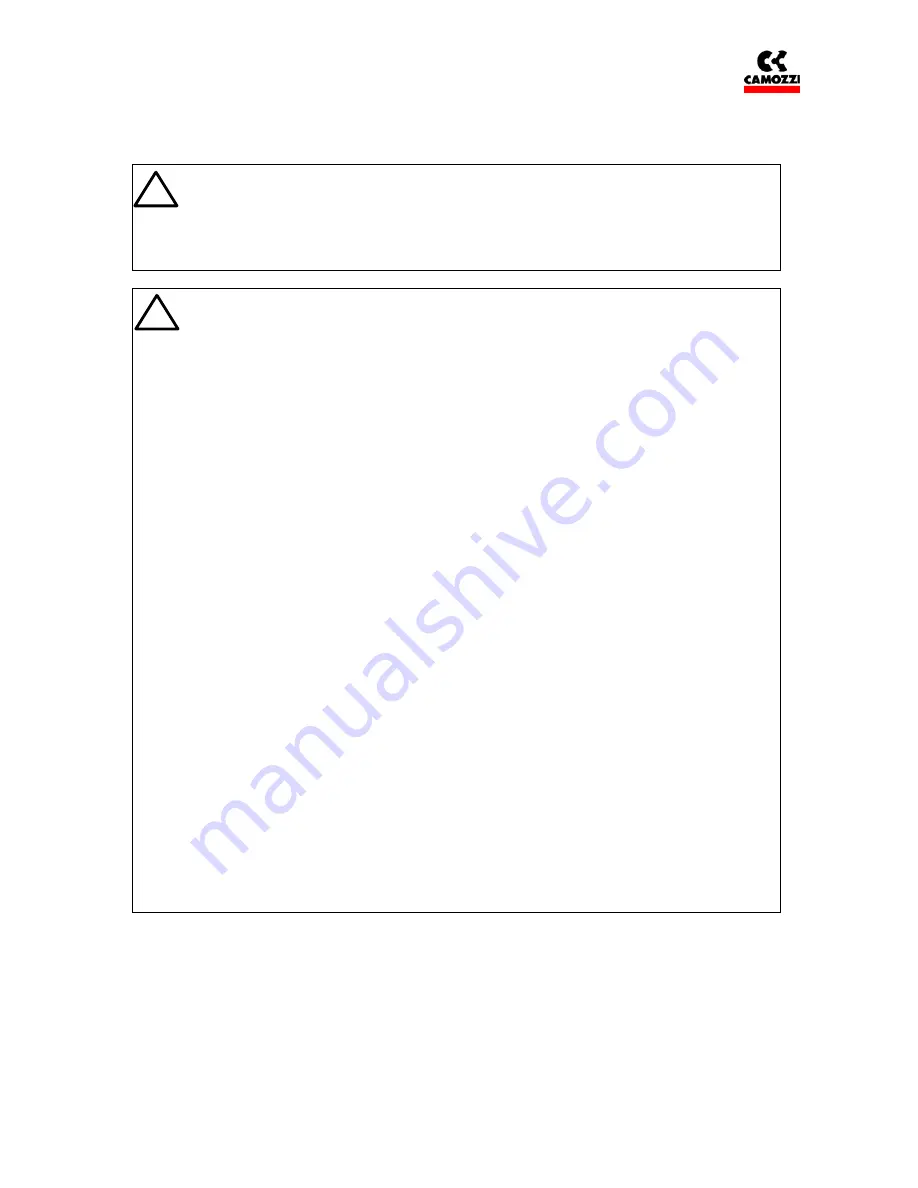
Electro-pneumatic Regulator ER100
Instruction Manual
rev. 2.0
page 33 / 38
5.
MAINTENANCE
•
Prior to maintenance work, be sure to turn the power off and remove
the compressed air supply to ensure that no residual pressure is
present.
・
These operations are the conditions required for securing operational
safety.
•
Carry out routine and periodic checking as planned so that
maintenance control is implemented correctly.
・
Unless this maintenance control is satisfactory, the product
functionality may be remarkably reduced, leading to equipment
malfunction and accidents, such as short service life, damage and
malfunctioning.
1. Pressure control to supply compressed air
・
Check to see if the set pressure is supplied.
Check to see if the pressure gauge during equipment operation is
pointing to the set pressure.
2. Pneumatic filter control
・
Check to see if drain is removed.
・
Check to see if the bowl and element fouling condition is normal.
3. Control for compressed air leak in the piping connection part
・
Check to see if the condition of the connection section especially in
the movable part is normal.
Leakage from piping may compromise correct operation.
4. Operating condition control
・
Check for operation delay and check to see if the exhaust status is
normal.
5. Control for pneumatic actuator operating condition
・
Check to see if the pneumatic actuator is working smoothly. Check
to see if the stopped condition at the stroke end is normal.
・
Check to see if the section coupled with the load is normal.
•
If an error is found during operation, turn the power off and stop the
compressed air supply immediately and stop operation.
•
Perform periodic inspection at least once every year to check for
correct operation.
•
The case is made of resin. Do not use solvent, alcohol, detergent or
other chemicals when removing dirt. They may cause damage to the
resin. Use a slightly wet cloth with neutral detergent.
!
WARNING
:
!
CAUTION
: