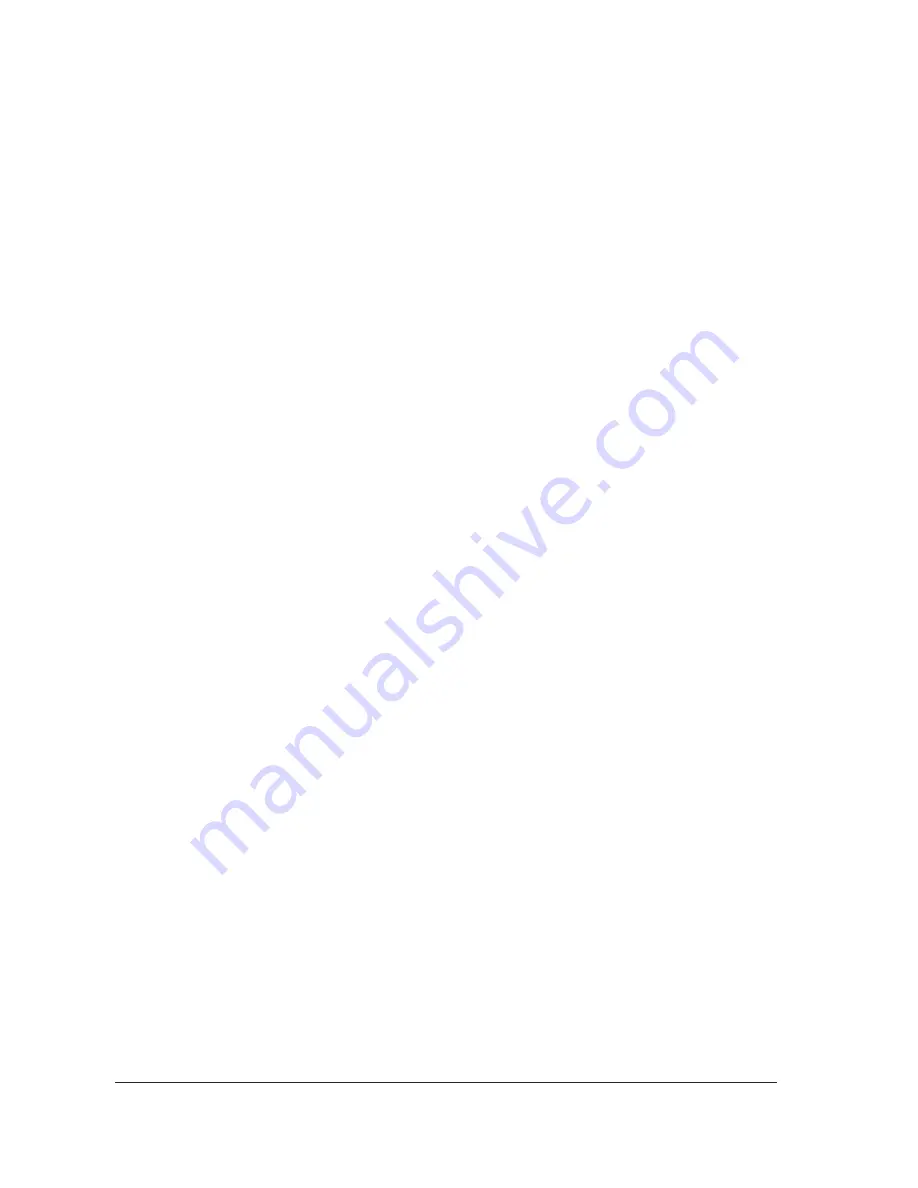
The Module has contactors for the LCDP pump and the LCMB pump (on an iL600 system),
pump power and current consumption sensors and short-circuit protection. Internal clocks and
counters in the Module measure the operating time of the iL system and keep count of the
number of iL system switch-on/switch-off and process cycles. The Module also has a
transformer and fuses for the 24 V control circuits and fuses for the following supplies: iL
Interface Module (11), emergency stop circuit (12) and d.c. electrical supply (47). Three
thermal-type, self-resetting fuses in the Electrics and Pump Control Module protect the d.c.
electrical supplies to the network.
Refer to Figure 1-4 detail D. The rear panel of the Electrics and Pump Control Module has the
following lamp and connections:
Power on lamp (7)
This lamp is on when the electrical supply to the
Electrics and Pump Control Module is on.
Tool Interface Module
connector (8)
Use this to connect an iL Tool Interface Module to the iL
system.
LON Interface Connector (9)
Use this to connect the iL system to a network.
Electrical supply connector (10)
Use this to connect your external electrical supply to the
iL system: refer to Section 3.16.3.
Protective earth (ground) stud (11)
If required, use this to make additional protective earth
(ground) connections: refer to Section 3.16.3.
GRC relay connector (12)
Not used on iL systems.
Fuse holder F7 (13)
This holds the fuse which protects the d.c. electrical
supply.
Fuse holder F9 (14)
This holds the fuse which protects the emergency stop
circuit.
Fuse holder F8 (15)
This holds the fuse which protects the iL Interface
Module (if fitted).
Refer to detail E. Fuses inside the Module (16 to 21) protect the internal circuits of the Module.
You cannot change these fuses; a BOC Edwards service engineer must change these fuses.
1-10
iL Dry Pumping Systems