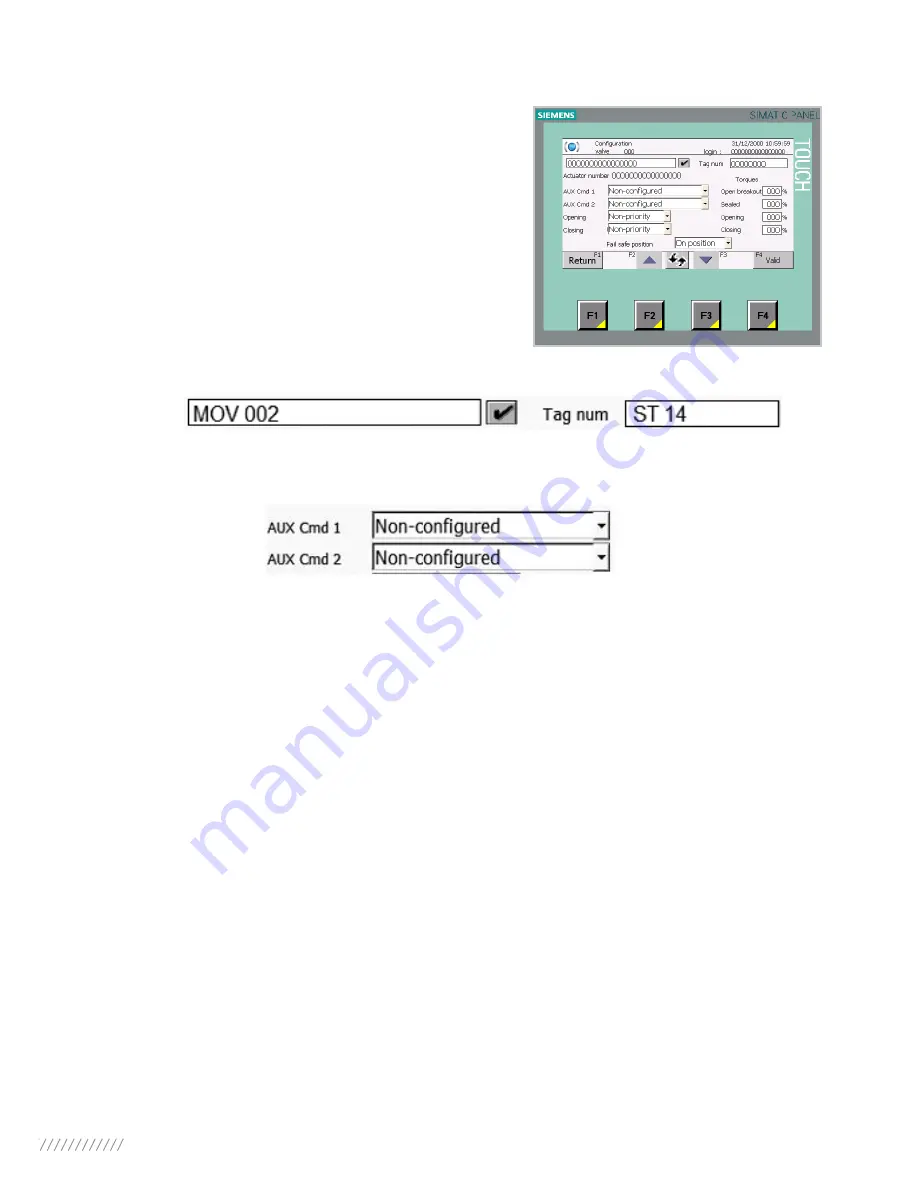
26
9.2 > CONFIGURE YOUR ACTUATOR
All users’ accounts, except Administrator account, allow
you to access to this page. But, only the Maintenance
account will be able to change the actuator configuration.
On this page you can change the Valve reference and the Tag number on these following fields:
You can allocate the auxiliaries commands to the following functions by selecting a parameter in the
down-drop list of the AUX Cmd 1 and AUX Cmd 2 fields:
• LOCAL/REMOTE:
Replace the local/remote selector on the actuator and, under remote control
conditions, authorize either local control or remote control.
• LOCAL+REMOTE/REMOTE:
This function has the same role as the previous one, but local and
remote control can be authorized simultaneously.
• PROHIBITING LOCAL CONTROL:
Prohibiting local control is controlled remotely. This function
prohibits local opening and closing controls and authorizes remote control even if the actuator
selector is placed on local control.
• PROHIBITING OPENING/CLOSING:
This control is used for preventing the actuator from star-
ting or stopping
• AUTO / ON-OFF:
For an actuator used in modulating mode with a positioning function, a com-
mand can be selected by position set-point (equivalent to the 4/20mA signal) or by opening, closing
or stop controls. The auto/on-off control is used for changing from one control mode to another.
• CLOSING / OPENING / EMERGENCY SHUTDOWN
: The ESD (Emergency Shut Down) is an
emergency remote command that has priority over the other commands. Depending on the type
of operation for which the valve is to be used, this emergency command can be opening, closing
or stopping in an intermediate position. The ESD command is assigned to a Modbus command for
auxiliary command 1 and to a wired link (separate cabling) for auxiliary command 2.
Note:
The cabled ESD has priority over the Modbus ESD. Emergency control is not possible when
the switch is in the OFF position.