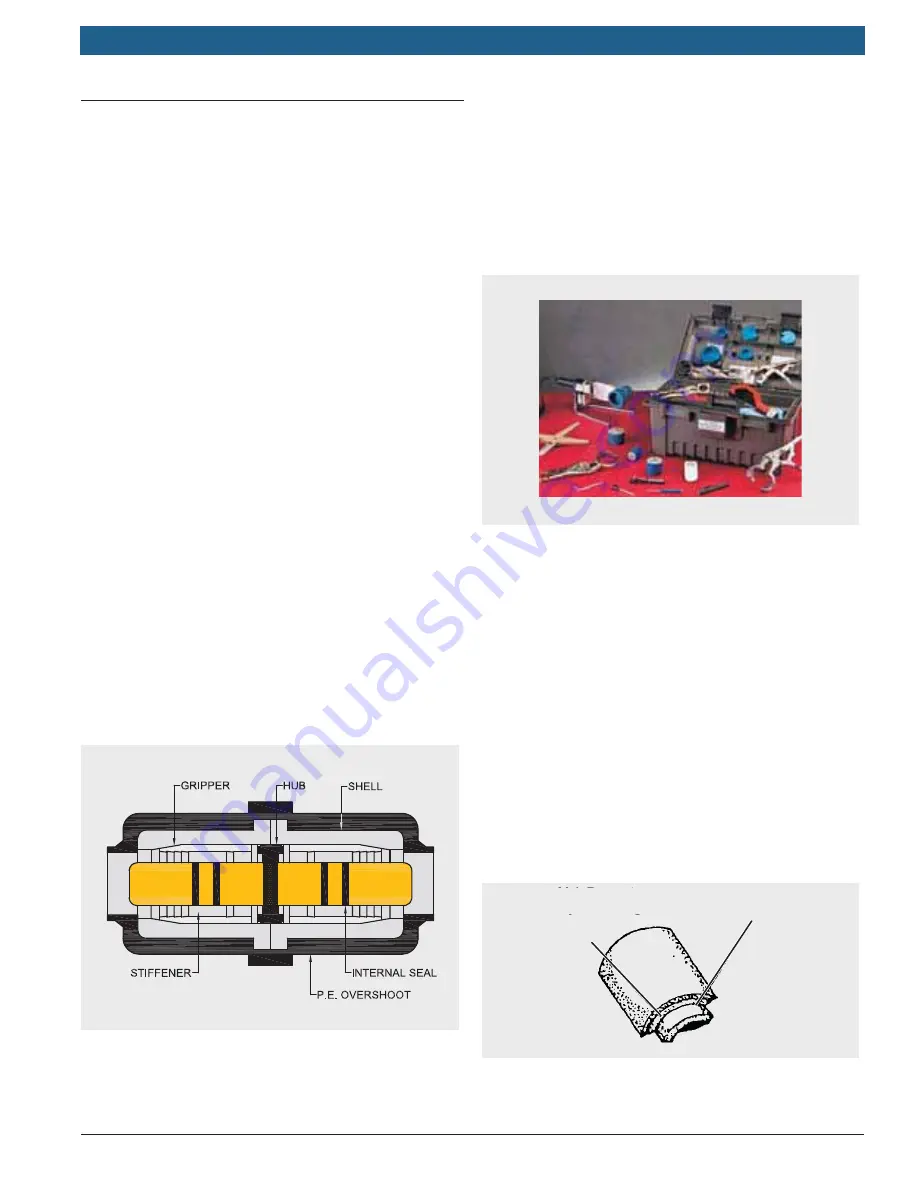
5 6 |
Bosch Geothermal Heat Pumps
Bosch Thermotechnology Corp.
Data subject to change
Applications Manual
9.7 Pipe Fusion Methods
The three basic types of HDPE pipe joining methods that
are used for earth coupled applications are socket fusion,
butt fusion, and sidewall fusion. In all processes the pipe
is melted together to form a joint. The preferred method
for 2" and smaller diameter pipe is typically socket fusion,
because it allows the tolerance of mating the pipe to be
much greater, the socket fusion joint is 3 to 4 times the
cross sectional area of a butt fusion joint in sizes under 2"
and therefore tends to be more forgiving of operator skill
level, and joints are frequently required in dif cult trench
conditions. Once the pipe diameter gets over 2", socket
fusion loses its advantages, and butt fusion is typically
the method of choice. Butt fusion requires a different
fusion machine, which is larger and less maneuverable.
All technicians doing fusion joints should be certi ed
by the pipe manufacturer or the geothermal heat pump
manufacturer, as well as IGSHPA.
Another fusion method available is Electro-fusion (EF),
where joining pipes means incorporating an electrical
heating coil. When electrically activated the welding
machine melts the surface of the pipes and/or pipes/
ttings together resulting in complete fusion.
Another more recent connection method is a compression
method referred to as the “Stab” method. The tting
used for this method features an internal seal and is an all
plastic tting that contains no metal parts (Fig. 42). This
method is approved by IGSHPA. Several manufacturers
offer these cost effective joining devices. They provide
simple assembly and only require the installer use
a chamfer tool. Note: Earth loop systems require a
hydrostatic test of typically 40-50 PSI before back lling to
test for leaks.
Fig. 42 Pipe fusion - Stab method
Courtesy of International Ground Source Heat Pump Association/Oklahoma
State University
Socket fusion joins two ends of pipe by fusing each pipe
end to a socket tting. This requires two heat fusion
procedures for each joint. This method requires the
technician to assemble the required equipment and tools
prior to fusing. Complete tool kits for socket fusion are
available (Fig. 43). These include an appropriate power
supply, a heater plate with correct socket faces, a depth
gauge, a cold ring, tubing cutters, a temperature-sensing
device, and clean, dry cotton rags.
Fig. 43 Socket fusion tool kit
The steps involved include correctly preparing the socket
fusion machine, cleaning and heating the socket faces
to the proper temperature, properly preparing the pipe
ends and ttings for fusion, using a proper depth gauge
and cold ring, simultaneously heating the pipe and tting,
properly fusing the pipe and tting and testing for leaks.
After the fusion process, and completing the speci ed
cooling and waiting time, remove the cold ring clamp
and the socket tting holder. A good joint will have a
uniform melt ring that is at against the socket tting and
perpendicular to the pipe.
Visually check the joint for uniformity and to assure no
gaps or voids exist (Fig. 44, 45). There should be no un-
bonded areas between the tting and the pipe.
Allow an additional 10 minutes undisturbed cooling time
before testing, back lling, or stressing the joint.
No Gaps or
Cavities
Melt Pressed
Against Fitting
Fig. 44 Socket fusion
Courtesy of International Ground Source Heat Pump Association/Oklahoma
State University