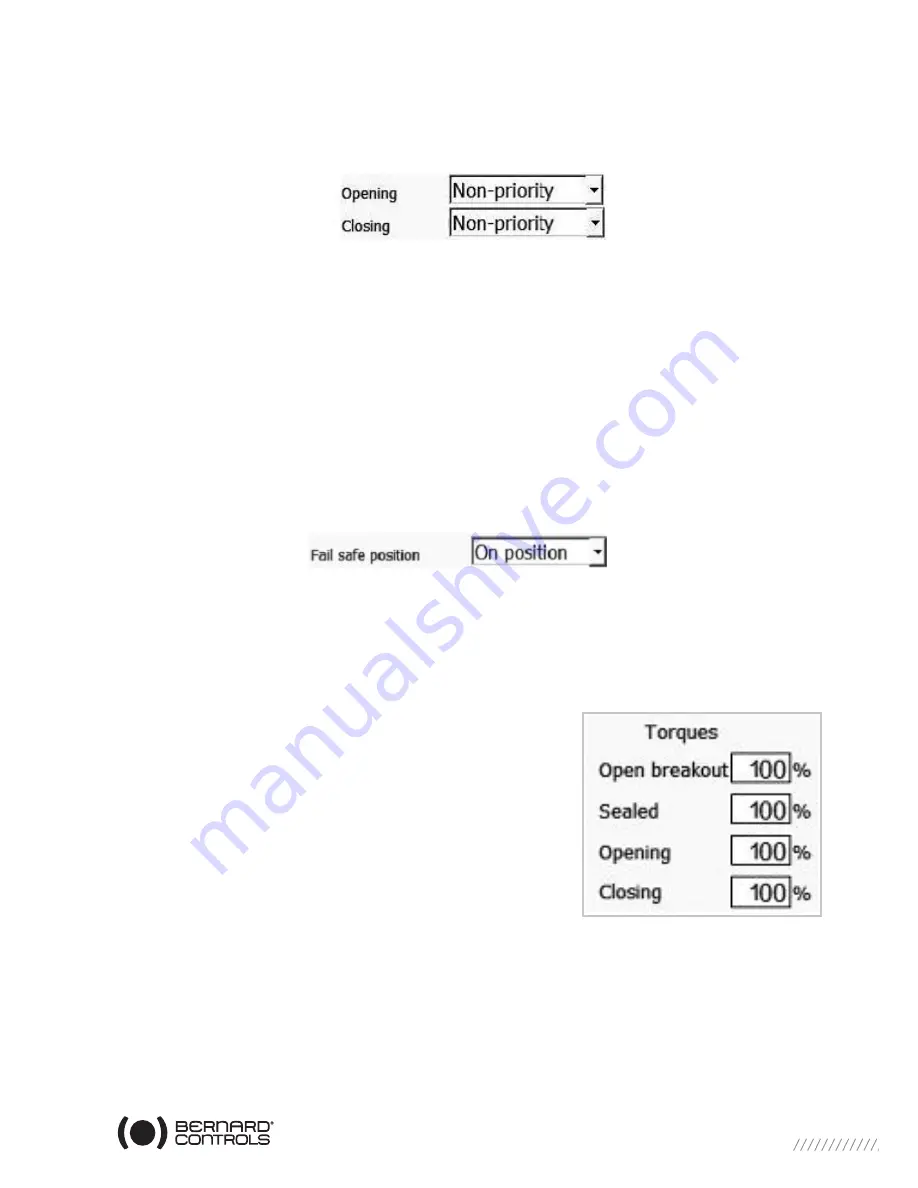
27
• PARTIAL STROKING:
This control carries out an automatic test to ensure that the actuator is still
operational. The test consists of starting the actuator over a part of its course. The starting position as
well as the percentage of movement can be set. An alarm is given off if the test has not been carried
out within a predetermined time.A priority can be selected between the opening command and the
closing command by selecting a parameter in the down-drop list of the Opening and Closing fields:
In standard there is no priority between opening and closing.
Priorities are used for:
•
Reversing the direction
of movement during operation without passing via a stop command. In
this case, a priority for opening or a priority for closing must be configured.
•
Giving priority to a direction
of rotation: If the actuator receives two simultaneous opening
and closing orders and an opening priority has been selected, the actuator will start in the opening
direction.
You can also select a fail-safe position that the actuator will reach in case of loss of communication
with the Master Station MS102, you can choose among the following positions by selecting a para-
meter in the down-drop list of the Fail safe position field:
• ON POSITION:
The actuator stays in position.
• OPENING:
The actuator runs in the opened direction.
• CLOSING:
The actuator runs in the closed position.
Finally, you can set up the maximum open breakout torque,
the maximum sealed torque, the maximum opening and
closing torque. The value must be between 40 % and 100%.
Enter the value in the appropriated field:
Note:
change the torque setting must be doing with full
knowledge for the fact.