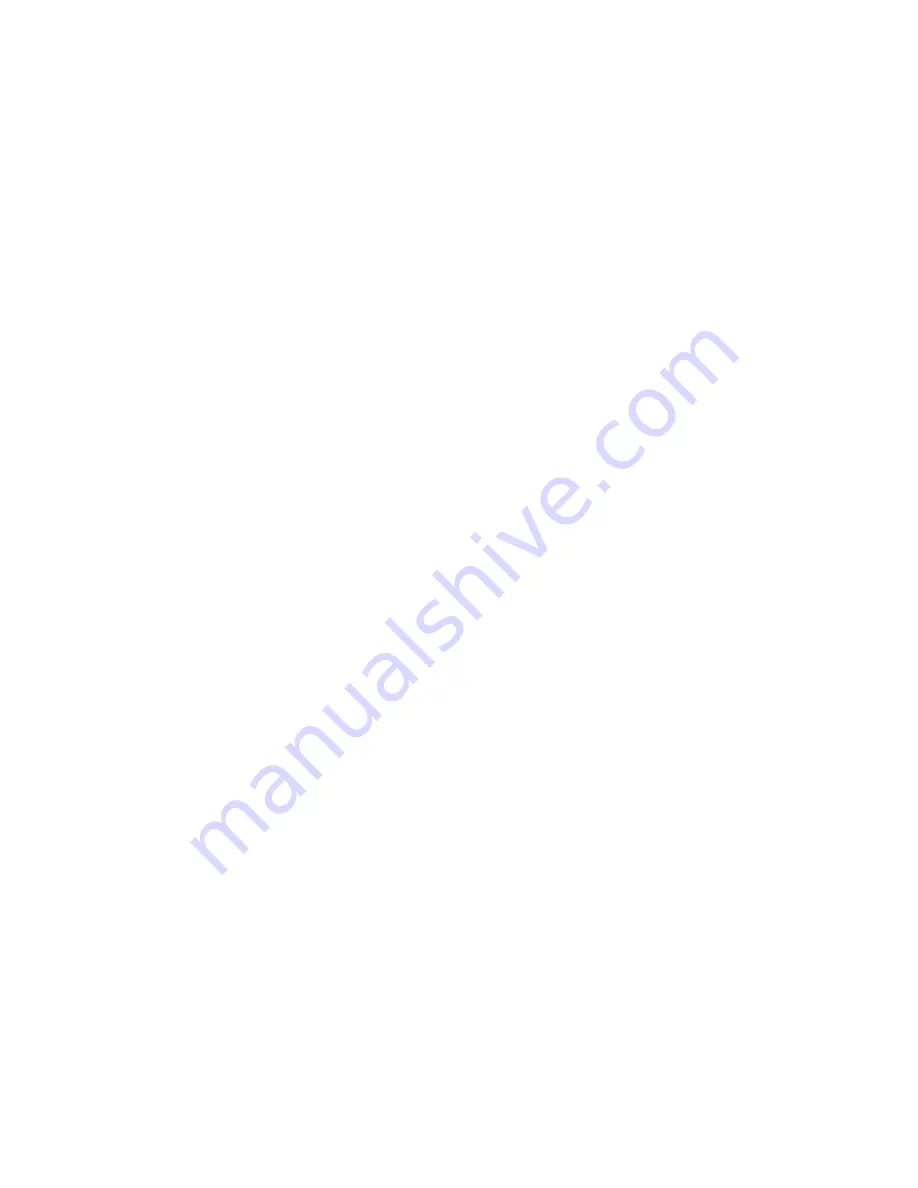
PF1352 USER MANUAL REV A 12/21/15
o
IMMediate
trigger
source will immediately go into Sweeping state after the
Trigger subsystem is initiated. A trigger command is not required to start the
event.
•
Set Trigger Delay: enter a value into the Trigger Delay text box and click the
Set
button. Use the
Get
button to query the trigger delay and display the response.
The trigger delay is the time delay between receiving a trigger and starting the event.
A trigger delay is not required to trigger an event. When the trigger source is set to
IMMediate, the trigger delay will be ignored.
•
Set Trigger Count: enter a value into the Trigger Count text box and click the
Set
button. Use the
Get
button to query the trigger count and display the response.
The trigger count is the amount of times a trigger event, including waiting for the
trigger, will be repeated. A trigger count is not required to trigger an event.
•
Select Trigger Mode: select FIX, STEP or LIST for each trigger event function
(VOLT, FREQ and CURR), and click the
Set
button for that function. Use the
Get
button to query the mode and display the response.
o
LIST: when the mode is set to LIST, define the list points in the List Commands
text box for that function. The list points should be separated by commas. Up to
ten list points can be defined. Use the
Set
button to submit the points, and the
Get
button to query and display the points.
Define the Dwell list points in the Dwell text box and click
Set
. The Dwell list
points define the time delay between the executions of each list point. Use the
Get
button to query and display the Dwell list points.
Define the list count in the List Count text box and click
Set
. Use the
Get
button
to query and display the count. The list count is the amount of times a list event,
not including the wait for trigger, will be repeated. A list count is not required to
trigger an event.
o
STEP: when the mode is set to STEP, define the step trigger value in the STEP
Commands text box for that function, and click
Set
. Use the
Get
button to query
and display the response.
o
FIX: when the mode is set to FIX, no event values need to be defined.