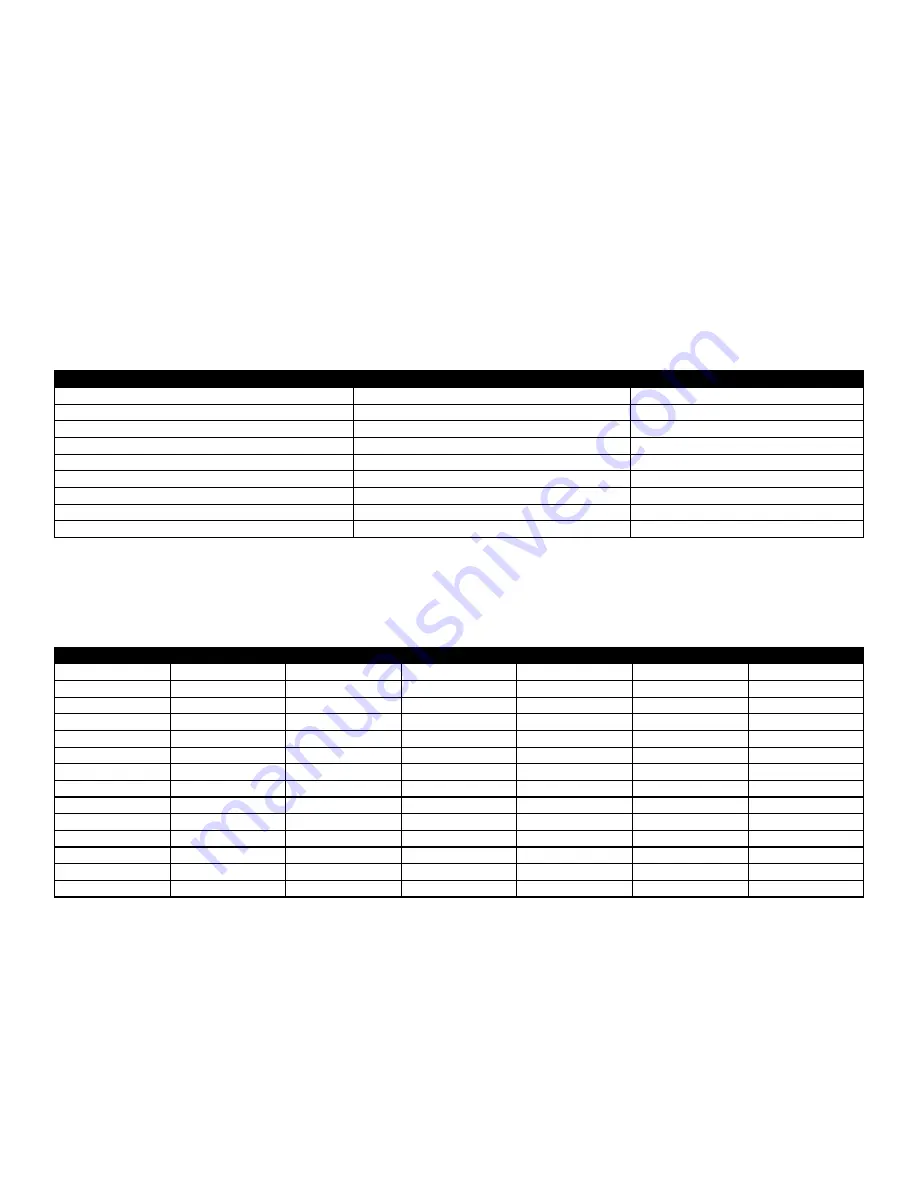
18
PART 3 GAS CONNECTIONS
Verify that the appliance is supplied with the type of gas specified on the rating plate. Consult factory for installations at high altitude.
3.1
GAS CONNECTION
Safe operation of unit requires properly sized gas supply piping. See gas line sizing data.
Gas pipe size may be larger than appliance connection.
Installation of a union at the appliance gas line connection is required for ease of service and removal of the gas train.
Install a manual main gas shutoff valve, outside of the appliance gas connection as required by local codes.
A trap (drip leg) MUST be provided in the inlet gas connection to the appliance.
Optional gas controls may require routing of bleeds and vents to the atmosphere, outside the building when required by local
codes.
Larger models of this appliance may be supplied with a gas pressure relief valve. This valve is designed to relieve lockup
pressure in excess of the high gas pressure switch setting. It must be piped to discharge excess gas pressure through the valve
to a safe location in accordance with local codes. Follow table 5 for sizing the vent line.
Table 5: Gas Pressure Relief Valve
– Vent Manifold Sizing Chart
Size of Combined Vent Line (Sch. 40 pipe)*
Qty of Pressure Relief Valves being combined
Pressure Relief Valve Size
– ¾” NPT
Pressure Relief Valve Size -
1” NPT
1
¾”
1”
2
1”
1 ¼”
3
1 ¼”
1 ½”
4
1 ¼”
2”
5
1 ½”
2”
6
1 ½”
2”
7
2”
2 ½”
8
2”
2 ½”
*Up to 50 feet. Increase by one pipe size for every 50 feet or part thereof that the vent line extends beyond the initial 50 feet. The
increase is to be made at the connection to the relief valve.
Table 6: Recommended Gas Pipe Size
Single Appliance Installation (For distance from natural gas meter or propane second stage regulator)
Input
0-100 feet
101-200 feet
201-300 feet
Btu/Hr x 1000
NAT.
L.P.
NAT.
L.P.
NAT.
L.P.
450
1 ½“
1 ¼“
2“
1 ½“
2“
1 ½“
600
1
½“
1 ¼“
2“
1 ½“
2“
1 ½“
800
2 “
1 ½“
2“
1 ½“
2 ½”
2”
1000
2 “
1 ½“
2“
1 ½“
2 ½”
2”
1200
2”
1 ½“
2 ½”
2”
2 ½”
2”
1400
2 ½”
2”
2 ½”
2”
3”
2 ½”
1600
2 ½”
2”
3”
2 ½”
3”
2 ½”
1800
2 ½”
2”
3”
2 ½”
3”
2 ½”
2000
2 ½”
2”
3”
2 ½”
3”
2 ½”
2500
3”
2 ½”
3”
2 ½”
3 ½
”
3”
3000
3”
2 ½”
3”
2 ½”
3 ½”
3”
3500
3”
2 ½”
3 ½”
3”
4”
3 ½”
4000
3 ½”
3”
4”
3 ½”
4”
3 ½”
3.2
GAS PIPING
All gas connections must be made with pipe joint compound resistant to the action of liquefied petroleum and natural gas. All piping must
comply with local codes and ordinances.
Summary of Contents for ADVANTUS AVH 1000
Page 2: ......
Page 3: ......
Page 38: ...31 Figure 23 Recommended Piping with Reverse Return and Variable Primary Flow...
Page 88: ...81 PART 12 EXPLODED VIEW Figure A...
Page 89: ...82 Figure B FAN BURNER ASSEMBLY AV500 600 some items may not be as shown...
Page 90: ...83 Figure C FAN BURNER ASSEMBLY AV800 4000 some items may not be as shown...
Page 91: ...84 Figure D Figure E...
Page 92: ...85 Figure F Figure G...
Page 93: ...86 Figure H CONTROL BOARD ASSEMBLY...
Page 100: ...93 PART 13 ELECTRICAL DIAGRAMS...
Page 101: ...94...
Page 102: ...95...