have the potential to scald with enough
exposure time, so thermostatic mixing valves that temper water
to safe levels should be provided. Such valves are required in
some jurisdictions. Storing and mixing water to cooler levels also
increases the effective storage volume, maximizing the delivery
potential of a given tank capacity.
Temperature,
°
F (
°
C)
Time for 1
st
Degree
Burn (Less Severe)
Time for 2
nd
or 3
rd
Degree Burn
110 (43)
High-end of Normal Shower Temperatures
116 (47)
35 Minutes
45 Minutes
122 (50)
1 Minute
5 Minutes
131 (55)
5 Seconds
25 Seconds
140 (60)
2 Seconds
5 Seconds
149 (65)
1 Second
2 Seconds
154 (68)
Instant
1 Second
Part 2 – Installation
2.1
– Checking the Equipment
Check for signs of shipping damage upon receiving equipment.
Pay particular attention to the powder coat stainless finish outer
shell, which may show signs of being hit or otherwise being
mishandled. Verify total number of pieces shown on packing slip
with those actually received. In case there is damage or a
shortage, immediately notify freight carrier. Pump assembly
ships lose with the unit which needs to be installed in the field.