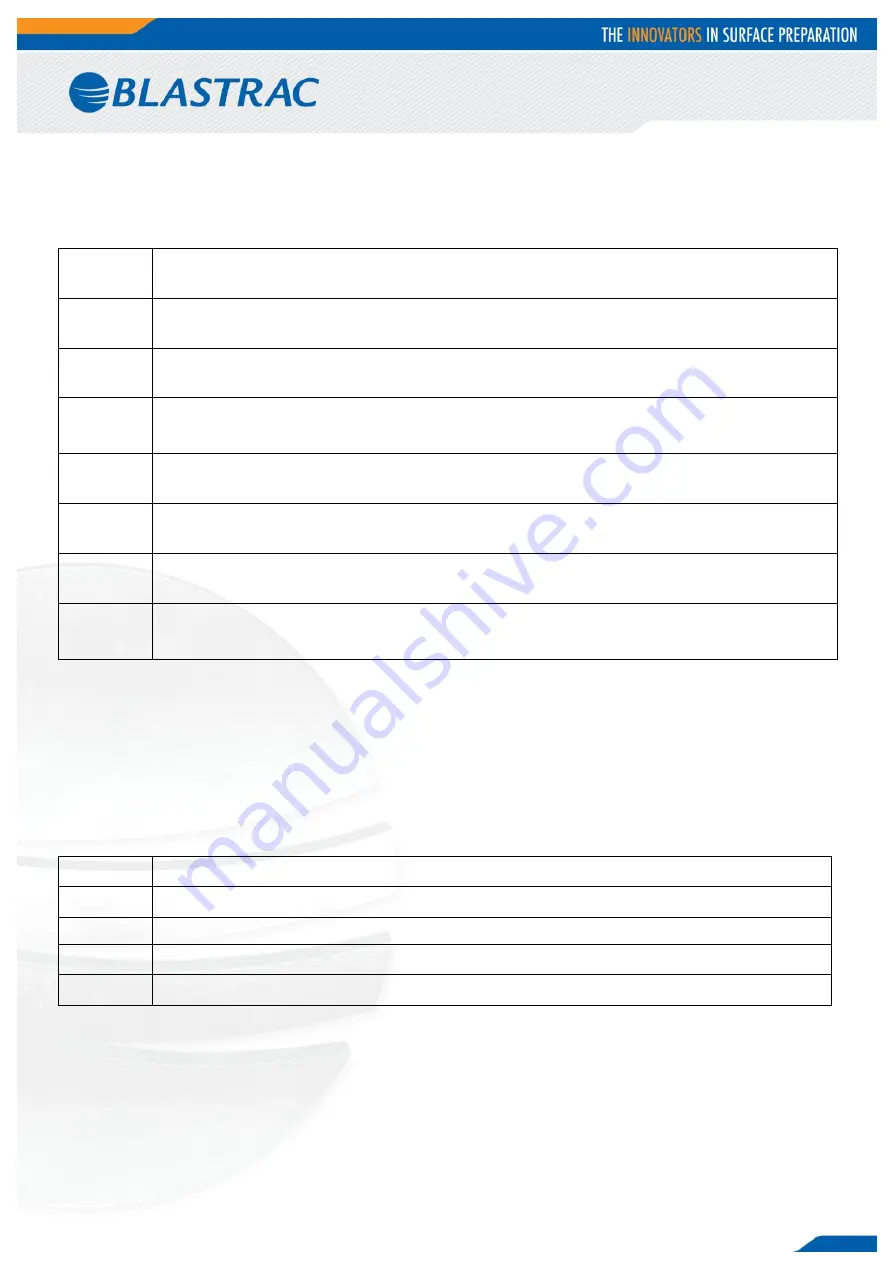
39
9.
Storing the machine for a lengthy period
Take the following measures if you intend to take the machine out of service for a lengthy period (3-12
months):
Step
Activity
1
Drain the fuel tank until it is nearly empty and fill with FAME*-free fuel. Operate the engine for a
few minutes so that only FAME-free fuel is still in the fuel system.
2
Change the engine oil and oil filter (Consult Hatz manual)
3
Change the fuel filter (Consult Hatz manual)
4
Let the machine cool down.
5
Remove the battery and store at ambient temperature. Comply with the local regulations as well
as the regulations of the battery manufacturer for the storage of batteries.
6
Close and seal all engine openings (air intake openings, air outlet openings and the exhaust gas
opening) so that no foreign bodies can enter, but a small amount of air can still be exchanged.
This avoids condensation.
7
After the machine has cooled down, cover it to protect it against
dust and store it in a dry and clean place.
*FAME = Fatty Acid Methyl Ester
Ambient conditions during storage
▪ Max. permissible storage temperature: -25 °C to +60 °C
▪ Max. permissible humidity: 70%
▪ Protect the engine from direct sunlight
Recommissioning
Step
Activity
1
Remove all covers.
2
Check the cables, hoses and lines for cracks and leak tightness.
3
Check the engine oil level.
4
Install the battery.