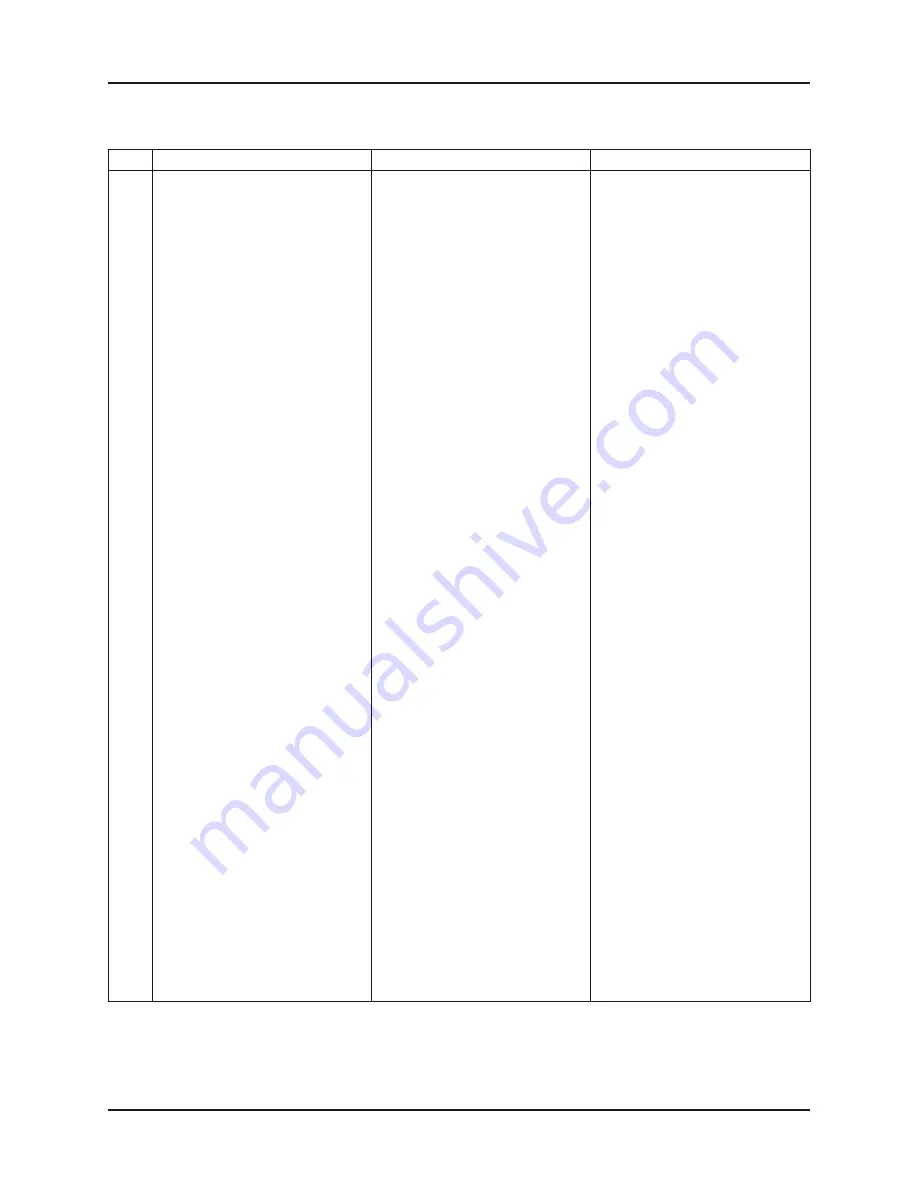
NO.
SYMP TOM
PROB A BLE CAUSE
COR REC TION
5
Com plete loss of lat eral and lon gi tu di nal
beam con trol.
(a) No volt age at coil ter mi nals, or in cor -
rect in ter nal re sis tance in coils.
(a) Check leads to coils. If the leads are
prop erly con nected and their con ti nu ity is
OK, check volt ages across both sets of
ter mi nals. If me ter in di cates a volt age
across both sets of ter mi nals, then check
in ter nal re sis tance of coils. The read ings
should be:
Lon gi tu di nal:
2.2 to 2.4 ohms
Lat eral:
3.0 to 3.2 ohms
If the read ings do not fall within these val -
ues, re place the coil as sem bly.
6
Beam spot changes po si tion as source
be comes heated.
(a) The ma te rial in the ex posed pocket is
a new slug of mag netic ma te rial such as
Ni or Fe. When heated past a value called
the Cu rie point, these ma te ri als be come
non mag netic, strongly al ter ing beam-spot
po si tion.
(a) Con trol beam po si tion man u ally when
melt ing such slugs, so that you can ob -
serve beam-spot po si tion and cor rect it af -
ter the ma te rial passes its Cu rie point.
NOTE: This phe nom e non oc curs only
the first time a slug of mag netic ma te -
rial is melted.
7
Elec tron beam spot can not be moved to -
ward rear of source along the lon gi tu di nal
axis.
(a) The source is be ing op er ated at less
than 10 kV.
(a) Mount shunt bars on source as ap pro -
pri ate (see sec tion 3.2).
8
Can not sweep en tire sur face of evaporant
ma te rial with a tight beam.
(a) The per ma nent mag net’s field is too
strong.
(a) Mount shunt bars on source as needed
(see sec tion 3.2).
9
Beam po si tion is too far to ward rear of
source.
(a) Per ma nent mag net is too weak.
(a) Check beam-spot po si tion with 0 A lon -
gi tu di nal de flec tion cur rent ap plied. If spot
is too far to ward rear of source (see Fig -
ure 6-1), re place per ma nent mag net or
have it regaussed.
(b) Leads to lon gi tu di nal coil are re versed
and coil is en er gized.
(b) If coils are con trolled by an e-beam
power sup ply or a non-bipolar beam
sweep con trol ler, make sure po lar ity of
lon gi tu di nal coil con nec tions is cor rect.
Re fer to man ual of com po nent in ques tion.
(c) Un needed shunts mounted on source.
(c) Re move shunts.
(d) Ac cel er a tion volt age is set too high.
(d) Check ac cel er a tion volt age set ting and
ad just to cor rect op er at ing value.
10
Beam po si tion is too close to emit ter as -
sem bly.
(a) Ac cel er a tion volt age is set too low.
(a) Make sure ac cel er a tion volt age is set
to the cor rect op er at ing value.
(b) Lon gi tu di nal coil is en er gized when un -
in tended.
(b) Check the out put of the de vice that
con trols the lon gi tu di nal coil.
11
Beam is highly nonuninform.
(a) Pole piece ex ten sions are not ad justed
sym met ri cally.
(a) Check po si tions of ex ten sions and ad -
just them as nec es sary (see sec tion 3.2
for in struc tions).
12
(a) Beam is too broad and dif fuse.
(a) Pole pieces are ad justed too far out.
(a) Ad just pole pieces in ward (see sec tion
3.2 for in struc tions).
13
(a) Beam is too nar row.
(a) Pole pieces are ad justed too far in.
(a) Ad just pole pieces out ward (see sec -
tion 3.2 for in struc tions).
Troubleshooting
STIH-270-2PT
0101-9004-0A
6-7