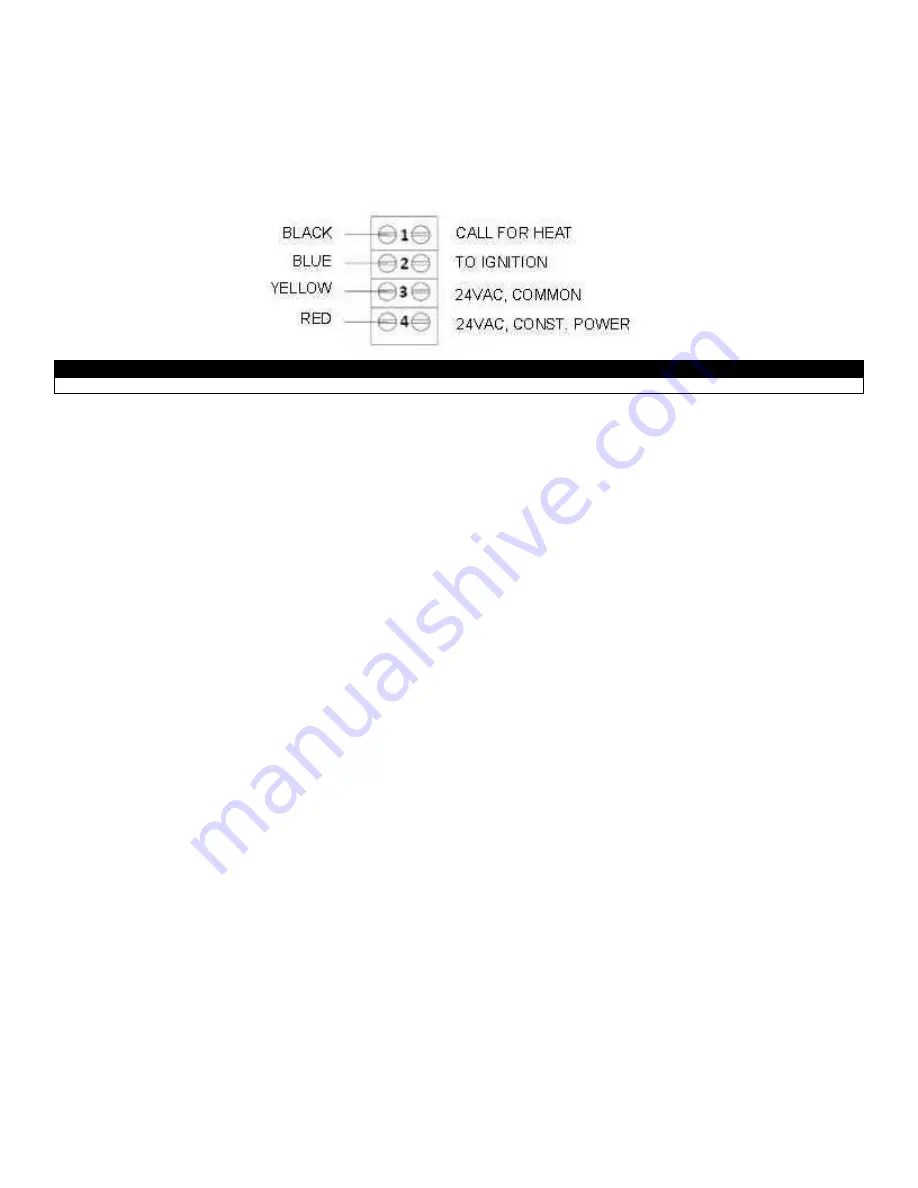
12
2.1.7
AIR INLET DAMPER
In cold climates, it is essential to provide a motorized air
Inlet Damper
to control the supply of combustion air and prevent nuisance
condensation. Each air
Inlet Damper
is designed to serve only one appliance and it must be electrically wired to the Air
Inlet Damper
Connection inside the junction box. All electrical wiring must be done in accordance with the requirements of the authority having
jurisdiction or, in the absence of such requirements, with National Electrical Code, ANSI/NFPA70 and/or the Canadian Electrical Code
part 1 CSA C22.1.
A minimum clearance of not less than 6” (152 mm) between the air
Inlet Damper
and combustible construction must
be maintained for service of the vent damper device.
Figure 7: Air Inlet Damper Connection inside J-Box
NOTE
Damper must be in open position when appliance main burner is operating.
2.1.8
MASONRY CHIMNEY INSULATIONS
Always follow local codes when venting this appliance into a masonry chimney. A standard masonry chimney must NOT be used to vent
the products of combustion from the flue of a condensing, positive or negative pressure appliance (Category II or IV). If a masonry
chimney is to be used, the chimney MUST use a sealed, corrosion resistant liner system to vent flue products from this high efficiency
appliance. Sealed, metallic, corrosion resistant liner systems (AL29-4C or equivalent, single wall or double wall, or flexible or rigid metallic
liners) must be rated for use with a high efficiency condensing, positive pressure vent system. Corrosion resistant chimney liner systems
are typically made from a high grade of corrosion resistant stainless steel such as AL29-4C or equivalent. The corrosion resistant liner
must be properly sized and fully sealed throughout the entire length. If the flue is contained within the masonry chimney, both the top
and the bottom of the masonry chimney must be capped and sealed to provide a dead air space around the sealed corrosion resistant
liner.
Consult with local code officials to determine code requirements or the advisability of using a masonry chimney with a sealed
corrosion resistant liner system.
2.1.9
VERTICAL VENTING TERMINATION
Follow Category II or IV vent termination and all General Instructions.
The vent terminal should be vertical and exhaust outside the building at least 2 feet (0.61 m) above the highest point of the roof
within a 10 foot (3.05 m) radius of the termination.
The vertical termination must be a minimum of 3 feet (0.91 m) above the point of exit.
A vertical termination less than 10 feet (3.05 m) from a parapet wall must be a minimum of 2 feet (0.61 m) higher than the parapet
wall.
2.1.10
COMBINED COMBUSTION AIR INLET
The air inlet pipes from multiple appliances can be combined to a single common connection if the common air inlet pipe has a cross
sectional area equal to or larger than the total area of all air inlet pipes connected to the common air inlet pipe.
Equivalent pipe diameter = Sq Root [(d
1
)
2
+ (d
2
)
2
+ (d
3
)
2
+ (d
4
)
2
+ ..... + (d
n
)
2
], d, pipe diameter
Example: What is equivalent pipe diameter of three air inlet pipes, 8” (20.3 cm), 10” (25.4 cm) and 12” (30.5 cm)
o
Equivalent pipe diameter = Sq Root [(8)
2
+ (10)
2
+ (12)
2
] = Sq Root (308) = 17.5”, Select 18” (82.8 cm) diameter pipe
or larger.
The air inlet point for multiple boiler air inlets must be provided with an exterior opening which has a free area equal to or greater than
the total area of all air inlet pipes connected to the common air inlet. This exterior opening for combustion air must connect directly to the
outdoors. The total length of the combined air inlet pipe must not exceed a maximum of 100 equivalent feet (30.5 m). You must deduct
the restriction in area provided by any screens, grills or louvers installed in the common air inlet point. Screens, grills or louvers installed
in the common air inlet can reduce the free area of the opening from 25% to 75% based on the materials used. Calculate and compensate
accordingly for the restriction.
Summary of Contents for ADVANTUS AVH 1000
Page 2: ......
Page 3: ......
Page 38: ...31 Figure 23 Recommended Piping with Reverse Return and Variable Primary Flow...
Page 88: ...81 PART 12 EXPLODED VIEW Figure A...
Page 89: ...82 Figure B FAN BURNER ASSEMBLY AV500 600 some items may not be as shown...
Page 90: ...83 Figure C FAN BURNER ASSEMBLY AV800 4000 some items may not be as shown...
Page 91: ...84 Figure D Figure E...
Page 92: ...85 Figure F Figure G...
Page 93: ...86 Figure H CONTROL BOARD ASSEMBLY...
Page 100: ...93 PART 13 ELECTRICAL DIAGRAMS...
Page 101: ...94...
Page 102: ...95...