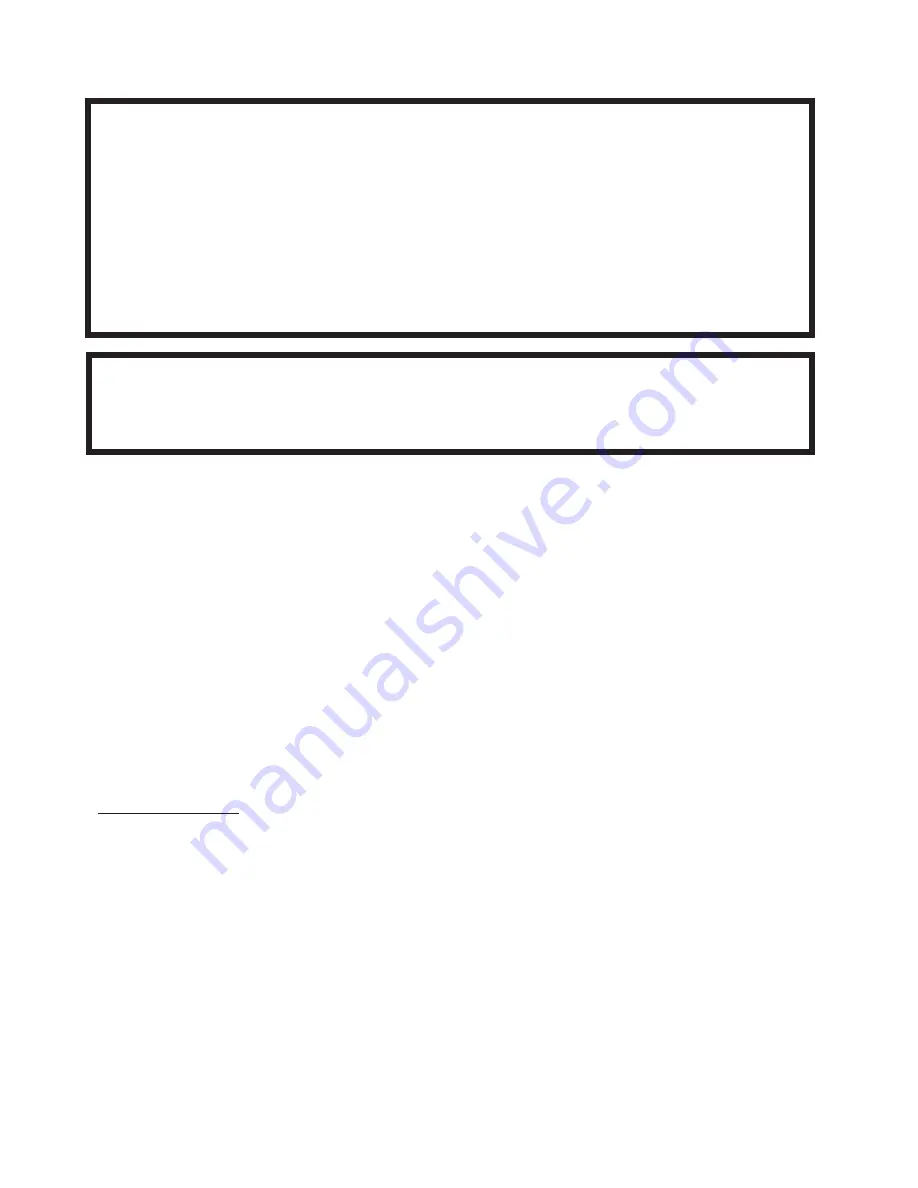
12
A. Vent System Design
There are three basic ways to vent this boiler:
•
Horizontal (“Side Wall”) Concentric Venting
- Vent system exits the building through an outside wall. Concentric
venting consists of a “pipe within a pipe”. Flue gas exits the building through the inner pipe and combustion air is
drawn into the boiler through the space between the inner and outer pipe.
•
Horizontal (“Side Wall”) Twin Pipe Venting
- Vent system exits the building through an outside wall. Combustion
air and flue gas are routed between the boiler and outdoors using separate pipes.
•
Vertical Concentric Venting
- Vent system exits the building through the roof. Concentric venting consists of a "pipe
within a pipe". Flue gas exits the building through the inner pipe and combustion air is drawn into the boiler through
the space between the inner and outer pipe.
•
Vertical Twin Pipe Venting
- Vent system exits the building through a roof. Combustion air and flue gas are routed
between the boiler and outdoors using separate pipes.
All of these systems are considered “direct vent” because in all of them, air for combustion is drawn directly from the
outdoors into the boiler. A description of all of these venting options are shown in Tables 7.1 and 7.9. For clarity, these
vent options are numbered from 1 to 6. One of the vent option columns in Tables 7.1 or 7.9 must match the planned
vent and air intake system exactly. In addition, observe the following guidelines:
1) Approved vent systems - Use only one of the approved vent systems shown in Tables 7.4a, 7.4b or 7.5. These vent
systems fall into two basic categories:
•
Concentric Vent System
- The standard boiler is supplied with a concentric vent system having a maximum usable
length of 25” (Figure 2.1). For longer runs, additional straight lengths and elbows are available from U.S. Boiler. In
some cases, larger diameter concentric pipe must be used. Each U.S. Boiler concentric vent component consists of an
inner pipe of polypropylene and the outer pipe of steel. Integral gaskets on each concentric fitting provide a gas tight
seal. A list of all U.S. Boiler concentric vent components is shown in Tables 7.4a or 7.4b.
In this manual, concentric pipe sizes are called out in terms of the inner and outer pipe nominal diameters in
millimeters. For example, “60/100mm” pipe consists of a 60mm exhaust pipe inside a 100mm diameter outer pipe.
•
Twin Pipe Vent Systems
- Approved vent systems are made of a special stainless steel alloy (AL29-4C) for protection
against corrosive flue gas condensate. They are designed to provide a gas tight seal at all joints and seams so that flue
gas does not enter the building. Each approved vent system has a unique method for installation -
do not attempt to
mix components from different vent systems
. A list of approved twin pipe vent systems is shown in Table 7.5. Note
that a special vent collar (U.S. Boiler P/N 101004-01) is required if the boiler is to be vented with one of the approved
stainless vent systems.
VII Venting
Warning
FailurE TO VEnT THis bOilEr in aCCOrDanCE WiTH THEsE insTruCTiOns COulD
CausE FluE gas TO EnTEr THE builDing rEsulTing in sEVErE PrOPErTY DaMagE,
PErsOnal inJurY, Or DEaTH:
* Do not attempt to vent this boiler with galvanized, PVC, or any other vent system not listed in
Tables 7.a or 7.b.
* Do not attempt to mix components from different approved vent systems.
* Do not obtain combustion air from within the building.
* Do not install a barometric damper or drafthood on this boiler.
CauTiOn
Moisture and ice may form on the surfaces around the vent termination. To prevent
deterioration, surfaces should be in good repair (sealed, painted, etc.)
Summary of Contents for FREEDOM
Page 8: ...8 Figure 1 Wall Mounting Hole locations ...
Page 9: ...9 Figure 5 2 Boiler Mounting Hardware ...
Page 11: ...11 Figure 6 1 Boiler Installed In A Confined Space Ventilation Air From Inside ...
Page 42: ...42 FIGURE 7 51 CONDENSATE PIPING ARRANGEMENT ...
Page 55: ...55 Figure 10 1 Wiring Connections Diagram ...
Page 56: ...56 Figure 10 2 Ladder Diagram ...
Page 57: ...57 Figure 10 3 Wiring of Isolation Relay for Control of Two Heating Circulators ...
Page 60: ...60 FCM Series Lighting and Operating Instructions ...
Page 66: ...66 FIGURE 12 2 BASIC MENU TREE ...
Page 75: ...75 ...
Page 77: ...77 ...
Page 79: ...79 ...
Page 80: ...80 ...
Page 81: ...81 ...
Page 83: ...83 150 151 152 153 154 155 ...
Page 84: ...84 156 157 158 159 160 161 ...
Page 85: ...85 162 ...