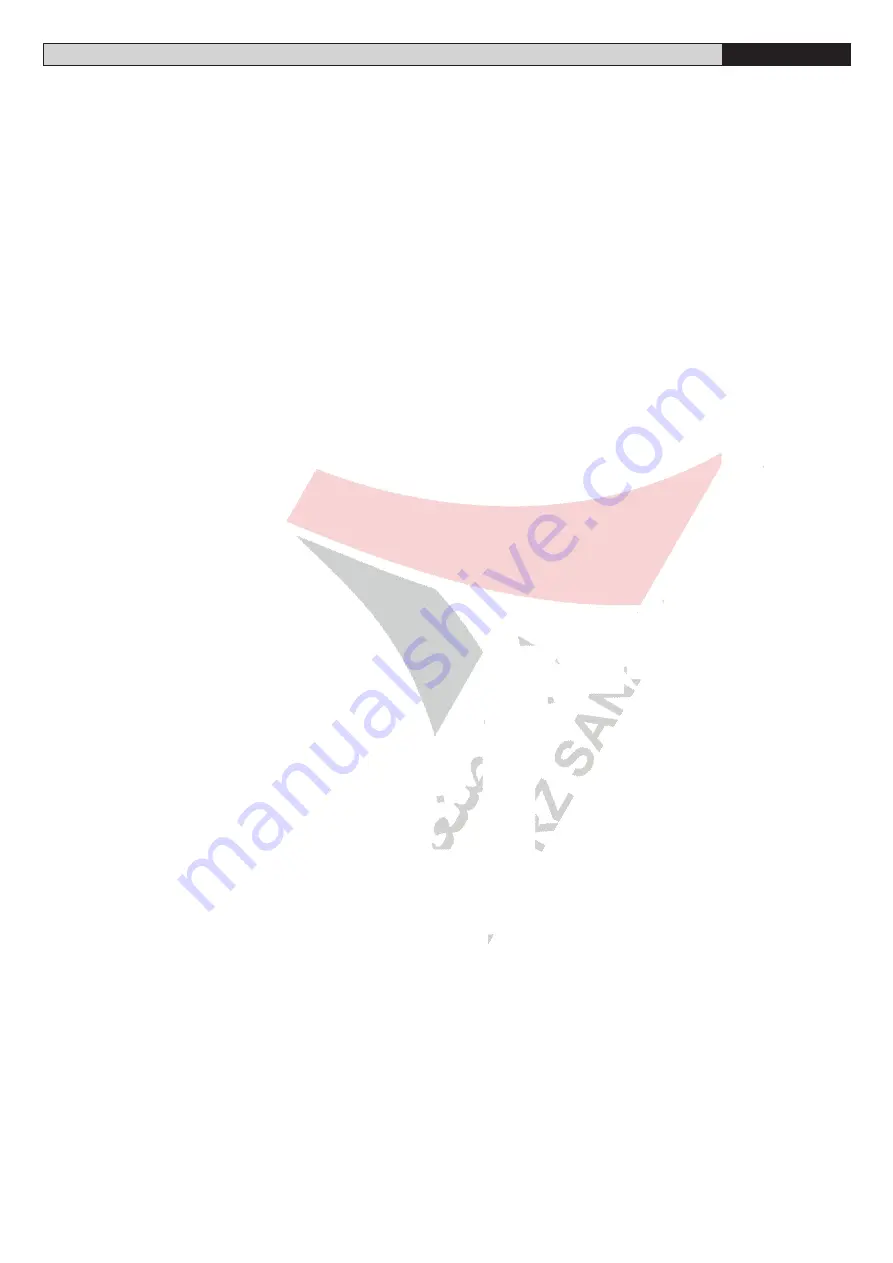
The crossing point between value 1,97 and boom length equal to 4,0 is within
the “A” area of MOOVI 50 graph. “A” hooking point will therefore be suitable
for correct boom balancing.
Calibrate the spring as described in paragraph 7.
WARNING!:
The securing points marked with A and B can be used with MOOVI 50
only.
The securing point marked with C can be used with MOOVI 30MM only.
If the point found is within the crossed area that means that installation is
not possible and it is necessary to shorten the boom or reduce the number
of accessories.
If no accessory is used, only use the weight of the “PA” boom to find the
securing point.
7) BAR BALANCING
(Fig.9)
- Activate the emergency release (fig.14).
- Position the bar at about 45° (fig.9). The bar must remain still.
- If the bar tends to open, unload the spring by operating on the “T” tie
rod.
- If the bar tends to close, load the spring by operating on the “T” tie rod.
- In both cases, load or unload the spring until the bar remains still at about 45°.
- Reset the motorised operation by rotating the release key to the opposi-te
direction (fig.14).
WARNING!
During the closing operation, the balancing spring must never
be reduced to a pack (be totally compressed). Fig.9 indicates the position
where the minimum value of the compressed spring is measured with the
rod in the opening (vertical bar) position.
8) ELECTRICAL INSTALLATION SET-UP
WARNING: before opening the door, make sure that the spring has
been unloaded (rod at 43°).
Set up the electrical installation (fig. 10) with
reference to the current regu-lations for electrical installations CEI64-8,
IEC364, in conformity with HD384 and other national standards. Keep the
mains power supply con-nections definitely separate from the service con-
nections (photocells, elec-tric edges, control devices etc.).
Warning! For connection to the mains, use a multipolar cable having
minimum 3x1.5mm
2
cross section and complying with the previously
mentioned regulations (for example, if the cable is not protected, it must
be at least equal to H07 RN-F, whereas if it is protected it must be at
least equal to H07 VV-F with a 3x1.5 sq mm
2
cross section).
Connect the control and safety devices in conformity with the previously
mentioned installation standards. Fig.10 shows the number of connections
and section for a 100m length of power supply cables; for greater lengths,
calculate the section for the true automation load. When the auxiliary con-
nections exceed 50-metre lengths or go through critical disturbance areas,
it is recommended to decouple the control and safety devices by means of
suitable relays.
The main automation components are (fig.10):
I)
Type-approved adequately rated omnipolar circuit-breaker with at least
3,5
mm contact opening, provided with protection against overloads
and short circuits, suitable for cutting out automation from the mains.
Place, if not al ready installed, a type-approved differential switch
with a 0.03A threshold just before the automation system.
QR)
Control panel and incorporated receiver.
S)
Key selector.
AL)
Blinker with tuned antenna.
M)
Actuators.
A)
Bar.
F)
Rest fork.
CS)
Electric edge.
CC)
Edge control.
Ft,Fr)
Pair of photocells.
CF)
Photocell post.
T)
1-2-4 channel transmitter.
9) TERMINAL BOARD CONNECTIONS
WARNING: before opening the door, make sure that the spring has been
unloaded (rod at 43°).
First pass the appropriate electric cables through the
raceways and fix the various automation components to the chosen points,
then connect them following the directions and diagrams contained in the
control unit instruction manual. Carry out phase, neutral and (compulsory)
earth connections. The protection wire (earth) with yellow/green insulating
sheath must be connected to the appropriate terminals marked by their symbol.
It is absolutely necessary to avoid operating the automation system without
adequate protection. This can jeopardise personal and product safety. In no
circumstances must the automation system be activated before carrying out
all connections and checking the efficiency of all safety devices.
Keep the low voltage connections definitely separated from the power supply
connections.
JP2
1-2
Power supply 230V
~
+/- 10% 50 Hz (Neutral wire to terminal 1).
3-4-5 M motor connection (terminal 4 common wire, terminals 3-5 motor
and capacitor operation).
1-4
Blinker connection 230V
JP1
7-8
Open-close push button and key selector (N.O.).
7-9
Stop button (N.O.). If not used, leave jumped.
7-10 Photocell or pneumatic edge input (N.C.). If not used, leave brid-
ged.
7-11 Opening limit switch (N.C.).
7-12 Closing limit switch (N.C.).
13-14 24 V
~
power supply output for photocell and additional devices.
15-16 Second radio channel output of the double-channel receiver board
(N.O.)
17-18 Antenna input for radio-receiver board (18 braid - 17 signal).
CON1
Radio-receiver board connector, 1-2 channels.
9.1) LED
(Fig.16)
The
ALPHA-BOM
control unit is provided with a series of self-diagnosis
leds which control all the functions.
The functions of the LEDs are the following:
(LD1 on - LD2 off) - Barrier opening.
(LD1 off - LD2 off) - Barrier stop.
(LD1 on - LD2 on) - Barrier closing.
LD3 Start - goes on when a start command is given.
LD4 Closing limit switch - goes off when the closing limit switch is ope-
rated.
LD5 Opening limit switch - goes off when the opening limit switch is
operated.
LD6 Photocell - goes off when the photocells are not aligned or in the
presence of obstacles.
LD7 Stop - goes off when a stop command is given.
9.2) FUNCTIONING LOGIC
4-step logic: (Dip-Fix IBL ON)
The following actions take place after a start command:
closed barrier: .................................................................................... opens
opening: ............................. stops and operates the TCA (Dip-Fix TCA ON)
open barrier: ..................................................................................... closes
closing: .................................. stops (stops and does not operate the TCA)
after the stop: ..................................................................................... opens
With Dip-Fix IBL ON, any start command given during opening has no ef-
fect.
9.3) DIP-FIX SELECTION
(Fig.16)
TCA
Automatic closing time TCA.
ON:
Automatic closing on.
OFF: Automatic closing off.
IBL
Blocks impulses.
ON:
START commands are not accepted during the opening phase.
OFF: START commands are accepted during the opening phase.
FCH
Photocells.
ON:
Photocells are only active in the closing phase. If an object is detected
by the photocells during the closing phase, the gate reverses the
current movement.
OFF: Photocells are active both in the closing and opening phase. If an
object is detected by the photocells on closing or opening, the gate
stops; once the object has been removed, the gate opens.
9.4) TRIMMER ADJUSTMENT
(Fig.16)
TCA (Dip-Fix TCA ON)
It is used to set the automatic closing time, after which the gate closes
automatically (adjustable from 0 to 90 sec.).
TW
It is used to set the motor working time, after which the motor stop (adjustable
from 0 to 30 sec.). When using electrical limit switches, increase the motor
stopping time by a few seconds with respect to the leaf closing time.
9.5) ACCESSORIES
SS
(fig.16).
Optional board signalling gate open. Operates only with electrical limit
switches.
INSTALLATION MANUAL
ENGLISH
MOOVI 30-50 Ver. 06
-
15
D811386_06
P:15