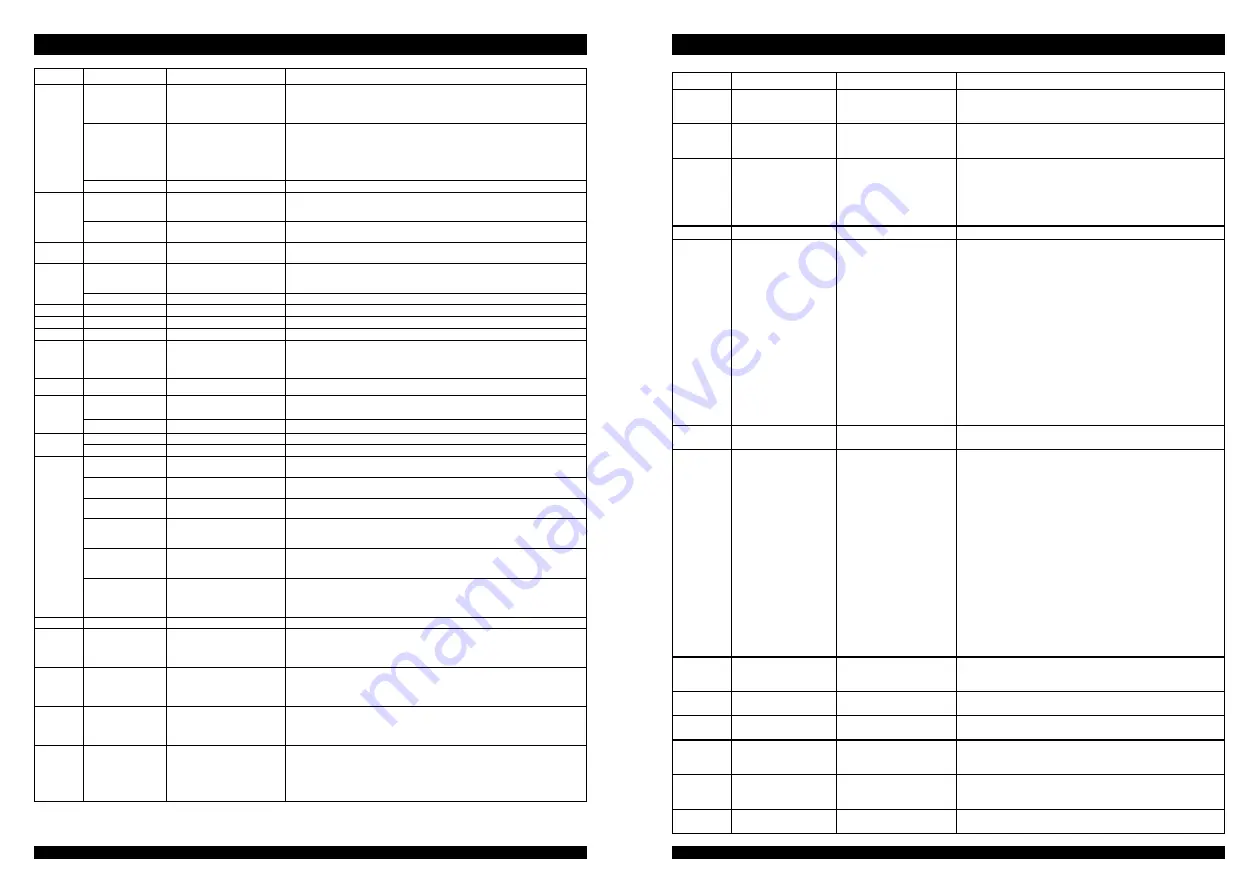
MAINTENANCE
OPERATOR MANUAL
68
EPS14P
69
OM-EPS14P2019001-EN
Display
ALARM
Fault name
Recommended inspection
02A89
POWER MOS SHORT
Short circuit of the power MOS
tube
Before the main contactor engages, the software can check the power bridge.
Convert the low end power of the MOS tube. Lower the phase voltage to –BATT (lift
to +BATT). If the phase voltage variation does not agree with the command, this
fault can occur. Replace the controller. Replace the controller.
PUMP VACC NOT OK
Oil pump lift speed regulation
sensor fault
Inspection time: With the forklift idling, the lift speed regulation sensor voltage
is at least 1V higher than the minimum set in the “PROGRAM VACC” menu for
accelerator signal range. Possible causes:
1.Upper and lower voltage limits of the lift speed regulation sensor have not been
taken. Move to the “PROGRAM VACC” menu and take them again;2.Lift speed
regulation sensor error3.Controller fault.
pev not ok
Not used in BYD system
02A90
PUMP VACC RANGE
Oil pump lift speed regulation
sensor signal is outside the
range
1. Upper and lower voltage limits of the lift speed regulation sensor have not been
correctly taken. Move to the “PROGRAM VACC” menu and take them again; 2.
Check whether the wiring of the lift speed regulation sensor is correct;
lift+lower
Trigger the lifting and lowering
at the same time
Check if the tiller switch signal is normal
02A91
lift low active
Lowering switch is triggered
The lowering switch is triggered when the vehicle is turned on, please check the
lowering switch
02A92
CURRENT GAIN
Fault with current gain
Maximum current gain is the factory set value. It indicates that the maximum
current adjustment procedure has not yet been initiated. Solution: ZAPI technician
correctly sets the current gain parameter.
canbus ko tiller
Tiller communication fault
Check CAN communication wire
02A93
wrong battery
Voltage level setting error
Check whether the battery voltage is normal.
02A94
data acquisition
Data update error
Controller parameter settings cannot be changed while the controller is working.
02A95
INPUT ERROR #2
Input error #2
02A96
ANALOG INPUT
Analogue signal input fault
This fault occurs when all analogue signals are converted into the same value by
the A/D converter, with delay exceeding 400ms. This function is used to detect
fault with the A/D converter or conversion of analogue signal. Fault analysis: If this
fault persists, replace the controller.
02A97
input error#1
Check whether A13 input is normal
02A98
reload hm from mdi
Not used in BYD system
input error#2
Check whether A14 input is normal
02A99
SLIP_PROFILE
Slip fault
“SLIP PROFILE” selection error. Check hardware parameter settings.
checkup needed
Checkup needed
Check interval is expired. Contact the service personnel to check.
06A00
STEER HAZARD
Steering angle exceeds limit
1. Reduce the steering angle and restart the key; 2. Change the internal angle
parameter setting of steering controller;
EMERGENCY
Emergency reverse
After completing the emergency reverse, engage the interlock switch again and
the fault disappears.
WAITING DATA
Waiting for data
1.Check if the CAN BUS communication line is connected properly;
2.Check if the bit rate of the communication is consistent;
EPS NOT ALIGNED
Zero not found
1.Check if the zero proximity switch is installed properly;
2.Check if the zero proximity switch is correctly selected;
3.Check if the output data of zero proximity switch is correct;
WAITING FOR TRAC
Waiting for towing controller
1.Check if the CAN BUS communication line is connected properly;
2.Check if the connection line of interlock switch is correct;
3.If the interlock switch is controlled by tiller, set TILLER SEITCH as HANDLE;
KEYOFF
Key switch voltage low
1.Check if the key switch voltage receives a low voltage pulse when turning on the
external load;
2.Check if B+ and B- are firmly connected to the controller;
3.If the fault is reported every time the key is turned on, replace the controller;
06A01
HIGH CURRENT
Current over high
1. Check if the steering controller matches the motor; 2. Replace the controller
06A02
POWER FAILURE #1
Power fault #1
1.Check if the controller fuse is normal;
2.Check if power supply cable is firmly connected to the controller;
3.Check if the controller W phase wire is connected properly;
4.Replace the controller;
06A03
POWER FAILURE #2
Power fault #2
1.Check if the controller fuse is normal;
2.Check if power supply cable is firmly connected to the controller;
3.Check if the controller U phase wire is connected properly;
4.Replace the controller;
06A04
POWER FAILURE #3
Power fault #3
1.Check if the controller fuse is normal;
2.Check if power supply cable is firmly connected to the controller;
3.Check if the controller V phase wire is connected properly;
4.Replace the controller;
06A05
STBY I HIGH
Standby current is high
Checks whether the motor current is zero via controller in the vehicle standby
state. If it is not zero, this fault occurs, stop the vehicle immediately. Possible
cause:
1. One end of the terminal is connected directly to another load rather than to a
drive motor, such as a lift motor. 2. Current sensor or logic card damaged. Replace
the logic card first. If the fault persists, replace the power part.
Display
ALARM
Fault name
Recommended inspection
06A06
D LINE SENSOR KO
Step motor D LINE voltage
failure
1.Check if the stepper motor cable is intact;
2.Resistance between D line and B- too small (Approaching
30Ω);
06A07
Q LINE SENSOR KO
Step motor Q LINE voltage
failure
1.Check if the stepper motor cable is intact;
2.Resistance between Q line and B- too small (Approaching
30Ω);
06A08
EEPROM KO
Memory is damaged
Forklift does not travel. Parameter storage becomes faulty
so that forklift stops operation. Operate the key switch for
several times. If the fault still exists, replace the logic card. If
the fault disappears, parameters previously stored have been
replaced by wrong parameters. It is imperative to set the
parameters again.
06A09
VMN NOT OK
VMN fault
Replace the controller;
06A10
HIGH TEMPERATURE
Temperature overheating
When full power is allowed, the temperature of the controller
exceeds 85 ° C (this temperature is related to the parameter
"MAXIMUM CURRENT"). Corresponding relation is as follows:
Parameter setting
Alarm temperature
MAXIMUM CURRENT=50%
96° C
MAXIMUM CURRENT=60%
94° C
MAXIMUM CURRENT=70%
92° C
MAXIMUM CURRENT=80%
90° C
MAXIMUM CURRENT=90%
88° C
MAXIMUM CURRENT=100%
86° C
At this time, the maximum current of the controller decreases
with increasing temperature. When the temperature is 105
° C, the controller current is reduced to 0. If the chopper is in
a cold state, the fault occurs: 1. The temperature calibration
parameter of logic card is incorrect. Check the parameter. 2.
The internal temperature sensor of the controller has fault. 3.
Check if the temperature sensor itself is damaged.
06A11
DATA ACQUISITION
Data collection
Activation of this fault indicates data acquisition is under
way. Wait data acquisition is completed.
06A12
LOGIC FAILURE #1
Logic card fault 1
Faults caused by under-voltage or over-voltage protection.
In 24V system, the controller detects a voltage above 45V
or below 9V; In 48V system, the controller detects a voltage
above 65V or below 11V
Possible causes:
1.Whether there is short circuit in the circuit system, such as
DC-DC, brake coil, etc., or whether the controller input power
supply is in good contact. (Driving controller)
2.Whether the battery voltage is over low or over high.
(Driving controller)
3.Check if the power cable above the terminals such as B+, B,
main contactor is tight. (Driving controller)
4.Whether the calibration parameter of controller voltage is
consistent with the actual voltage. (Driving controller)
5.Fault with the hardware circuit protected by over-voltage
on the logic card. Replace the controller. (Driving controller)
6.The voltage between W and U does not meet the
requirements, and the controller needs to be replaced;
(Steering controller)
06A13
LOGIC FAILURE #2
Logic card fault 2
The voltage between W and V does not meet the
requirements, and the controller needs to be replaced;
(Steering controller)
06A14
LOGIC FAILURE #3
Logic card fault 3
The output VU-VV of the voltage amplifier exceeds 2.2V-2.8V,
and the controller needs to be replaced; (Steering controller)
06A15
LOGIC FAILURE #4
Logic card fault #4
The output VW-VV of the voltage amplifier exceeds 2.2V-2.8V,
and the controller needs to be replaced; (Steering controller)
06A16
KS CLOSED
Safety contactor of slave
c o n t a c t o r c l o s e d i n
advance
Main contactor monitors the advanced close of safety
contactor of slave contactor, and the controller needs to be
replaced;
06A17
KM CLOSED
Safety contactor of main
c o n t a c t o r c l o s e d i n
advance
Slave contactor monitors the advanced close of safety
contactor of main contactor, and the controller needs to be
replaced;
06A18
KS OPEN
Safety contactor of slave
contactor open
Main contactor monitors the open of safety contactor of
slave contactor, and the controller needs to be replaced;
Summary of Contents for EPS14P
Page 1: ...EPS14P OPERATOR MANUAL OM EPS14P2019001 EN...
Page 2: ...EPS14P OPERATOR MANUAL OM EPS14P2019001 EN...
Page 38: ......