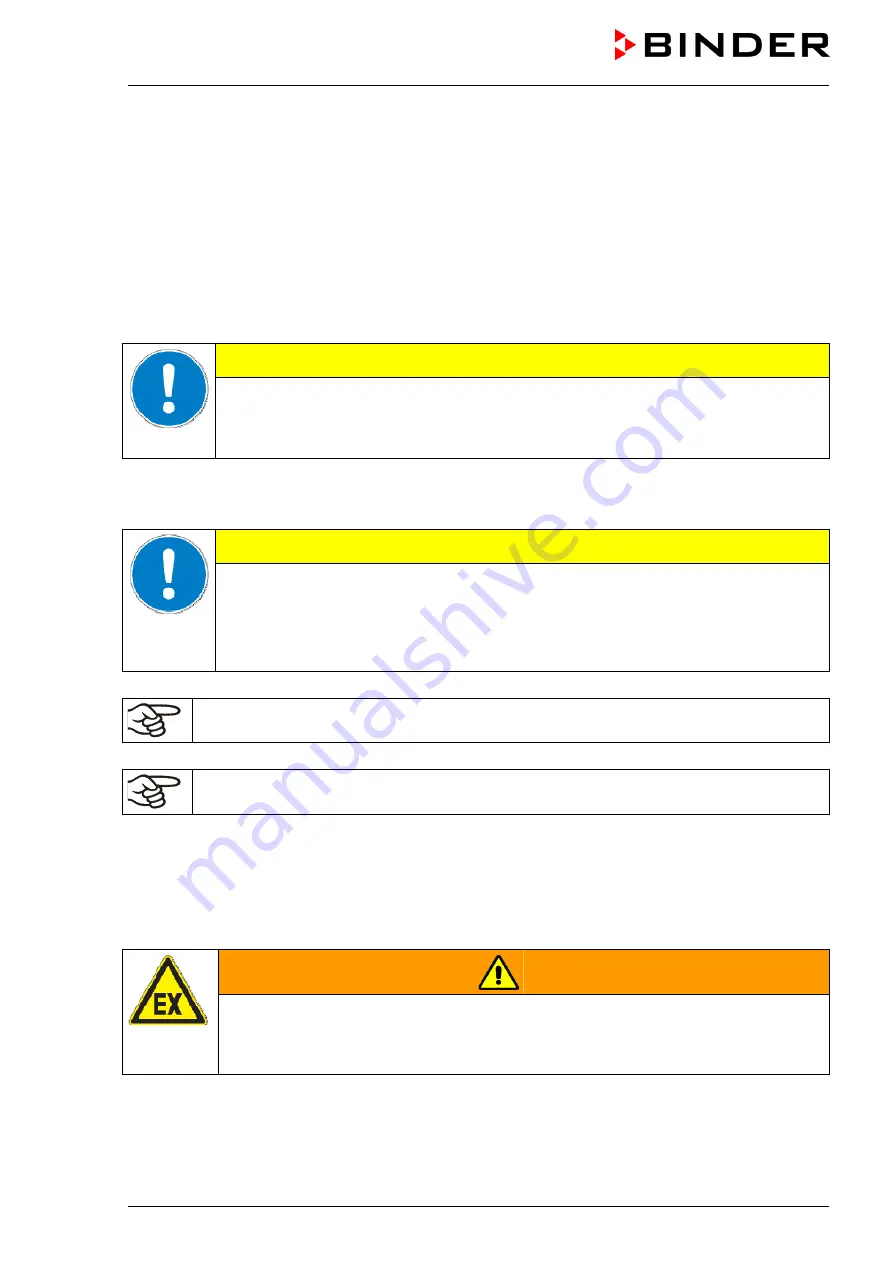
C 150 (E2) 06/2011
page 60/78
•
Sterilization phase: The temperature is maintained for 3 hours, which ensures that 180 °C /
356 °F
is
reached on all internal surfaces for at least 30 minutes.
•
A cooling-down phase follows until 37 °C /
98.6 °F
is reached
.
The precise duration of the entire sterilization cycle depends on the ambient temperature at the installa-
tion site and can thus vary. At an ambient temperature of 25 °C /
77 °F
, the total duration is approx. 12
hours. The display "
End
" in the lower controller display (Figure 35 page 62) indicates the end of the ster-
ilization procedure. You can shorten the cooling-down time by aborting the sterilization cycle (chap. 15.5)
during the cooling-down phase, i.e. no sooner than after 6 hours.
During sterilization, the CO
2
valve is closed and the CO
2
controller turns off entirely.
The CO
2
sensor is temperature resistant up to a maximum temperature of 60 °C /
140 °F.
CAUTION
Excess temperature.
Damage to the CO
2
sensor.
∅
Do NOT expose the CO
2
sensor to hot-air sterilization.
The CO
2
sensor head was especially adjusted for your specific chamber. To avoid confusion, an adhe-
sive label with a serial number is adhered to the sensor head. When exchanging the sensor, repeat CO
2
control adjustment.
CAUTION
Different CO
2
sensor.
Invalid calibration.
∅
Do NOT change the CO
2
sensor head.
¾
Write to down the serial number of the CO
2
sensor.
The safety controller settings are inactive during sterilization. They become functional again
following abortion of the sterilization and/or restart of the unit at the main power switch.
Before carrying out the first hot-air sterilization, remove any protective lamination sheet from
the inner metal surfaces.
Procedure for hot-air sterilization:
•
Turn off the unit
•
Pull out the sensor
•
Empty the water pan.
WARNING
Danger of implosion.
Damage to the unit.
¾
Empty the water pan before starting the hot-air sterilization.
•
Clean the C 150.
•
Water pan and shelves must be inside the incubator, the water pan at its usual place on the bottom.
•
Close the inner glass door and the outer unit door.
•
Turn on the unit.
Summary of Contents for APT.line C 150
Page 75: ...C 150 E2 06 2011 page 75 78 18 9 Dimensions C 150...
Page 79: ......