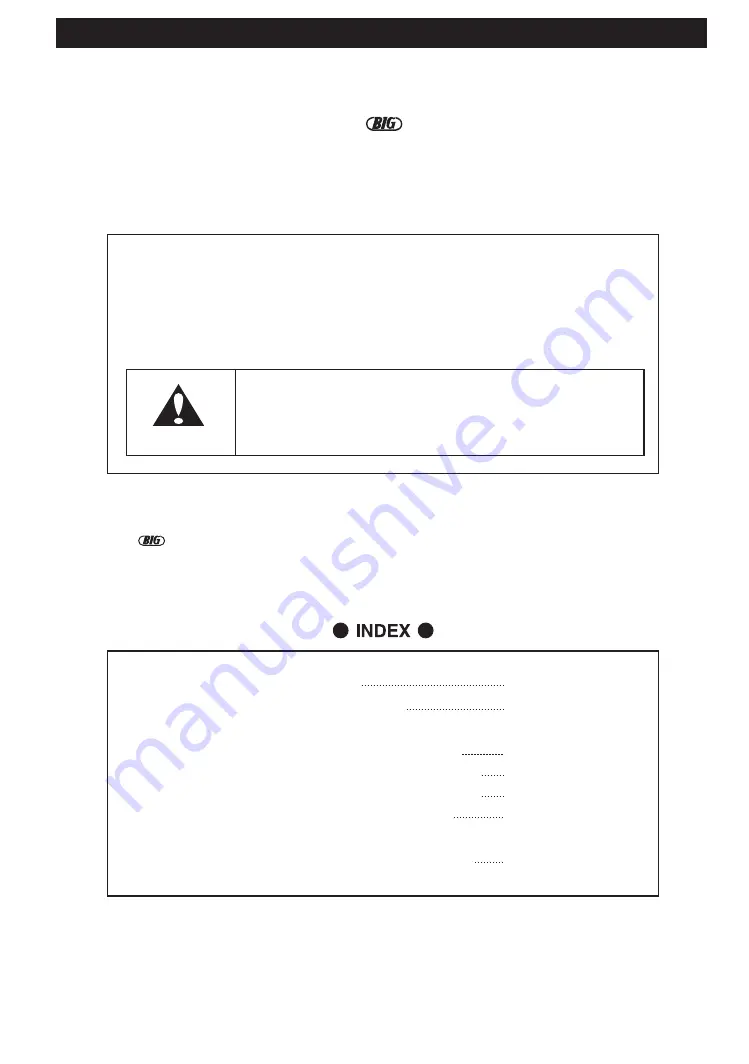
Thank you for purchasing the ANGLE HEAD.
Please read these instructions before use and keep them where
the operator may refer to them whenever necessary.
Caution
Regarding the safety
INSTALLATION & OPERATING INSTRUCTIONS FOR ANGLE HEAD
1
■
SPECIFICATIONS
■
OPERATION SEQUENCE
■
OPERATION PROCEDURES
1. How to adjust the cutter angle
2. How to check the cutter direction
3. How to adjust the cutter direction
4. Installation of the cutting tool
■
OTHER
1. Coolant feed to the cutting edge
P 2
P 3
P 4
P 8
P 9
P11
P12
ANGLE HEAD
The following indicator is used in the operation manual to signify points
relating to safe operation. Please ensure these points are fully understood
and followed correctly.
The Angle Head contributes to efficient machining by reducing setup times and
production processes, allowing automatic tool change and full adjustment of the cutter head
direction.
Should this equipment be incorrectly operated injury is possible
to the operator, or other personnel in the area. Equipment may
also be damaged.