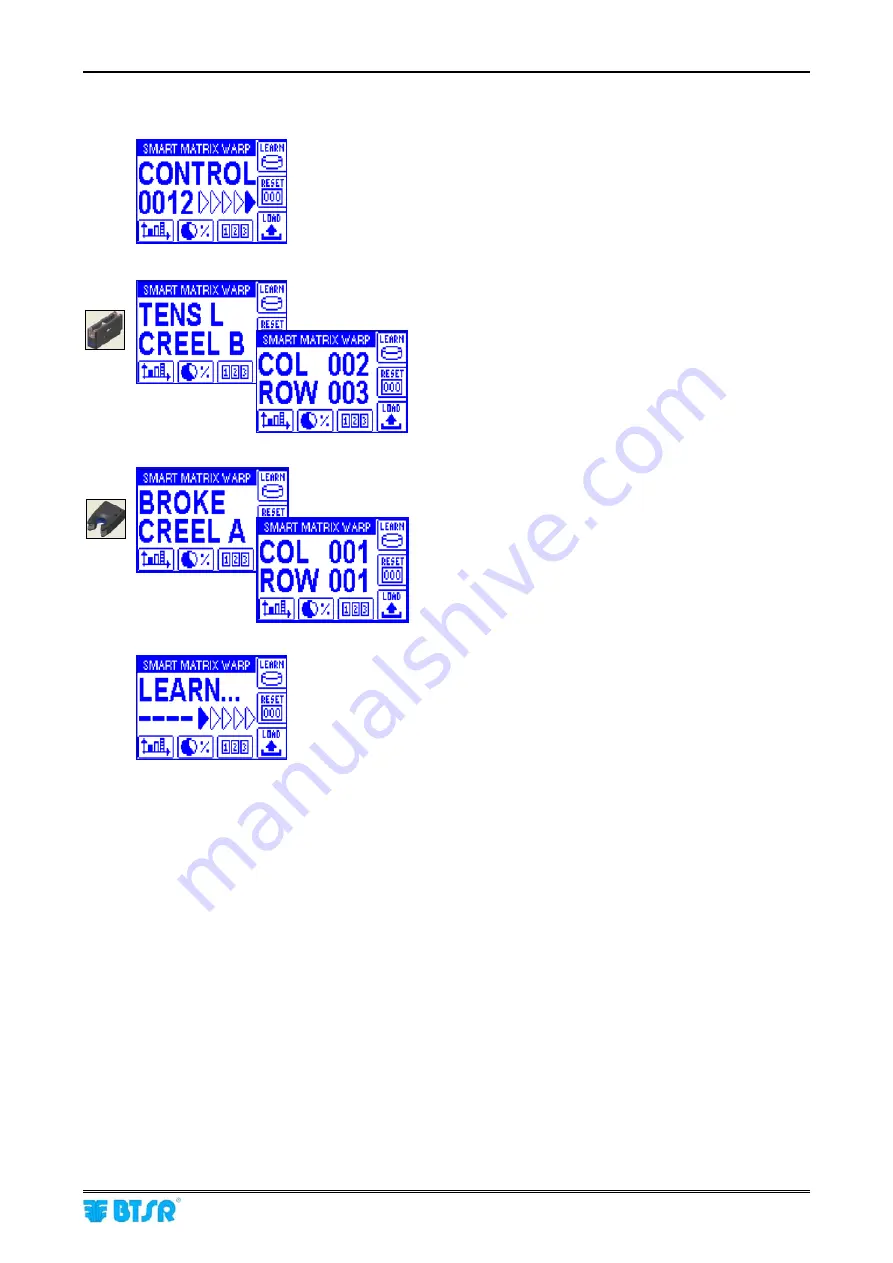
SMART MATRIX WARP Operation
SMART MATRIX
- 2-8 -
Interpretation of Operating Screens
•
System working in Control status
•
No errors detected!
•
0012 = 12 active sensors
•
Tension Low error (
TENS L
) on
CREEL B
•
Coordinates of sensor that detected the error:
Column 2 (
COL 002
)
Row 3 (
ROW 003
)
•
Yarn Broken Error (
BROKE
) on
CREEL A
•
Coordinates of sensor that detected the error:
Column 1 (
COL 001
)
Row 1 (
ROW 001
)
•
Learning in progress!
At the end of the learning process, the number of detected sensors will
appear instead of
----
.
For more details about Error images, please refer to paragraph “SMART MATRIX Error Messages”
on Section 2.
Summary of Contents for SMART WARP
Page 1: ...SMART MATRIX WARP Operating Manual ENGLISH Rev 3 0 December 2011 ...
Page 3: ...Introduction i ...
Page 4: ......
Page 9: ...Connections and Electrical Interface 1 ...
Page 10: ......
Page 21: ...Operating Instructions 2 ...
Page 22: ......
Page 79: ...System Components and Configuration 3 ...
Page 80: ......
Page 102: ...SLOW FAST Control Parameters SMART MATRIX 3 22 Page left intentionally blank ...