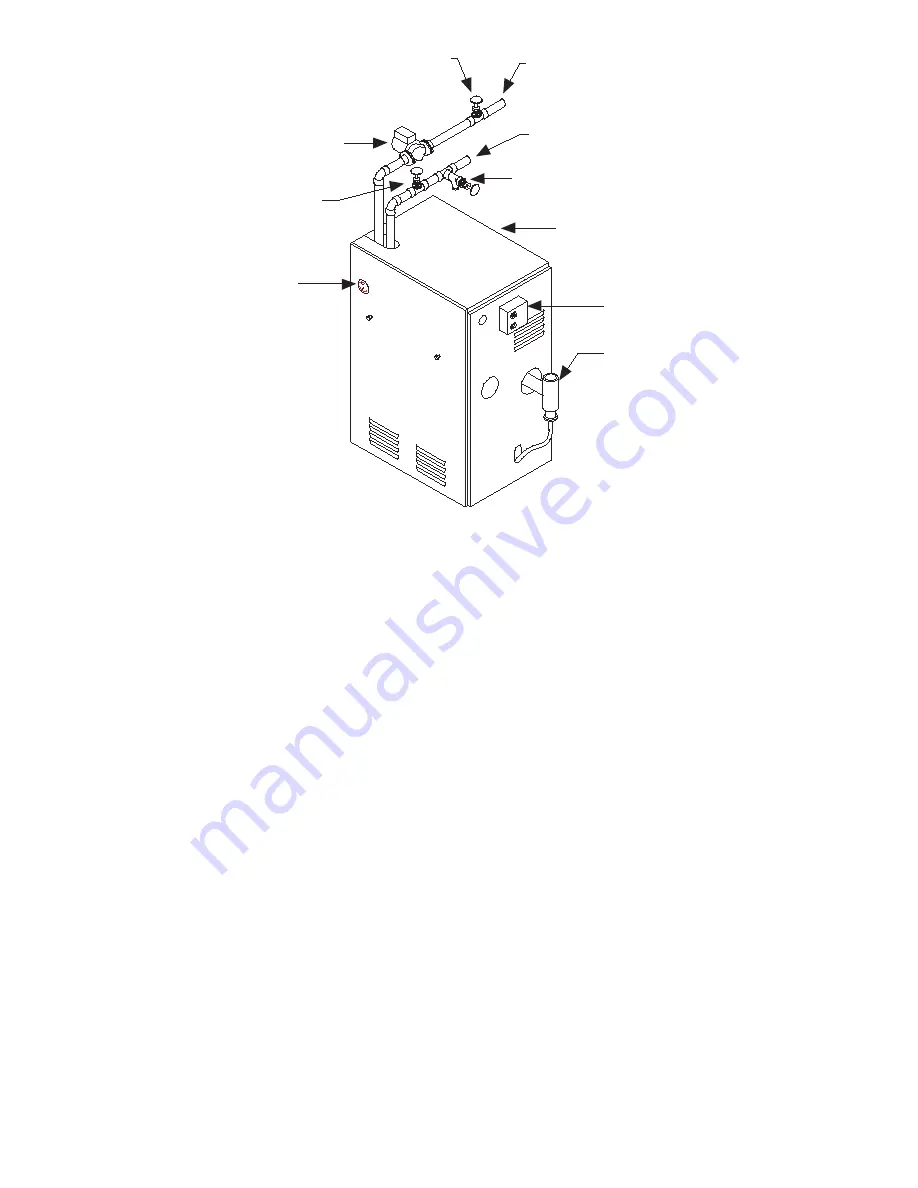
D.
Condensate Drain Piping
Condensate trap is built into boiler. External trap is not required and should NOT be used.
Provide 1/2-in. PVC Condensate drain and fittings. Condensate drain to be pitched down to floor drain at a minimum of 1/4-in. per foot.
Install furnished 1/2–in. PVC tee to overflow fitting as shown in Fig. 9.
The 1/2-in. diameter schedule 40 PVC or CPVC condensate drain piping and pipe fittings must conform to ANSI standards and ASTM D1785
or D2846. Schedule 40 PVC or CPVC cement and primer must conform to ASTM D2564 or F493. In Canada, use CSA or ULC certified schedule
40 PVC or CPVC drain pipe and cement.
A condensate pump with a reservoir (not furnished) may be used to remove condensate to a drain line (sanitary line) above boiler if a floor drain
is not available or is inaccessible.
E.
Filling Condensate Trap with Water
NOTE:
On the initial start up the condensate trap must be manually filled with water. The following are the steps required to initially fill the
condensate trap for start up, these steps are only required at the initial start up or if maintenance requires draining of the condensate trap.
1. Disconnect the vent condensate drain line from the bottom of the vent tee on the boiler.
2. Pour about 1 cup of cold tap water into the vent drain line with a proper funnel.
3. Excess water should go through the overflow and out through the condensate drain line. Verify proper operation of the drain line (or external
condensate pump if used).
4. Reinstall the vent drain line.
F.
Chilled Water Piping
The boiler, when used in connection with a refrigeration system, must be installed so the chiller medium is piped in parallel with the boiler with
appropriate valves to prevent the chilled medium from entering the boiler.
The boiler piping system of a hot water boiler connected to heating coils, located in air handling units where they may be exposed to refrigerated
air circulation, must be equipped with flow control valves or other automatic means to prevent gravity circulation of the boiler water during cooling
cycle.
PROCEDURE 4—COMBUSTION AIR AND VENT PIPE
A.
Connections and Termination
For boilers for connection to gas vents or chimneys, vent installations shall be in accordance with part 7, Venting of Equipment, of the National
Fuel Gas Code, NFPA-54-2002/ANSI Z223.1-2002 revision and applicable provisions of the local building codes.
Provisions for combustion and ventilation air must be in accordance with section 5.3, Air For Combustion and Ventilation, of the National Fuel
Gas Code, NFPA-54-2002/ANSI Z223.1-2002, or applicable provisions of the local building code.
These boilers require a dedicated direct vent system. All air for combustion is taken directly from outdoors through combustion air intake pipe.
All flue products are discharged to the outdoors through vent pipe.
Fig. 3—Single Zone Boiler Piping
A99157
SUPPLY TO
RADIATION
RETURN FROM
RADIATION
PURGE (DRAIN)
VALVE
SERVICE
VALVE*
CIRCULATOR
SERVICE
VALVE*
RELIEF VALVE
(NOT SHOWN)
DISCONNECT WITH
SERVICE OUTLET
EXHAUST TEE
WITH DRAIN
TEMPERATURE/
PRESSURE
GAUGE
*FIELD INSTALLED
—9—
→
Summary of Contents for BW9
Page 37: ...Fig 29 Troubleshooting Chart No 1 A00318 37 ...
Page 39: ...Fig 31 Troubleshooting Chart No 3 A00319 39 ...
Page 40: ...Fig 32 Troubleshooting Chart No 4 A00320 40 ...
Page 41: ...Fig 33 Troubleshooting Chart No 5 A00321 41 ...
Page 42: ...Fig 34 Troubleshooting Chart No 6 A00322 42 ...
Page 46: ...Fig 38 Boiler Block and Piping Assembly A99176 46 ...
Page 51: ... 51 ...
Page 52: ... 2003 CAC BDP 7310 W Morris St Indianapolis IN 46231 imbw9a03 52 Catalog No 63BW 9A4 ...