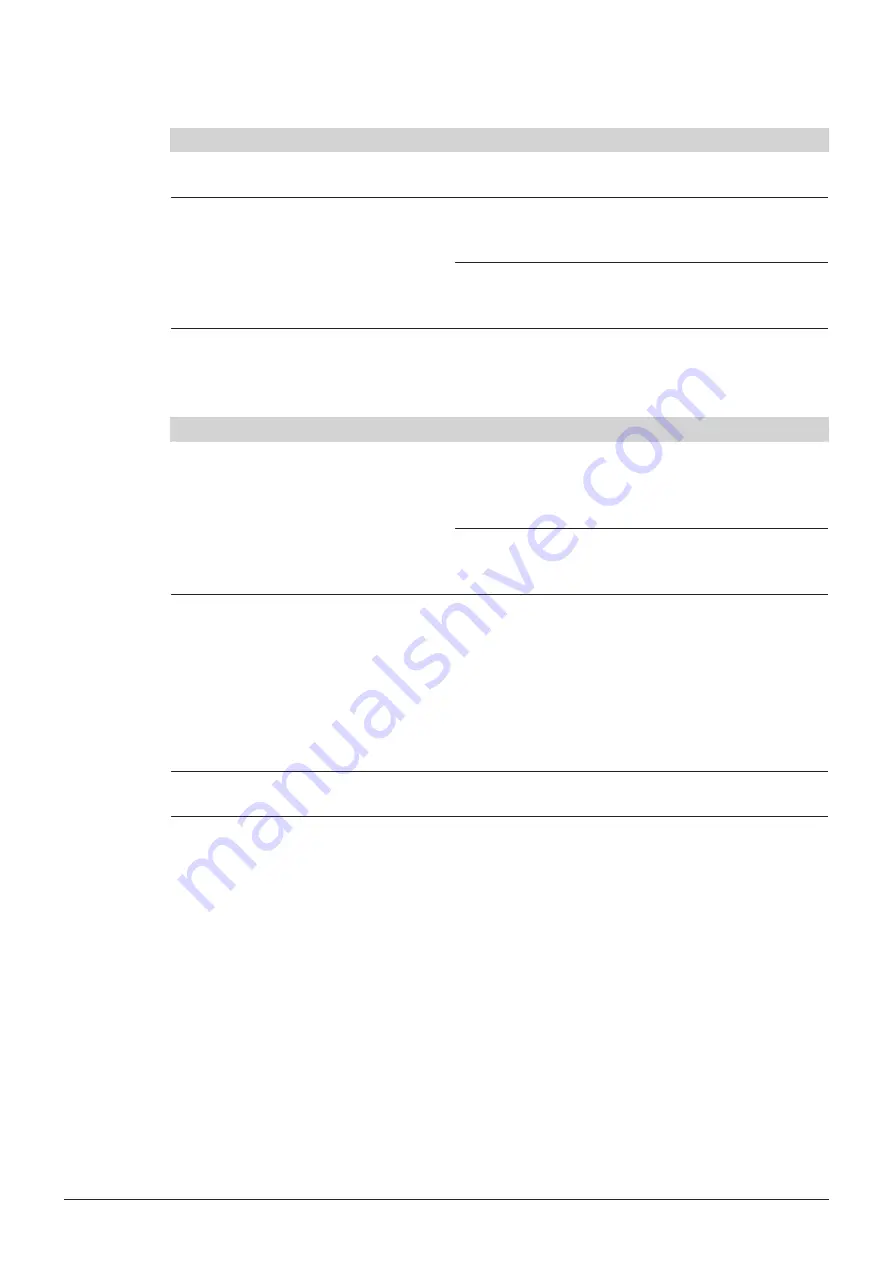
4 Description of function
25
R-220 Pro Continuous Operation Manual, Version A
Vacuum / gas circuit
1
Vacuum pump (recommended type:
Vacuum Pump V-600)
For most applications a vaccum is used to significantly reduce
the boiling point of the liquid content inside the evaporating flask
2
+
3
Aeration / inert gas inlet at the
Vacubox
The aeration valves at the optional vacuum controller and
the aeration valve of the Rotavapor
®
are used to aerate the
Rotavapor
®
Under inert conditions, both aeration inlets must be connected
to an inert gas source with regulated output pressure equal to
ambient air pressure!
4
Vacuum sensor tube at vacuum
controller
If a Vacuum Interface I-300 Pro is installed, a tube connec-
tion must be established to detect the vacuum level inside the
glassware
Cooling medium circuit
a
Chiller or cooling water tap (optional
with cooling water valve)
When a chiller is used, up to 300 liters of mains water can be
saved a day during operation In addition, higher process safety
and lower solvent emissions due to the constant, low cooling
temperature can be achieved
The cooling water valve can also significantly reduce cooling
water consumption by cutting off the water supply when no
cooling is necessary
b
Water flow sensor
Detects cooling water flow when installed
c
Flow reducing valve
The valve can be used to reduce the cooling water flow to
achieve the best cooling to water consumption ratio
Cooler(s)
Depending on the type of glassware configuration, one or more
coolers can be connected in serial
Cooling water output to sink / return
loop to chiller
The warmed cooling water can be disposed of into a sink or
reused in a closed cooling cycle when a chiller is used
Replenishment water tap
For safety reasons the replenishment water tap must not be
connected when a heating medium different to water is used!