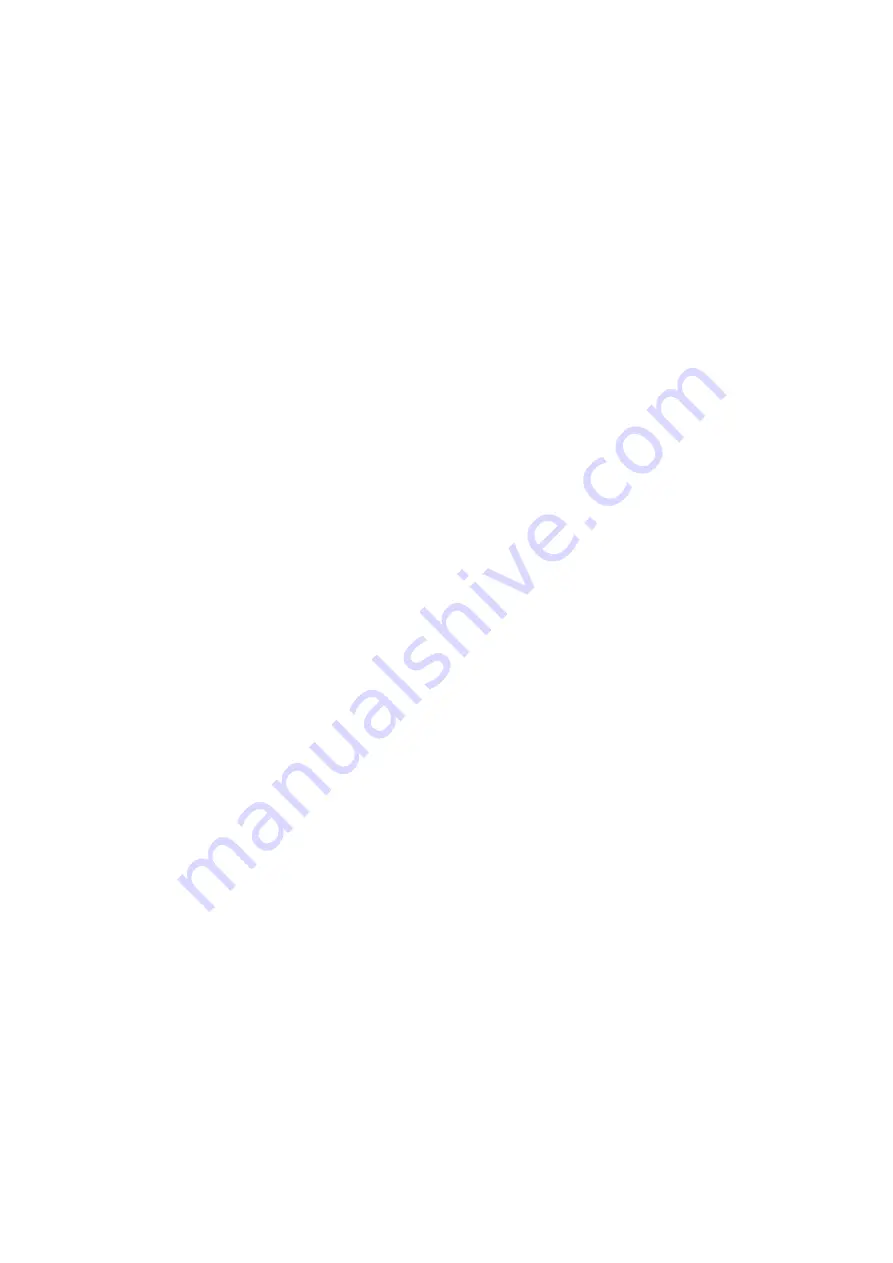
16
When the required number of break-points has
been entered, return to the linearisation sub-menu
by pressing
E
.
The indicator will display the 'Add'
or 'dEL' prompt depending upon the last sub-
function used. The indicator input current and
corresponding indicator display at each break-
point, can now be entered using the ‘in’ and ‘diSP’
sub-functions.
Using the
▲
or
▼
button select 'in' from the sub-
menu and press
P
which will reveal the first break-
point '0 : n', where n is the total number of break-
points entered. Press
P
and use the
▲
and
▼
buttons and the
P
button to move between digits,
to enter the input current at which the first break-
point is required, usually 4.000mA. When set as
required, press
E
to return to the ‘0 : n’ prompt
from which the the next break-point can be
selected using the
▲
and
▼
buttons. When the
required break-point has been selected press
P
and enter the indicator input current at which this
break-point is required. Repeat this procedure until
the indicator input current at all the break-points
has been defined and then return to the ‘in’ sub-
function by pressing the
E
button.
The corresponding indicator display at each of the
break-points can now be defined with the ‘diSP’
sub-function Using the
▲
and
▼
buttons select
the ‘diSP’ sub-function and press
P
which will
reveal the first break-point '0 : n', where n is the
total number of break-points entered. Press
P
and
use the
▲
and
▼
buttons and the
P
button to
move between digits, to enter the required
indicator display at this first break-point. When set
as required, press
E
to return to the ‘0 : n’ prompt
from which the the next break-point can be
selected using the
▲
or
▼
buttons. When the
required break-point has been selected press
P
and set the required indicator display at this
break-point.
Repeat this procedure until the indicator display at
all the break-points has been defined and then
return to the ‘SEt’ function in the configuration
menu by pressing the
E
button twice.
6.3 Lineariser error message
If an attempt is made to position a break-point at a
current which is not greater than the current of the
preceeding break-point, or at a current which is not
less than the current of the following break-point,
the error message ‘FaiL’ will be displayed. This
error message will also be displayed if an attempt
is made to position a break-point outside the
current range 3.8 to 21.0mA.
6.4 Under and over-range
The lineariser does not change the under and
over-range indication described in section 5.12.
At input currents below that specified for the first
break-point (0), the indicator will continue to use
the specified slope of the first segment. Although
not guaranteed, most indicators will continue to
function normally with an input current between
1.8mA and 4mA, at lower currents the instrument
will display ‘LPLo’ before it stops functioning.
At input currents above that specified for the last
break-point, the indicator will continue to use the
slope specified for the last lineariser segment.
6.5 Lineariser default configuration
When the lineariser is reset to the default
conditions using the ‘rSEt’ reset function described
in section 5.11, the defaults conditions are:
BA507E BA527E
BA508E BA528E
First break-point 4mA
0.0
0.00
Second break-point 20mA
100.0
100.00