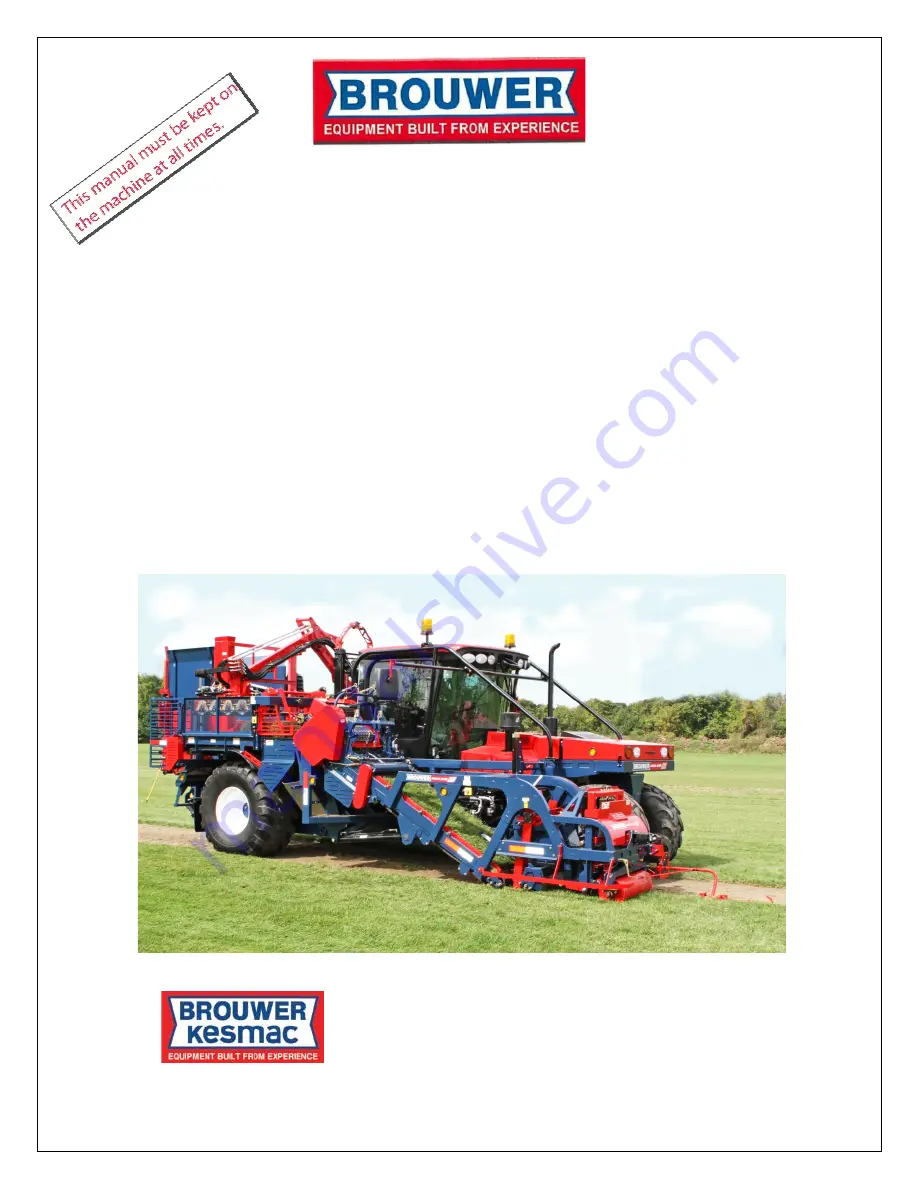
B
B
R
R
O
O
U
U
W
W
E
E
R
R
4
4
0
0
0
0
0
0
-
-
R
R
S
S
e
e
l
l
f
f
P
P
r
r
o
o
p
p
e
e
l
l
l
l
e
e
d
d
S
S
o
o
d
d
H
H
a
a
r
r
v
v
e
e
s
s
t
t
e
e
r
r
O
O
p
p
e
e
r
r
a
a
t
t
o
o
r
r
’
’
s
s
M
M
a
a
n
n
u
u
a
a
l
l
Kesmac Inc.
23324 Woodbine Avenue, Keswick Ontario Canada L4P 3E9
Tel (905) 476-6222 Fax (905) 476-6744
Web Site www.brouwerturf.com Email [email protected]
KM.99188
April 2019
Summary of Contents for 4000 R Series
Page 2: ......
Page 4: ......
Page 7: ......
Page 8: ......
Page 10: ......
Page 22: ...DECALS 1 12 ...
Page 23: ...DECALS 1 13 ...
Page 24: ...DECALS 1 14 ...
Page 25: ......
Page 26: ...1 16 ...
Page 28: ......
Page 30: ......
Page 34: ...This page left blank 2 04 ...
Page 36: ......
Page 38: ......
Page 42: ......
Page 57: ......
Page 58: ......
Page 59: ......
Page 60: ......
Page 61: ......
Page 62: ...This page left blank 3 22 ...
Page 63: ......
Page 64: ......
Page 67: ......
Page 68: ......
Page 73: ...HYDRAULIC SYSTEM Main Components Layout 4 05 ...
Page 74: ...HYDRAULIC SYSTEM ...
Page 75: ...HYDRAULIC SYSTEM Main Conveyor Hydraulic Layout 4 07 ...
Page 76: ......
Page 77: ......
Page 78: ......
Page 82: ......
Page 84: ......
Page 86: ......
Page 88: ......
Page 90: ......
Page 101: ...ELECTRICAL SYSTEM Inter Connect 5 13 ...
Page 102: ...ELECTRICAL SYSTEM Service Panel Under Cab Mount 5 14 ...
Page 103: ...ELECTRICAL SYSTEM Wiring Schematics 5 15 ...
Page 104: ...ELECTRICAL SYSTEM Wiring Schematics 5 16 ...
Page 105: ...ELECTRICAL SYSTEM Wiring Schematics 5 17 ...
Page 106: ...ELECTRICAL SYSTEM Wiring Schematics 5 18 ...
Page 107: ...ELECTRICAL SYSTEM Wiring Schematics 5 19 ...
Page 108: ......
Page 110: ......
Page 123: ...MAINTENANCE 6 13 ...
Page 126: ...LUBRICATION 6 16 ...
Page 127: ...LUBRICATION 6 17 ...
Page 128: ...LUBRICATION 6 18 ...
Page 130: ......
Page 132: ...AUTO STEER 7 02 ...
Page 133: ...AUTO STEER 7 7 03 ...
Page 136: ......
Page 139: ......
Page 140: ......
Page 141: ......
Page 142: ......
Page 143: ......
Page 144: ......
Page 145: ......
Page 146: ......
Page 147: ......
Page 148: ......
Page 149: ......
Page 150: ......
Page 151: ......
Page 152: ......
Page 153: ......
Page 154: ......
Page 155: ......
Page 156: ......
Page 157: ......
Page 158: ......
Page 159: ......
Page 160: ......
Page 161: ...ENGINE SECTION 9 Caterpillar Engine Operation and Maintenance ...