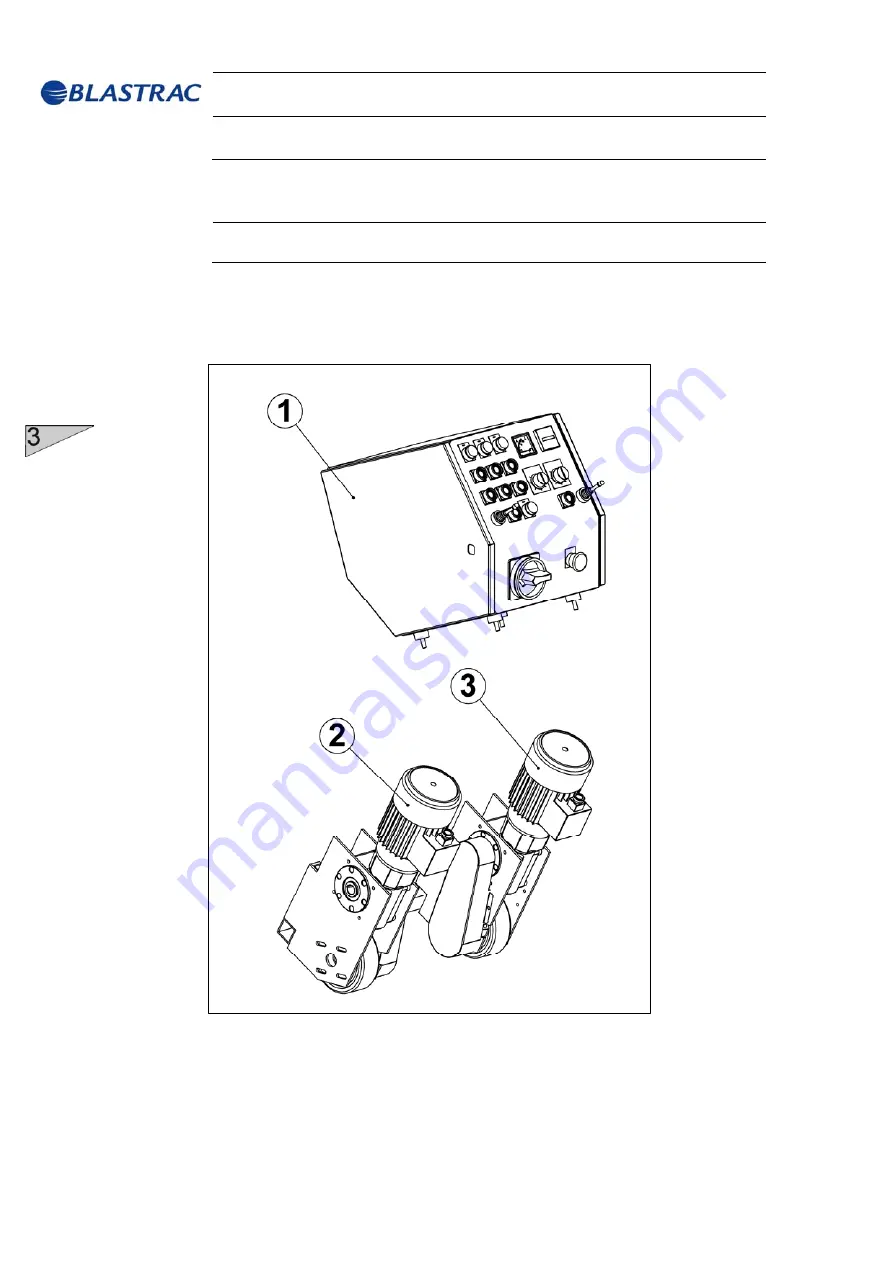
Operating Instructions
500 E Global
General
12
3.11 Drive system
The drive is an independent electric system contained within the ‘V’ of
the blast housing cabinet. There is an
On/Off
switch on the electrical
panel to operate this drive control system.
Fig. 3.8
1 Control
box
3
Drive wheel system left
4
Drive wheel system right
Summary of Contents for 500 E Global
Page 1: ...Operating Instructions 500 E Global MAN 500E Global EN REV 0...
Page 2: ......
Page 4: ......
Page 42: ...Operating Instructions 500 E Global Transport 4...
Page 50: ...Operating Instructions 500 E Global Initial operation 8...
Page 58: ...Operating Instructions 500 E Global Operation 8...
Page 72: ...Operating Instructions 500 E Global Maintenance 14...
Page 74: ...Operating Instructions EBE 500 E Electrical systems 2...
Page 75: ...500 E Global Operating Instructions Electrical systems 3 8 1 Electric circuit diagrams...
Page 76: ...Operating Instructions EBE 500 E Electrical systems 4...
Page 90: ...Operating Instructions EBE 500 E Electrical systems 18...
Page 96: ...Operating Instructions 500 E Global Fault diagnosis 6...
Page 97: ...500 E Global Operating Instructions Spare parts 1 Contents Chapter 10 10 1 Spare parts...
Page 99: ...500 E Global Operating Instructions Spare parts 3 10 1 Spare parts Fig 10 1...
Page 102: ...Operating Instructions 500 E Global Spare parts 6 Fig 10 3...
Page 106: ...Operating Instructions 500 E Global Spare parts 10...
Page 108: ...Operating Instructions 500 E Global Spare parts 12 Fig 10 7...