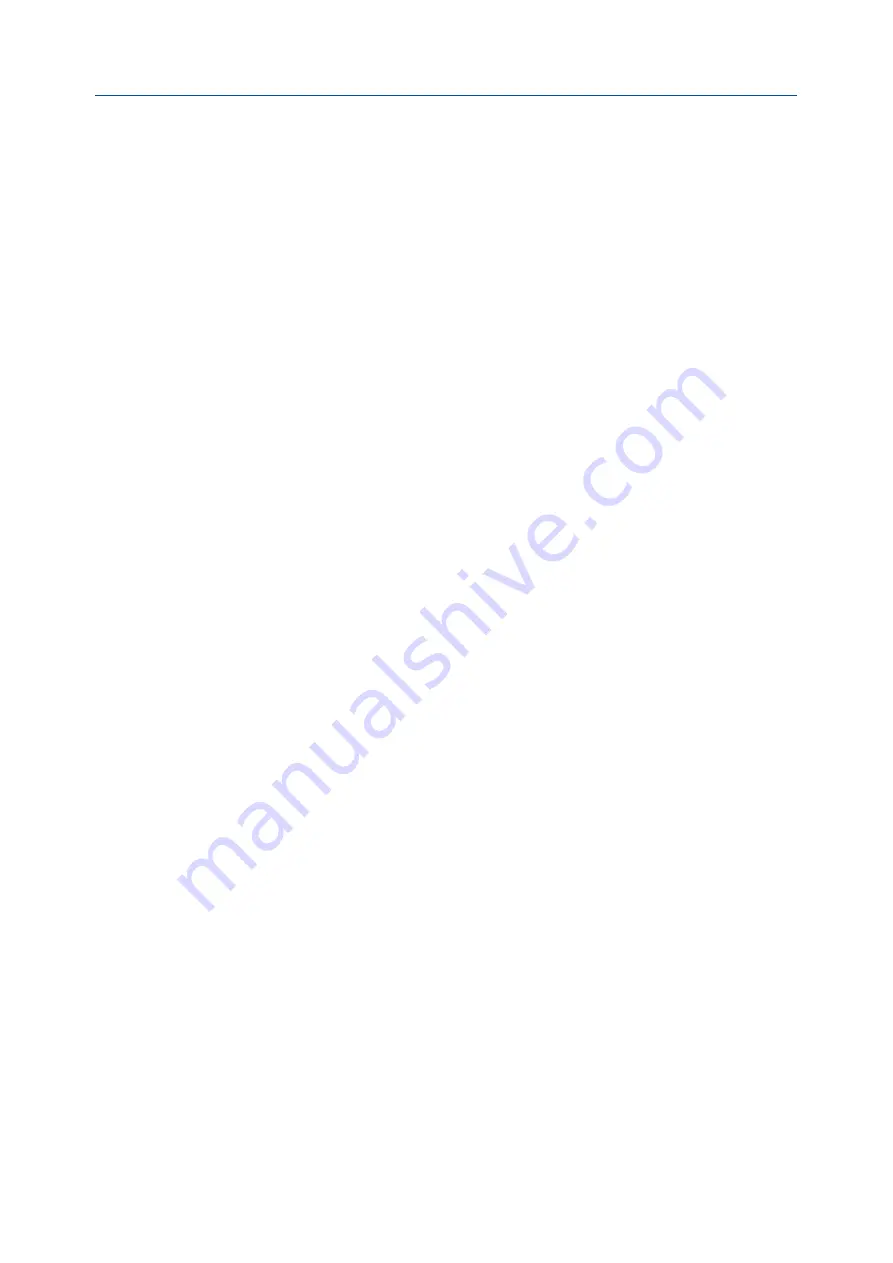
37
Installation, Operation and Maintenance Manual
MAN 607 Rev. 6
February 2022
Section 5: Maintenance
Maintenance
Seals replacement
Prior to reassemble check that the actuator components are in good condition and is clean.
Lubricate all the surfaces of the parts, which move in contact with other components,
by recommended oil
(SHELL OMALA S4 WE 320 or equivalent)
. If the O-ring must be
replaced, remove the existing one from its groove, clean the groove carefully and lubricate
it with protective oil film. Assemble the new O-ring into its groove and lubricate it with a
protective oil film.
1.
Replace the O-ring (3) of the head flange (2).
2.
Replace the O-ring (3) of the end flange (13).
For replacement of piston rod seal ring (4) and of the O-ring (5), proceed as follows:
1.
Remove the existing Teflon seal ring (4) with its O-ring from their groove.
2.
Clean the groove carefully and lubricate it with a protective oil film.
3.
Assemble the new O-ring into its groove and lubricate it with a protective oil film.
4.
Assemble the new Teflon seal ring (4) into the flange groove,on the rubber
O-ring (5), by bending it; take care that the bending radius is as large as possible
to avoid damaging the seal. Then, enlarge the seal ring with your fingers so as to
restore its round shape; pay attention not to utilize any tools which can damage
the seal ring.
To replace the piston dual-seal ring (9), proceed as follows:
1.
Remove the existing dual-seal ring (9) with its O-ring from its groove.
2.
Clean the groove carefully and lubricate it with a protective oil film.
3.
Assemble the new dual-seal ring (9) by introducing one side of it into the groove
and then enlarge it with your fingers so as to introduce it into the groove: take
care to enlarge it uniformly without any tools which could possibly damage it. The
elastic memory of the kind of Teflon type the seal ring is made of allows the ring to
shrink back to its previous dimension after a short time.
If the O-ring (17) has to be replaced, measure the protrusion of the stop screw (11) with
reference to the end flange (13) surface, so as to be able to easily restore the setting of the
actuator mechanical stop in the open valve position, once the maintenance procedures
have been completed.
4.
Loosen the protection cover (14) and unscrew the stop screw (11) until it
is removed.
5.
Replace the O-ring (17) from the stop screw cover (14).
6.
Screw the stop screw into the threaded hole of the end flange until it reaches its
original position (the same protrusion with reference to the flange surface).
7.
Tighten the protection cover (14).