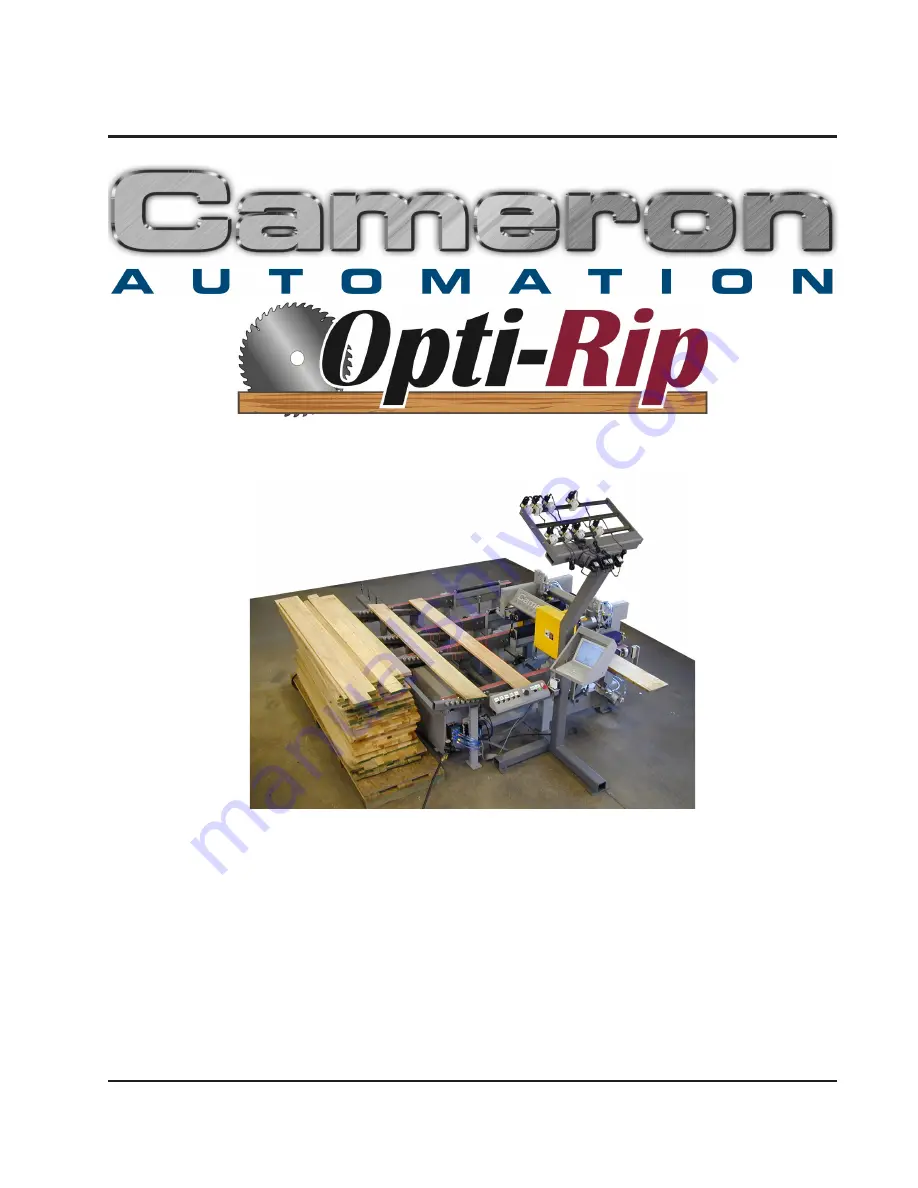
130 Salt Point Turnpike
Poughkeepsie, NY 12603
Tel: (845)-452-3780
Fax: (845)-452-0764
Email: [email protected]
Web: http://www.cameronautomation.com
Model - #415A-M1
SN -
Summary of Contents for Opti-Rip 415A-M1
Page 5: ...5 INTRODUCTION INTRODUCTION INTRODUCTION ...
Page 9: ...9 RULES FOR SAFE OPERATION RULES FOR SAFE OPERATION 415 R1 RULES FOR SAFE OPERATION ...
Page 14: ...14 INSTALLATION INSTALLATION 415 R1 8 15 18 JR INSTALLATION ...
Page 25: ...25 OPERATION OPERATION 415 R1 8 15 18 JR OPERATION ...
Page 46: ...46 OPERATION OPERATION 415 R1 8 15 18 JR ...
Page 56: ...56 TROUBLESHOOTING TROUBLESHOOTING 415 R1 8 15 18 JR TROUBLESHOOTING ...
Page 63: ...63 MAINTENANCE MAINTENANCE 415 R1 8 15 18 JR MAINTENANCE ...
Page 66: ...66 PARTS SERVICE PARTS SERVICE 415 R1 8 15 18 JR PARTS SERVICE ...
Page 69: ...69 PARTS SERVICE PARTS SERVICE 415 R1 8 15 18 JR ...
Page 70: ...70 PARTS SERVICE PARTS SERVICE 415 R1 8 15 18 JR ...
Page 71: ...71 PARTS SERVICE PARTS SERVICE 415 R1 8 15 18 JR ...
Page 72: ...72 PARTS SERVICE PARTS SERVICE 415 R1 8 15 18 JR ...
Page 73: ...73 PARTS SERVICE PARTS SERVICE 415 R1 8 15 18 JR ...