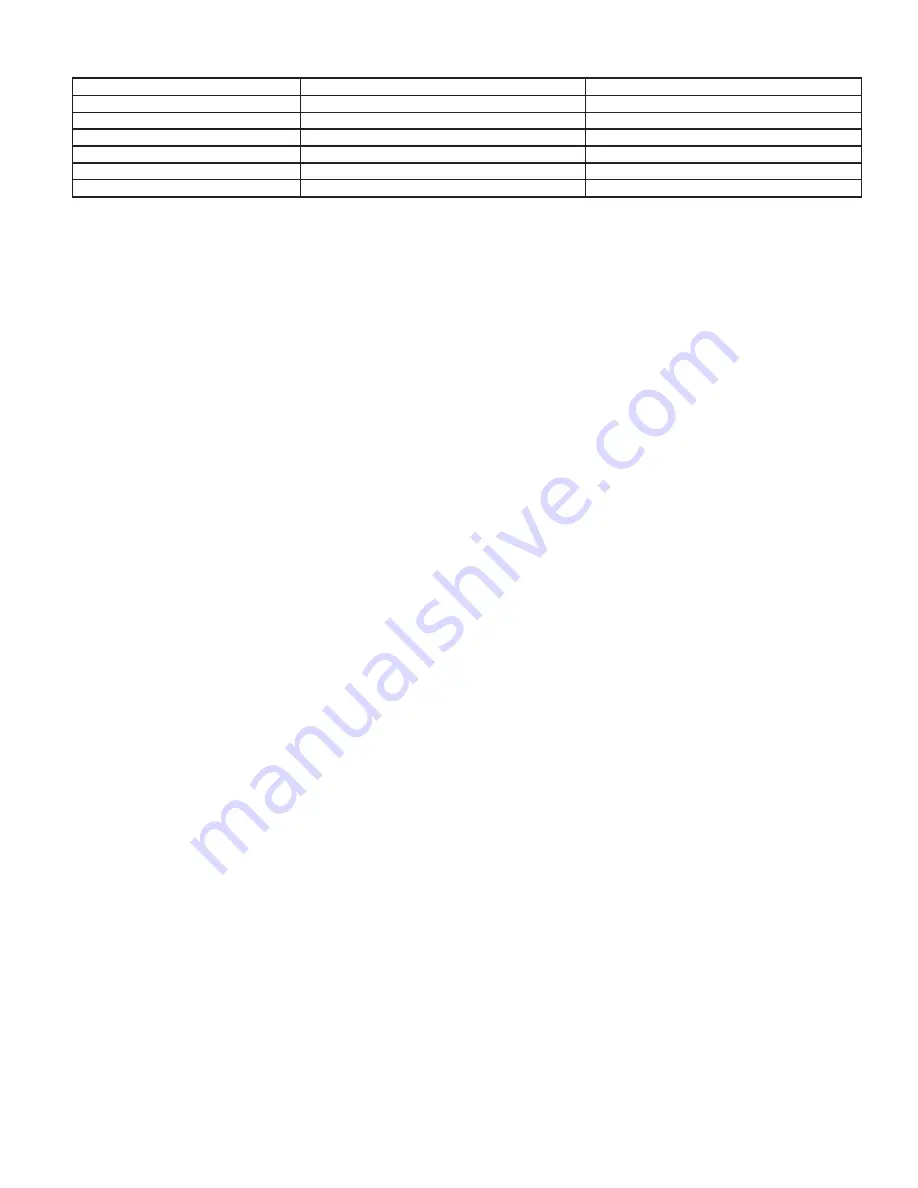
b. Once the condensate trap is emptied of water, disconnect condensate lines from the fittings on the boiler, the vent tee, and the condensate
outlet.
c. Remove the condensate trap and run cold water through the condensate lines to thoroughly flush out any sediment or debris in the lines.
d. Reinstall and connect the condensate trap, using the hose clamps to secure the various condensate lines to their fittings.
e. Follow the instructions under
″
Near Boiler Piping
″
for
″
filling condensate trap with water.
″
4. Inspection of the flue connector requires the following steps (Refer to the repair parts diagram.) Inspection of the flue connector requires
the following steps (Refer to the repair parts diagram.)
a. Loosen the clamp on the draft inducer end of the 2–in. flexible coupling that connects the vent tee to the draft inducer. Disconnect
(unplug) wiring harness from draft inducer motor and draft inducer temperature safety switch. Remove 4 bolts that attach draft inducer
to flue connector.
b. Remove draft inducer and gasket from top of flue connector.
c. Inspect interior of flue connector. Any buildup of sediment or aluminum oxide on the inside surface must be cleaned. Position the draft
inducer gasket and the draft inducer and fasten with 4 screws. Be sure to connect ground wire from draft inducer motor to one of the
four mounting screws.
d. Connect wiring harness leads to the draft inducer motor and the draft inducer temperature safety switch.
e. Connect the 2–in. flexible coupling to the draft inducer outlet.
5. Follow start-up and check-out procedures to verify proper operation.
PROCEDURE 7—DIFFERENTIAL AIR PRESSURE SWITCH CHECK
The following steps and diagram indicate the locations of the connection points required to check the differential air pressure. The differential air
pressure switch is a safety device which will prevent the boiler from firing if there is an air intake, boiler heat exchanger or vent blockage. Refer
to Table 10 and Fig. 35.
1. Turn off service switch or lower thermostat setting.
2. Remove vinyl caps from tee and 4-way connector.
3. Install testing lines as shown to inclined manometer or differential pressure gauge with the ability to read 0.01-in. to 2.00-in. w.c.
4. Turn on service switch and set thermostat to call for heat.
When pressure reading is proper and the pressure switch is operating properly, remove testing lines and reinstall vinyl caps to tee and 4-way
connector.
PROCEDURE 8—SERVICE HINTS
See Fig. 24-35.
Table 10—Differential Air Pressure Switch Setting
BOILER STATUS
DIFFERENTIAL PRESSURE (W.C.)
PRESSURE SWITCH CONNECTS
Not Running
0-in.
Normally Open
Setpoint
1.0–in. for BW9–100
1.35–in. for BW9–75
1.55–in. for BW9–50
Running without Blockage
Greater Than Setpoints
Closed
Running with Blockage
Less Than or Equal to Setpoints
Open
If manometer readings do not correspond to the chart above, check for possible causes:
—Blockage or moisture in suction lines to switch
—Blockage in air intake or vent pipes
—Undersized air intake or vent pipes
—Loose blower wheel on motor shaft
—Incorrect pressure switch or pressure switch setpoint
—31—
→
Summary of Contents for BW9
Page 37: ...Fig 29 Troubleshooting Chart No 1 A00318 37 ...
Page 39: ...Fig 31 Troubleshooting Chart No 3 A00319 39 ...
Page 40: ...Fig 32 Troubleshooting Chart No 4 A00320 40 ...
Page 41: ...Fig 33 Troubleshooting Chart No 5 A00321 41 ...
Page 42: ...Fig 34 Troubleshooting Chart No 6 A00322 42 ...
Page 46: ...Fig 38 Boiler Block and Piping Assembly A99176 46 ...
Page 51: ... 51 ...
Page 52: ... 2003 CAC BDP 7310 W Morris St Indianapolis IN 46231 imbw9a03 52 Catalog No 63BW 9A4 ...