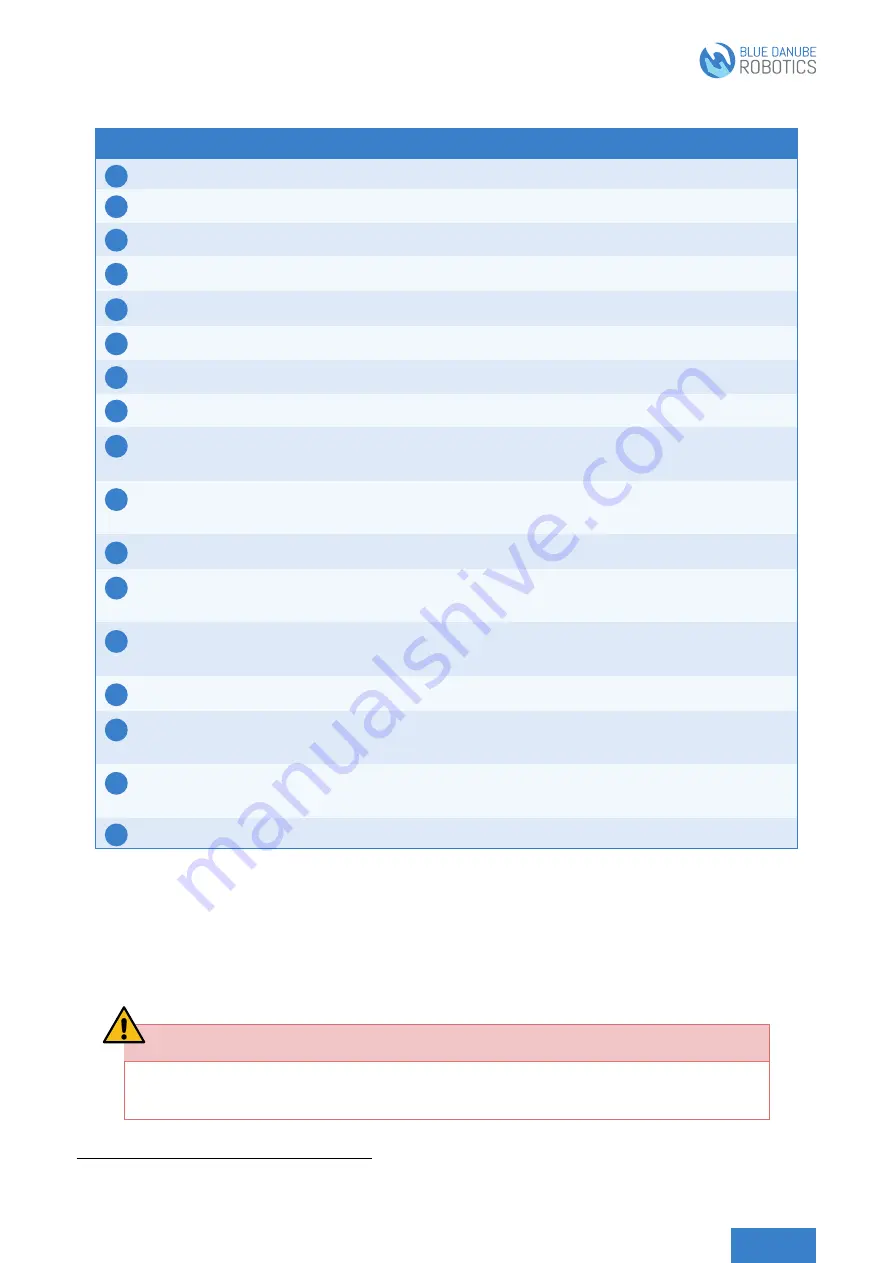
Tab. 1.1
POS. COMPONENT
UNITS
ART. NO.
M4x16 countersunk screw DIN 7991
4
2300012
Safetyflange cover
1
AS-SF1-CP
Plain bearing washer
2
2400022
Spring 1 (up to
2
.
5 kg
payload)
1
2400041
Spring 2 (
2
.
5
-
5 kg
payload)
1
2400042
Spring 3 (
5
-
7
.
5 kg
payload)
1
2400043
AIRSKIN® Safetyflange
1
–
M4x50 cylinder screw DIN 6912
4
2300013
50 mm
Robot flange adapter
(assembly pattern as specified by ISO 9409-1-50-4-M6)
1
AS-SF1-RF_50-4-M6
50 mm
Tool flange adapter
(assembly pattern as specified by ISO 9409-1-50-4-M6)
1
AS-SF1-TF_50-4-M6
M6x10 cylinder screw DIN 7984
4
2300010
31
.
5 mm
Robot flange adapter
(assembly pattern as specified by ISO 9409-1-31.5-7-M5)
1
AS-SF1-RF_31.5-7-M5
31
.
5 mm
Tool flange adapter
(assembly pattern as specified by ISO 9409-1-31.5-7-M5)
1
AS-SF1-TF_31.5-7-M5
M5x10 cylinder screw DIN 7984
7
2300011
40 mm
Robot flange adapter
(assembly pattern as specified by ISO 9409-1-40-4-M6)
1
AS-SF1-RF_40-4-M6
40 mm
Tool flange adapter
(assembly pattern as specified by ISO 9409-1-40-4-M6)
1
AS-SF1-TF_40-4-M6
M4x20 countersunk screw DIN 7991
3
2300026
Each AIRSKIN® Safetyflange is additionally supplied with the following components:
• AIRSKIN® Connection Box (see
• External cables
• Manual
Risk of suffocation for children!
Keep packaging films out of the reach of children. Ensure eco-friendly disposal of pack-
aging materials!
1
When delivered, the AIRSKIN® Safetyflange is preconfigured with Spring 2 (for
2
.
5
-
5 kg
payload).
2
The scope of delivery includes the robot adapter plate that is supplied for the specific customer.
3
The scope of delivery includes the tool flange adapter plate that is supplied for the specific customer.