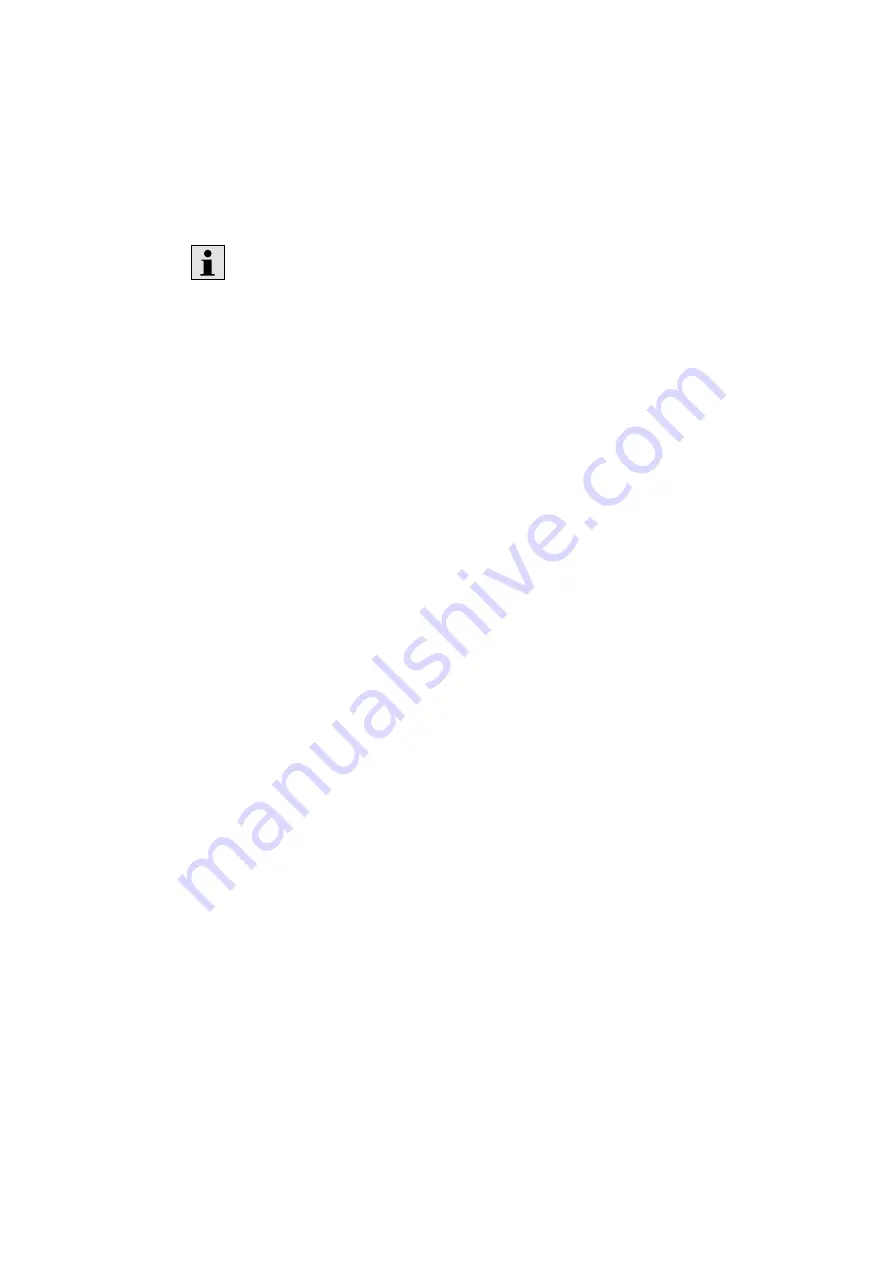
50/68 Commissioning
Bosch Rexroth AG
, A20V(L)O Series 1, RE 93100-01-B/2019-09-10
Use only a hydraulic fluid that corresponds to the following requirements:
You can find details on the minimum requirements for hydraulic fluids in
Bosch Rexroth data sheets 90220, 90221, 90222, and 90223. The titles
of the data sheets can be found in Table 1 "Required and supplementary
documentation" on page 5.
Bosch Rexroth evaluates hydraulic fluids on the basis of the Fluid Rating
according to data sheet 90235. For hydraulic fluids which have been positively
evaluated in the Fluid Rating, please refer to data sheet 90245 "Bosch Rexroth
fluid rating list for Rexroth hydraulic components (pumps and motors)". The
hydraulic fluid should be selected so that the operating viscosity in the operating
temperature range is within the optimum range (
ν
opt
; see selection diagram in the
data sheet 93100).
To ensure the functional reliability of the axial piston unit, cleanliness level 20/18/15
according to at least ISO 4406 is required for the hydraulic fluid. At a hydraulic fluid
viscosity of less than 10 mm²/s (e.g. due to high temperatures during short-term
operation) at the drain port, a cleanliness level of at least 19/17/14 according
to ISO 4406 is required. You can find details on the permissible and optimal
viscosities and admissible temperatures in data sheet 93100.
Proceed as follows to fill the axial piston unit:
1.
Place a drip tray under the axial piston unit to collect any hydraulic fluid that may
leak.
NOTICE!
Contaminated hydraulic fluid!
The cleanliness levels of commercial hydraulic fluids are usually insufficient for our
components.
▶
Use a suitable filter system to filter hydraulic fluids during filling to minimize solid
particle contamination and water in the hydraulic system.
2.
Fill and air bleed the axial piston unit via the appropriate ports; see chapter 7.3
"Installation position" on page 29. Also fill the hydraulic lines of the system.
NOTICE!
Risk of property damage due to inadequate lubrication!
Product can be damaged or destroyed!
▶
When using a shut-off valve in the suction line, make sure that the drive of the
axial piston unit can only be started when the shut-off valves are open.
▶
Dimension a shut-off valve in the suction line so that no inadmissible pressure
drop occurs in the suction area when the shut-off valve is open.
3.
If you use a shut-off valve in the suction line, only operate the axial piston unit
with opened shut-off valves.
4.
Test the direction of rotation of the drive motor. To do this, run the drive motor
briefly at the lowest rotational speed (inching). Make sure that the direction
of rotation of the axial piston unit agrees with the details of the name plate,
see chapter 5.3 "Product identification", Fig. 4: Name plate A20VO, size 520
on page 22.
Procedure