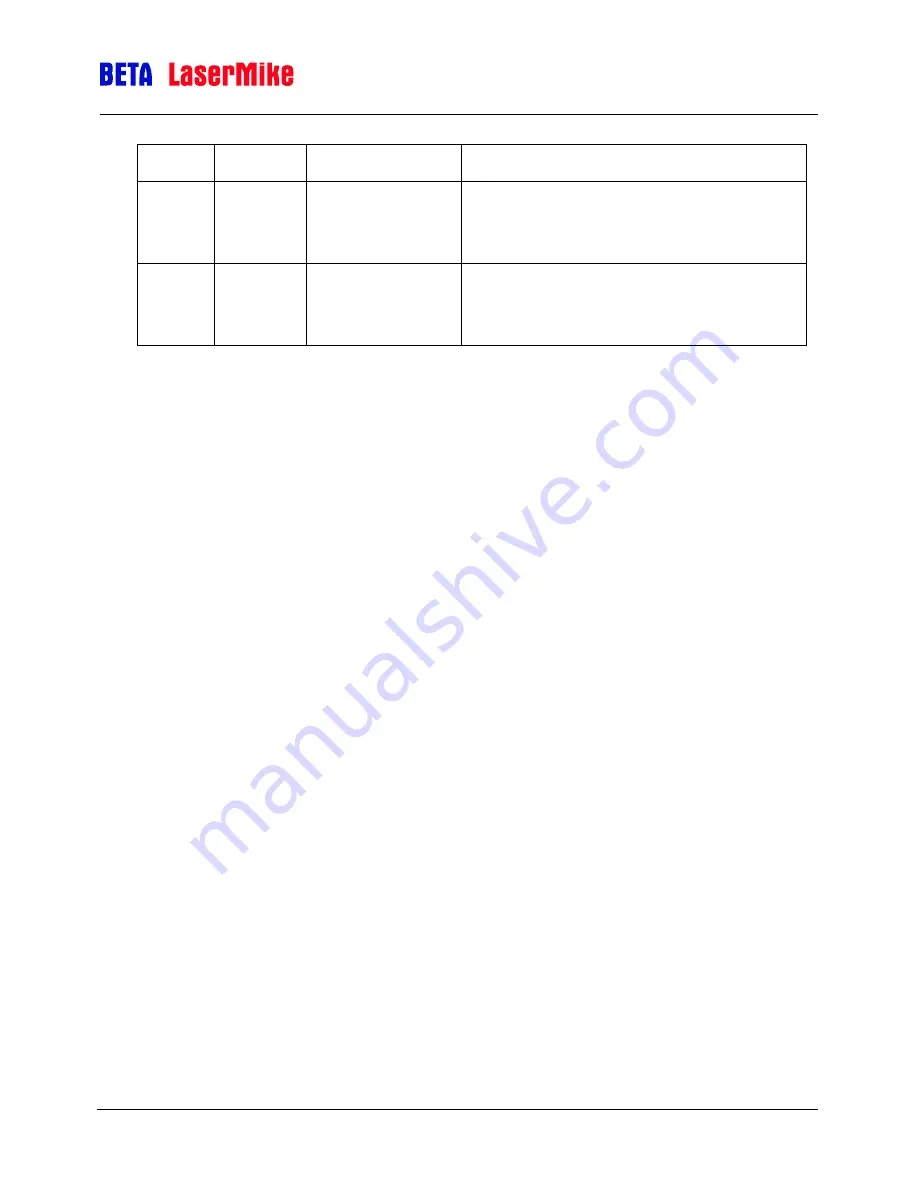
LaserSpeed 8000/9000 I/O Module Instruction Handbook
Operation
Part No. 93342 / Drawing No. 0921-01516
Page 68 of 84
Revision E (Dec 2013)
78
4.7
Reserved
8-bit byte - Don't use (set to 0)
79
4.8
User Update Rate
8-bit byte
User Update Rate Setting
Serial Command: "O"
80 (start)
↓
95 (end)
5.0 (start)
↓
5.15 (end)
Gauge Version
String (8 bit, NULL terminated char array)
Gauge Firmware String (similar to "LS9KVC"
Serial Command: "Z"