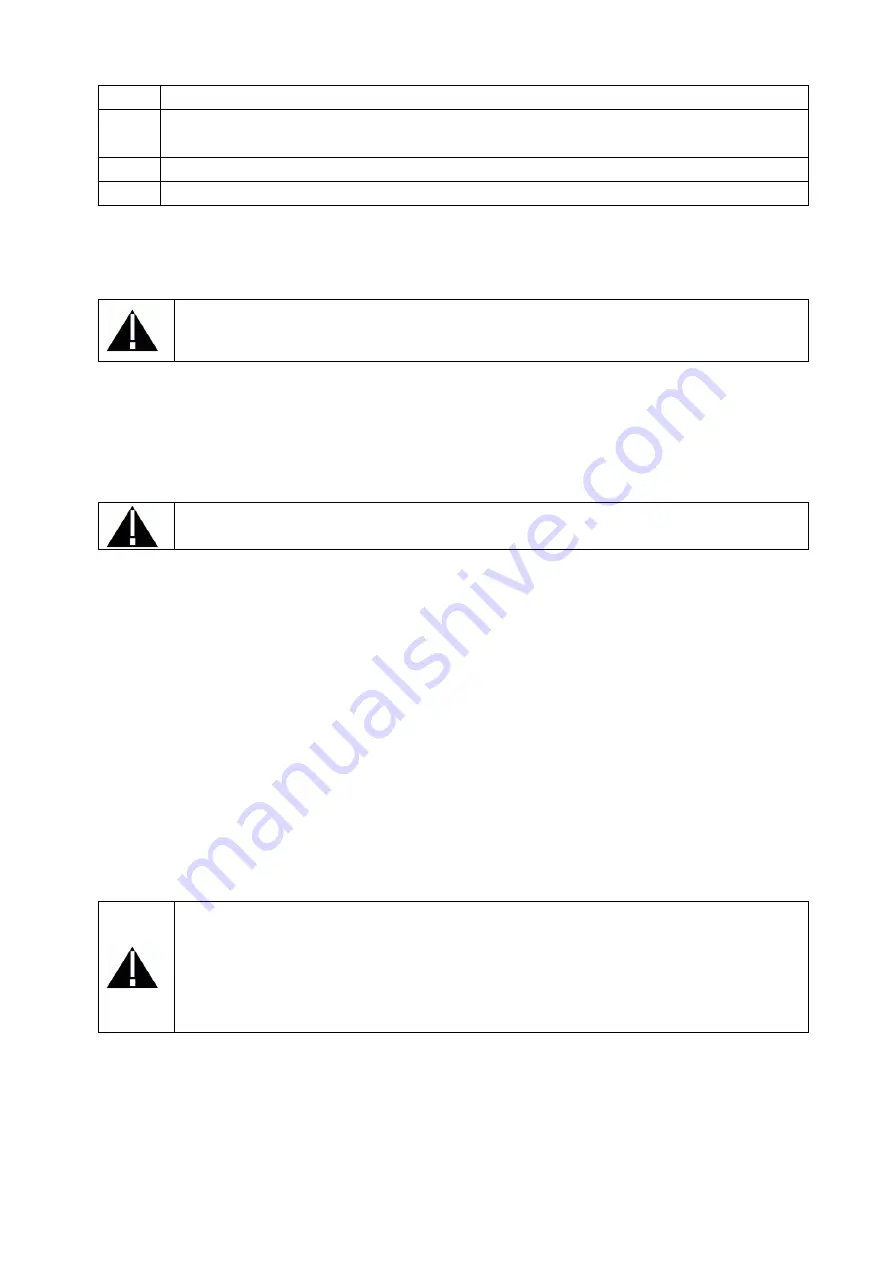
MM3156A DRUM SANDER
21
120
Medium fine: light surfacing and stock removal, thin stock dimensioning
150
Fine: minimum stock removal, finish sanding surface preparation, thin stock
dimensioning
180
Fine: finish sanding
220
Very fine: finish sanding
MAINTENANCE OF UNIT
WARNING:
To prevent possible serious personal injury, always disconnect the wide
Drum Sander from the power source before serving the unit or changing
abrasive strips.
Keep your Wide Drum Sander clean. Remove accumulated sawdust from the drum and
other working parts. Frequently clean resin buildup from the inner drum using a
kerosene or a resin remover dampened cloth with the unit disconnected from the power
source.
WARNING:
Provide adequate ventilation when using solvents. Do not use solvents to
clean plastic parts.
Some basic requirements are necessary to ensure a long and enjoyable life for your
Wide Drum Sander.
1. Periodically lubricate moving parts using a non-petroleum based lubricant, including
the threadec depth control, sliding surfaces, and bronze bushings associated with the
depth control menchanism. Do not use oil or grease because they tend to attract and
hold sawdust.
2. Periodically check the tightness of all frame bolts and motor/drum mounting
bolts/screws.
3. Keep sanding drum feed belt clean.
4. Use only clean sanding abrasives.
5. Periodically check the sanding drum feed belt table alignment. If out of alignment,
see alignment procedure.
WARNING:
Do not operate the W ide Drum Sander with the drum cover
open. Use extreme caution when performing drum cleaning maintenance on
your W ide Drum Sander. DO NOT wear long sleeve shirts, neckties, or
jewelry. Tie back long hair when cleaning the sandin drum. Failure to heed this
warning can result in serious personal injury.
DRUM ABRASIVE STRIP CLEANING
During use, the sanding strip abrasive may become clogged with sawdust, causing
insufficient sanding, marring of workpiece, and burning of the workpiece. With the
machine off and unplugged from its power source, occasionally check the condition of