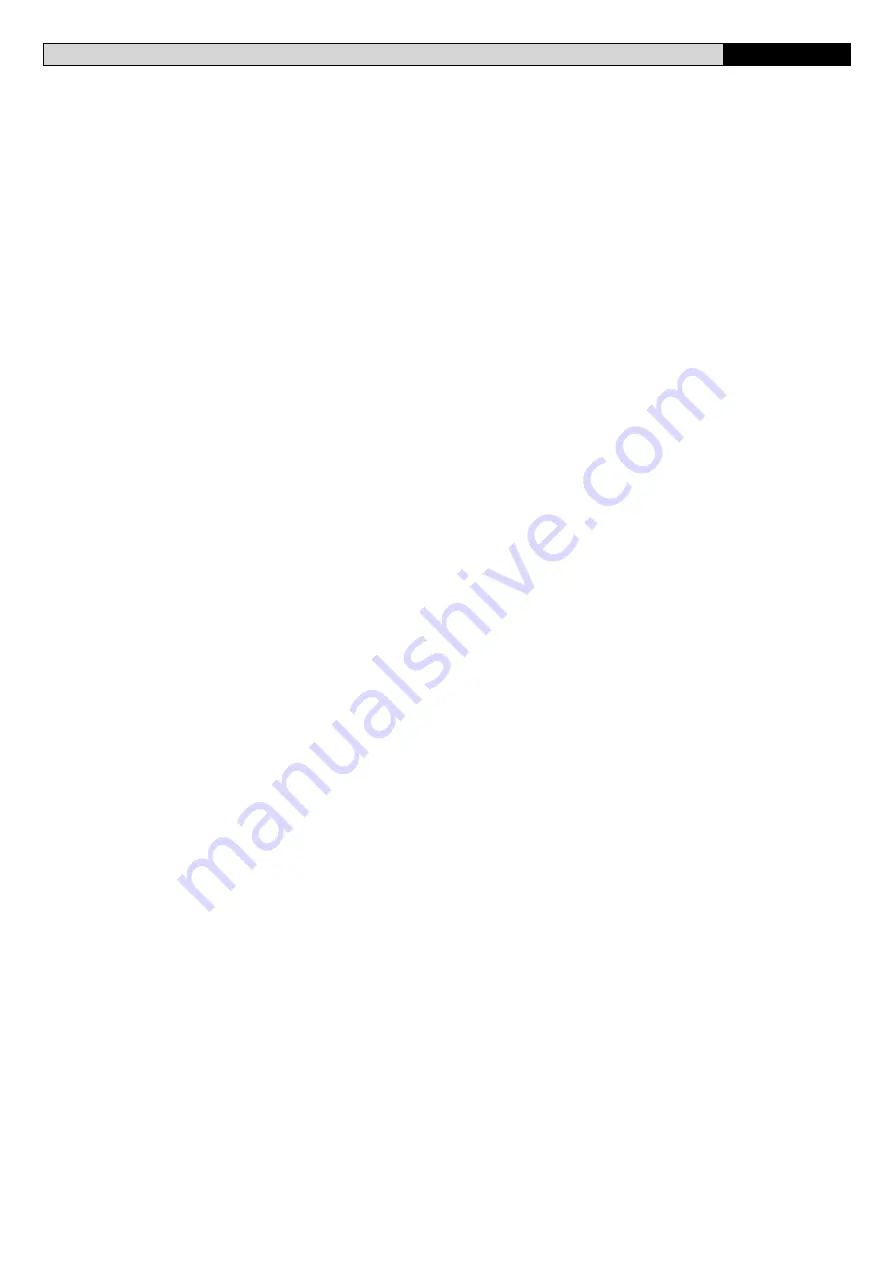
LOOP 50 / 50M - Ver. 04
-
9
D811443_04
c) Insert the operator in the winding tube, and centre any inside tube welding
with the undercut existing both in wheel “C” and ring nut “G”.
If necessary, eliminate any imperfection or cutting burrs which prevent
free coupling.
d)
WARNING!
In the case of a round winding tube, measure riveting distance
“T” of the pulling wheel (fig. 5-ref. ”C”) before fixing it by means of rivets
/ screws.
e) Fit the support system chosen, with reference to Fig.5.
WARNING!
Accurately check that the roller is parallel and perpendicular
to the shutter panel.
5.4)
Manual manoeuvre
Various types of installation are available using the accessories. The most
common ones are illustrated in Fig. 6b:
1) Eye for manual manoeuvre positioned under the box
2) 90° Universal joint installed on the front panel of the box
3) 45° Universal joint installed under the box
5.5) Electrical installation setup
Lay out the electrical installation with reference to the CEI in force for
electrical installation.
WARNING!
For connection to the mains, use a multipolar cable having
a minimum cross section of 3x1.5 sq mm and complying with the current
standards. For example, if the cable is fitted outside (in the open) it must be
at least equal to H07RN-F, whereas if it is inside (in a raceway) it must be at
least equal to H07VV-F, and have a section of 3x1.5 sq mm.
In the case where the control units used are preset for serial control, the
telephone line must be kept totally separate from the mains power supply
(separate raceways).
For the
HOLD-TO-RUN
control device, use an omnipolar commutator (10A-
250V) having a three-position button and direction arrows.
The connection is illustrated in fig.8.
For other control devices, consult the relevant instruction manuals.
WARNING!
Do not control more than one automation device with the
same
commutator. Should other control devices be adopted, these must be
fitted
in observance of the current safety standards.
WARNING!
When the power supply cable is damaged, it must be replaced
by the manufacturer or its technical assistance service, or else by a person
having similar qualification, in order to prevent any risk.
6) END-OF-STROKE ADJUSTMENT
6.1) Warning
• In order to avoid any risks during the end-of-stroke adjustment procedure, it
is
indispensable
that the motor-driven tube can be stopped at any time.
• It is recommended to use an the special key to adjust the end-ofstroke
points.
• Do not fit any caps or small stop squares to the end blade of the winding
tube.
6.2)
Preliminary information
IMPORTANT:
product warranty is not valid in case of malfunction or failure
due to noncompliance with installation instructions or servicing performed
by nonauthorized technicians. If the power cable is damaged, it must be
replaced by the Manufacturer or Manufacturer’s After-Sales Technicians to
avoid further damages.
Fit the tubular motor into the rolling tube and check with the plate on the limit
switch unit (see fig.7). Arrows 1 and 2 indicate directions of rotation of the
rolling tube. Adjusting screw A is for direction of rotation 1, whereas adjusting
screw B is for direction of rotation 2.
By turning the adjustment screw A towards the “+” sign the number of mo-
tor/winding tube revolutions in the direction shown by arrow 1 will increase
while, on the other hand, by turning the adjustment screw towards the “-” sign
the number of revolutions in the direction shown by arrow 1 will decrease.
By turning the screw B towards the “+” sign the number of motor/winding
tube revolutions in the direction shown by arrow 2 will increase while, on the
other hand, by turning the adjustment screw towards the “-” sign the number
of revolutions in the direction shown by arrow 2 will decrease.
6.3) Sunshades
During the installation of sunshades, it is advisable to adjust the stop points
with a reasonable margin of safety, which takes into account any changes
in the shutter panel dimensions due to various atmospheric factors (heat,
humidity etc.).
Carry out a check after a few days of operation in order to correct any slack
in the fabric.
Use automatic closing systems in case of strong wind (anemometer) in order
to avoid any damage to the operator.
7) AUTOMATION CHECK
Before the automation device finally becomes operational, scrupulously
check the following conditions:
• Check that all the components are securely fixed. Check that the power
supply cable is not in contact with rotating components and cannot be
caught into moving components.
• Check that the roller shutter rolls up correctly in the winding tube.
• Check that all safety and control devices, if fitted, operate correctly.
WARNING
! Efficient actuator operation is only ensured when the data stated
in the present manual are respected. The Company is not to be held
responsible for any damage resulting from failure to observe correct technical,
safety and installation standards
8) AUTOMATION CONTROL
There are different types of controls (manual, radio control, etc.) depending
on the installation requirements and characteristics.
For the various control systems, see the relevant instructions.
The installer undertakes to instruct the user on correct automation use, also
pointing out the operations required in case of emergency.
9) MAINTENANCE
Before carrying out any maintenance to the actuator, disconnect the power
supply. When any operational malfunction if found, and not resolved, di-
sconnect the system power supply and request the assistance of a qualified
techni-cian (installer).
10) SCRAPPING
In case of scrapping, the automation devices do not entail any particular
risks or danger. Disconnect the mains power supply and discard all materials
according to current standards. The different materials should be sorted out
by type (electrical components, copper, aluminium, plastic etc.).
11) DISMANTLING
WARNING
! This operation should only be carried out by qualified personnel.
When the automation system is disassembled to be reassembled on another
site, proceed as follows:
• Disconnect the power supply from the mains.
• In the case where some of the components cannot be removed or are
damaged, they must be replaced.
WARNINGS
Correct controller operation is only ensured when the data contained
in the present manual are observed. The company is not to be held
responsible for any damage resulting from failure to observe the
installation standards
and the instructions contained in the present
manual.
The descriptions and illustrations contained in the present manual are
not binding. The Company reserves the right to make any alterations
deemed appropriate for the technical, manufacturing and commercial
improvement of the product, while leaving the essential product features
unchanged, at any time and without undertaking to update the present
publication.features unchanged, at any time and without undertaking
to update the present publication.
INSTALLATION MANUAL
ENGLISH