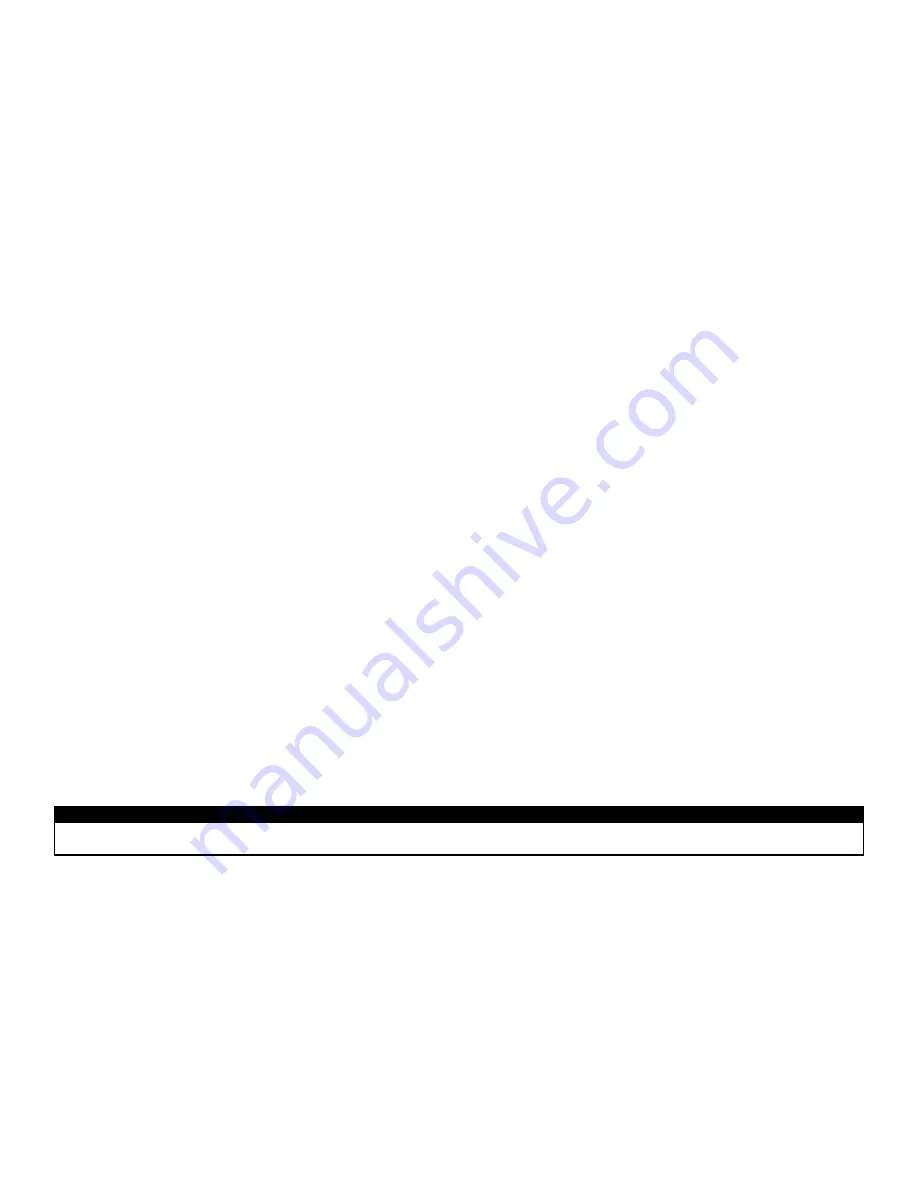
5
1.7
REMOVAL OF EXISTING APPLIANCE
When an existing appliance is removed from a common venting system, the common venting system is likely to be too large for proper
venting of the appliances remaining connected to it. At the time of removal of an existing appliance the following steps must be followed
with each appliance remaining connected to the common venting system placed in operation, while the other appliances remaining
connected to the common venting system are not in operation.
Seal any unused opening in the common venting system.
Visually inspect the venting system for proper size and horizontal pitch and determine that there is no blockage, restriction,
leakage, corrosion or other deficiency, which could cause an unsafe condition.
Insofar as is practical, close all building doors and windows and all doors between the space in which the appliances remaining
connected to the common venting system are located and other spaces of the building. If applicable, turn on the clothes dryers
and any appliances not connected to the common venting system. Turn on any exhaust fans, such as range hoods and bathroom
exhausts, so they will operate at maximum speed. Do not operate a summer exhaust fan. Close fireplace dampers.
Place in operation the appliance being inspected. Follow the lighting instructions. Adjust thermostat so that the appliance
operates continuously.
If provided, test for spillage at the draft control device relief opening after 5 minutes of main burner operation. Use a cold mirror,
the flame of a match, or candle or smoke from a cigarette.
After it has been determined that each appliance remaining connected to the common venting system properly vents when
tested as outlined above, return doors, windows, exhaust fans, fireplace dampers and any other gas-burning appliance to their
previous condition of use.
Any improper operation of the common venting system should be corrected so that the installation conforms to the National Fuel
Gas Code, ANSI Z223.1/NFPA 54 and/or the Natural Gas and Propane Installation Code, CAN/CGA B149.1, Installation Codes.
When resizing any portion of the common venting system, the common venting system should be resized to approach the
minimum size as determined using the appropriate tables in Chapter 13 of the National Fuel Gas Code, ANSI Z223.1/NFPA 54
and/or the Natural Gas and Propane Installation Code, CAN/CGA B149.1, Installation Codes.
Heat exchanger surfaces and vent piping should be checked every six months for deterioration and carbon deposits. Remove all soot or
other obstructions from chimney and flue, which might impede draft action. Replace any damaged or deteriorated parts of the venting
system.
A qualified service technician should follow this procedure when inspecting and cleaning the heat exchanger and vent pipe.
1. Turn off electrical power and main gas shut-off and allow appliance to cool down.
2. Remove the vent pipe running to the chimney and check heat exchanger, vent and chimney for obstruction and clean as
necessary.
3. Remove burner from appliance and carefully clean as required. Never brush or wipe the knitted metal fiber surface
– use a
garden hose and wash instead.
Caution: Never use a pressure washer to clean the burner.
4. Use a pressure washer to clean heat exchanger if necessary.
5. Reinstall parts removed in steps 2 and 3. Be sure that vent pipe has proper pitch and is properly sealed. Replace any damaged
gasket. Note that the burner is supplied with two gaskets; a high temperature graphite coated ceramic paper gasket under the
burner flange, and a stamped silicon gasket between the burner flange and fan flange. Tighten fan flange mounting nuts to 20
ft-lb (Models 500 & 600), 25 ft-lb (Models 800-4000).
6. Restore electrical power and gas supply to appliance.
7. Place appliance in operation using lighting instructions provided.
8. Confirm proper operation of all safety devices.
9. Check for gas leaks and proper vent operation.
NOTE
Experience has shown that improper installation or system design, rather than faulty equipment, is the cause of most
operating problems.
1.8
BOILER ROOM OPERATING CONDITION
Due to low jacket losses from the appliance, temperatures in a typical boiler room may drop significantly; supplemental heat is
required to maintain ambient temperature at acceptable levels.
Camus
Advantus
boilers and water heaters are approved at 95% efficiency and are required to be vented as a Category II or IV
condensing appliance.
1.9
CLEARANCE FROM COMBUSTIBLE MATERIAL
This appliance is suitable for alcove (a closet without a door) installation with minimum clearances to combustibles as follows:
Summary of Contents for ADVANTUS AVH 1000
Page 2: ......
Page 3: ......
Page 38: ...31 Figure 23 Recommended Piping with Reverse Return and Variable Primary Flow...
Page 88: ...81 PART 12 EXPLODED VIEW Figure A...
Page 89: ...82 Figure B FAN BURNER ASSEMBLY AV500 600 some items may not be as shown...
Page 90: ...83 Figure C FAN BURNER ASSEMBLY AV800 4000 some items may not be as shown...
Page 91: ...84 Figure D Figure E...
Page 92: ...85 Figure F Figure G...
Page 93: ...86 Figure H CONTROL BOARD ASSEMBLY...
Page 100: ...93 PART 13 ELECTRICAL DIAGRAMS...
Page 101: ...94...
Page 102: ...95...