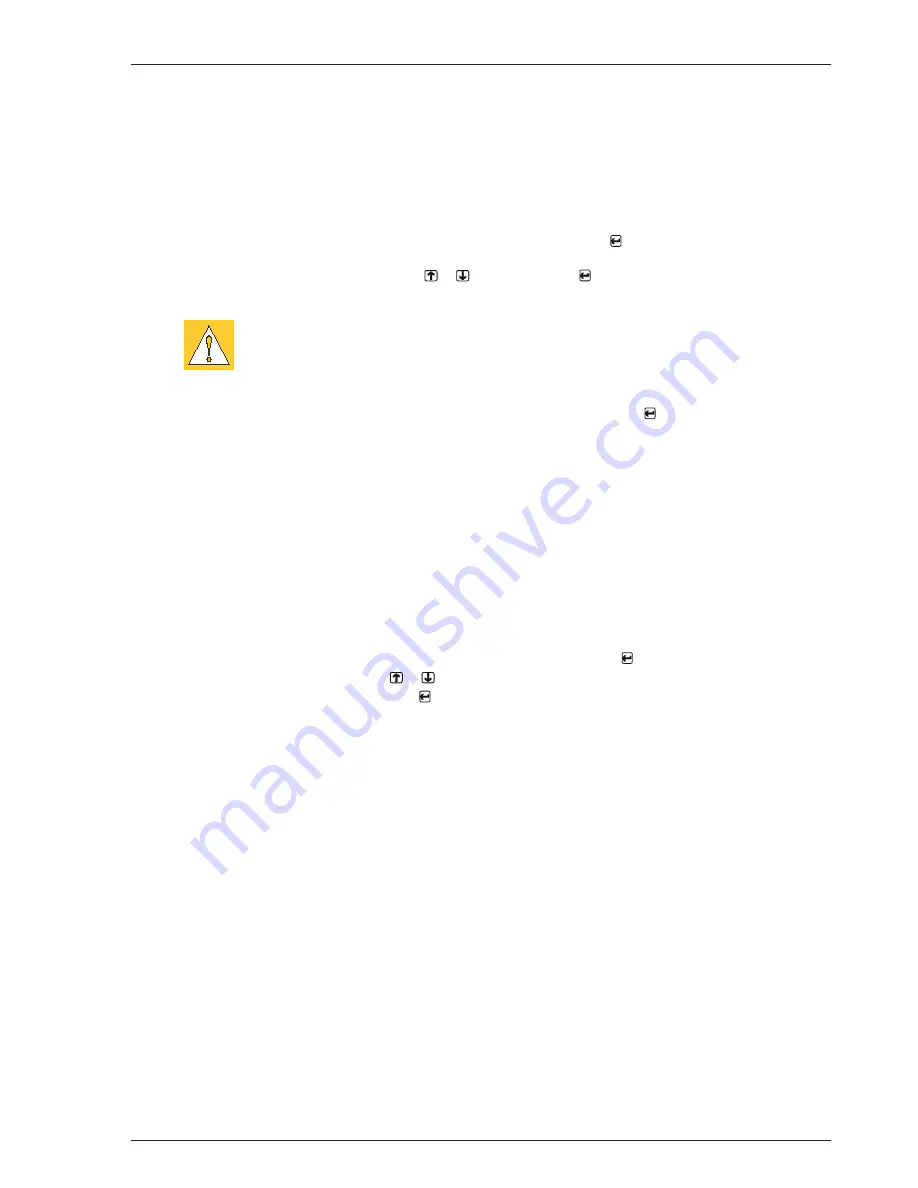
21
Printer Applicator System PAM 3600
Service Manual PAM 3600
2 Expanded Functions for Servicing
Loading the NVRAM
The "Load NVRAM" function is used to reload a previously saved printer configuration from a CompactFlash
memory module.
This function is only accessible with the service key inserted and the CF card in the slot.
Load the NVRAM as follows:
The printer is switched on.
Insert a CF card containing the stored printer configuration into the CF slot.
Insert the service key into the Master USB socket.
Select the "Load NVRAM" function in the "Service" menu and press the key.
"No" appears in the display.
Change the selection to "Yes" with the or key, and press the key.
The loading process begins and is indicated by the green LED next to the CF slot.
CAUTION!
Data loss!
Do not press the ejection key for the CF card while the green LED is lit.
5. "OK" appears in the display when the loading process has finished. Press the key again.
An error message appears in the display if a fault occurred during the loading process.
In this case, try to repeat the loading process.
If an error occurs again, you have to reset the configuration parameters of the printer individually.
Setting the Device Name
The "Set OEM Name" function is used to adapt the CPU PCB to operating in the actual printer, because the CPU
PCB is qualified for several printer types. This adjustment is necessary after replacing the CPU PCB to detect
exactly the printer type over the interfaces.
This function is only accessible with the OEM key inserted.
Insert the OEM key into the Master USB socket.
Select the "Set OEM Name" function in the "Service" menu and press the key.
Select the device name with the or key.
Confirm the selection by pressing the key.
1.
2.
3.
4.
1.
2.
3.
4.
Summary of Contents for PAM 3600
Page 1: ...Printer Applicator System PAM 3600 Service Manual Edition 1 07...
Page 74: ...A 2 Printer Applicator System PAM 3600 Service Manual PAM 3600 Appendix A Block Diagram...
Page 88: ...B 14 Printer Applicator System PAM 3600 Service Manual PAM 3600 Appendix B Circuit Diagrams...
Page 94: ...C 6 Printer Applicator System PAM 3600 Service Manual PAM 3600 Appendix C Layout Diagrams...